Multiscale.Sim EN
About Multiscale.Sim
Multiscale CAE system "Multiscale.Sim"
Multiscale.Sim is a CAE tool for multi-scale analysis that is developed by using the customized language of the multi-physics analysis tool Ansys. Multiscale.Sim provides the analysis systems that are needed for multi-scale analysis, such as macro structure analysis, localization (micro structure) analysis, and numerical material test of micro structure by the homogenization method. Multiscale.Sim uses standard features of Ansys that has a track record for many years of service as an analysis engine for mesh creation and solver. Please note that a contract of conjunction with Ansys products for this product is required since it is an add-on product to Ansys if you do not hold any Ansys product licenses.
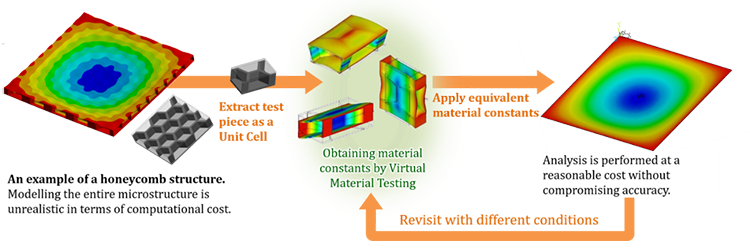
Analysis workflow of Multiscale.Sim
What is Multiscale Analysis?
The multi-scale analysis is literally the means of the analysis that will combine the behavior or the properties of both structure bodies with different scales. To put into a few words, there are various methods to approach and one of the techniques such as the homogenization method has been well known as a typical method. For example, composite materials that are used for various products in recent years consist of multiple, various materials. Supposing that the characteristics of the composite material can be homogenized, we could predict the behavior of the overall product. As a result, ideal material design is possible.
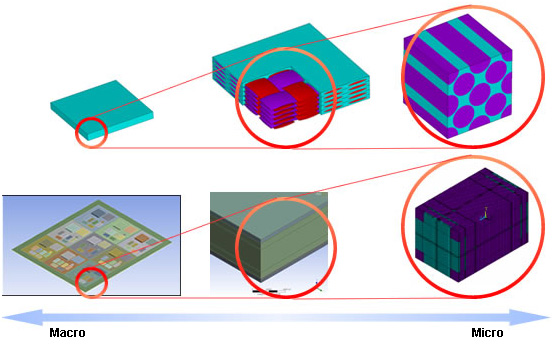
Multiscale Analysis flow
Material property values are calculated by numerical material test of micro structure without material tests that were required conventionally, by utilizing Multiscale.Sim. The results enable prediction of the macroscopic behavior by the macro structural analysis. Further, it is possible to predict the microscopic behavior by going back to the micro structure analysis again.

- Create a Micro Model
Create a micro model using 3D CAD or Ansys DesignModeler for numerical material test. - Homogenization Analysis
After mesh generation and entering the boundary conditions in Ansys, perform numerical material test and then calculate the equivalent property value such as elasticity modulus. - Macro Structure Analysis(*figure shows a printed circuit board model)
Apply the equivalent property value output from the homogenization analysis results as a material property of the macro model, then perform verification and analysis of macro model repeatedly. - Localization Analysis
Verify the behavior of the local area by selecting the element selected to be localized from the macro analysis results and perform a localization analysis using the strain of that localized area as condition.
The need for multi-scale analysis
In recent years, a composite material that has anisotropic properties and complex microstructure is used in various products. Therefore, it is necessary to grasp the material characteristics of microstructure first of all in order to understand the behavior of the overall product.
Usually, it is common to perform the material test in order to determine the material characteristics of the composite material. However, characteristics obtained from this test are actually characteristics of the macro-structure instead of the microstructure. Suppose that there is an analysis tool that could consider the characteristics at the micro-level and the macro-level such as parts model or components with different scales of the analysis model simultaneously, and will enable material design that takes advantage of the characteristics of the material inherent. In addition, there is a possibility that if the material could be on the design variables, product development can be performed with great features that did not exist before.
【 Composite Material Example 】
Laminate sheet, fiber reinforced plastic, carbon, metal matrix composites, bone, reinforced concrete, light metal
(such as aluminum, magnesium, titanium), alloys (such as stainless steel), fiber (Natural fiber, synthetic fiber,
carbon fiber), ceramics, paper, and synthetic resin.
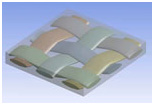
Cloth material
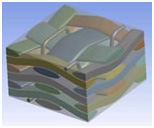
Stitch material
Utility of multi-scale analysis
Examples of utility of multi-scale analysis are shown below.
- Development of new composite materials
- Development of FRP
- Study of the cross-sectional shape of the filament
- Study of the angle of the strand
- Study of the matrix material
- Study of the crystal orientation
- Product design using composite materials
- Design of Printed circuit board
- Design of bumper
- Study for product defects in composite materials
- Study for product parts with damaged mechanisms
- Alternative to material testing
- production costs reduction of material testing
- Ideal material test
- Reduction of analysis scale
- Simplification of the model using homogeneous material
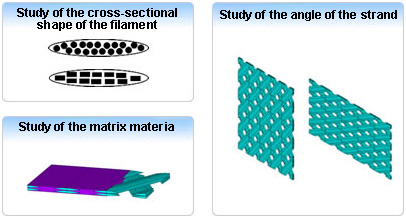
Development and Sales Framework
CAE tool "Multiscale.Sim" uses the homogenization method which is one method of multi-scale modeling, and is jointly developed by three companies, Cybernet Systems Co.,Ltd., Nitto Boseki Co.,Ltd., and Quint Corporation by receiving cooperation from Professor Kenjiro Terada of Tohoku University. The official release date was June 25, 2007.
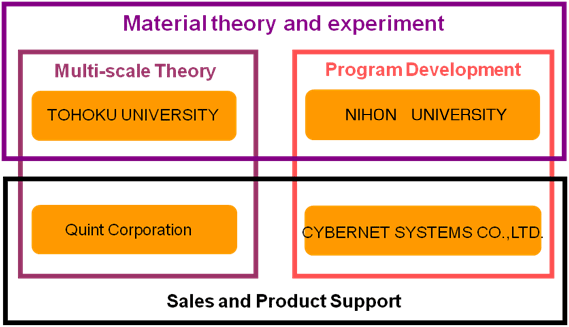
関連情報
関連する解析事例
MORE関連する資料ダウンロード
MORE-
コントローラ&センサのデータ駆動型シミュレーション
~データ駆動によるロボットのモデリングと制御設計~
-
EMCのお悩みありませんか? ~EMCソリューション~
-
炭素回収・利用・貯留におけるCO2の削減 ~Ansys Fluentによるソリューション~
~Ansys Fluentによるソリューション~
-
仮想環境で実現するマシンビジョン設計~Ansys Speosによるカメラ&照明最適化ソリューション~
~Ansys Speosによるカメラ&照明最適化ソリューション~
-
構想設計ですぐにリアルタイム検証 ~解析専任者ゼロでも使いこなせるAnsys Discovery~
~解析専任者ゼロでも使いこなせるAnsys Discovery~
-
流体機器設計の新たな一歩
~Ansys Discoveryで加速する設計改革~
-
筐体の冷却性能を構想設計から見える化 (手戻りを削減できる)
~Ansys Discoveryで始める電気筐体製品の設計改革~
-
若手でもすぐに使えるリアルタイム解析 (勘と経験からの脱却)
~Ansys Discoveryによる30名規模メーカーの設計改革~