Multiscale.Sim Journal Articles Introduction
Introduction to Composite Materials for Structural Analysts ~ Micro-Macro Analysis of Composite Materials
Prof. Norio Hirayama, College of Industrial Technology, Department of Mechanical Engineering, Nihon University.
Journal Name: CYBERNET Mechanical CAE NEWS Vol.27
Introduction
Failure strength criteria for composite material are predicted by macroscopic stress. These criterions are very useful and widely used in engineering because failure evaluation can be done with ease. However, microscopic structures in actual composite materials are arranged periodically and microscopic stress state inside them are not uniform. High stress concentration occurs at the interface between fibers and resin due to their difference in material properties. As a result, localized damage in the microscopic structure progresses and leads to macroscopic failure. To accurately predict the failure of composite materials, it is necessary to evaluate the stress in the microscopic structure. In addition, nine independent elastic coefficients must be measured to perform macroscopic analysis, even if the composite material is assumed to be orthotropic.
In this article, we will first explain the coupled analysis of microscopic and macroscopic structures based on the homogenization theory. And then the numerical material test will be explained which calculates the anisotropic material constants of composite material. This can be done by performing numerical analysis based on the homogenization method on the microscopic structure of a composite material. Then we move on to the localization analysis, which returns the results of the macroscopic structure analysis to the microscopic structure and calculates the state of the microscopic structure approximately. Finally, an example of evaluating anisotropic nonlinear material properties of composite material by nonlinear numerical material test based on the homogenization method is introduced.
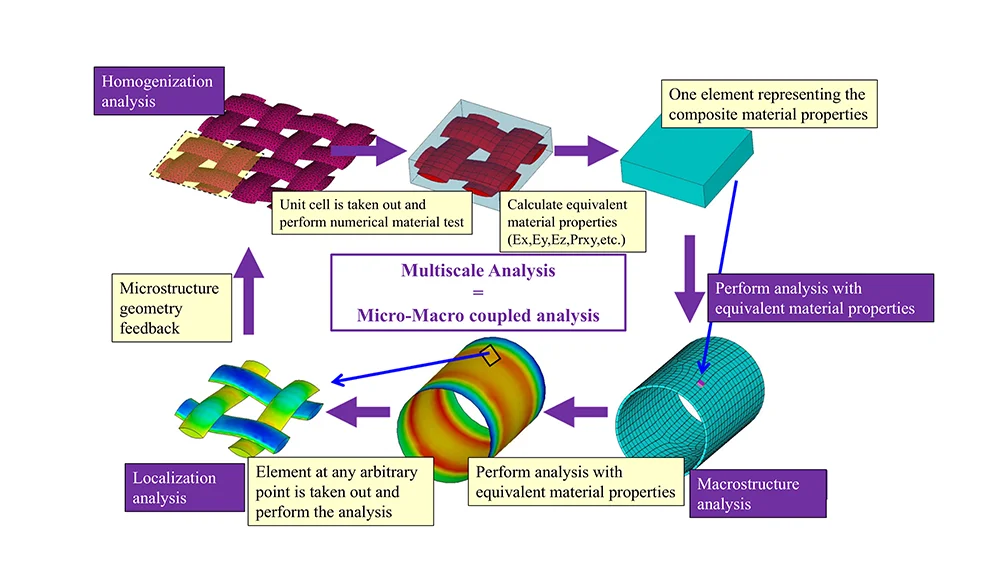
Fig: Flow of Multiscale Analysis using Multiscale.Sim
Read the full paper.
Contents:
- Introduction
- Multiscale analysis using homogenization method.
- Homogenization analysis based on the homogenization method (Numerical material test).
- Localization analysis of composite materials based on homogenization method.
- Numerical material testing of nonlinear materials (extension to nonlinear analysis)
- - Nonlinear properties of composite materials.
- - Anisotropic Hill’s constants for plasticity and creep.
- - Identification of anisotropic Hill’s constant by nonlinear material test.
- Conclusion and references.
Multiscale.Sim offers robust virtual material testing capabilities using the homogenization method and it comes with a number of material microstructure templates.
Search for similar contents
Virtual material testing, Multiscale analysis, Homogenization theory, Microstructure, Creep, Elasto plastic, Composites,
関連情報
関連する解析事例
MORE関連する資料ダウンロード
MORE-
熱流体解析ソリューション ~設計段階からの熱課題をシミュレーションで解決する~
~ツールの導入から熱設計、解析業務の効率化まで支援~
-
多拠点で同時進行デザインレビューを実現する
~Ansys Discoveryで設計検証が効率化~
-
リアルタイム解析で変わる商談提案の革新
~Ansys Discoveryで商談中に即座に検証結果を表示~
-
バイオ医薬のスケールアップに貢献する
~Ansys Fluentによる攪拌槽解析~
-
剥離・接合強度評価ソリューション ~Ansys Workbench Mechanicalで実施できる剥離解析~
-
レーザー集光の高温レンズ歪みを克服するAnsys連携ソリューション
-
周波数応答解析×自動抽出で干渉チェックを高速化
-
直観的な操作で無線/デジタルフィルタの設計・最適化を支援する〜Ansys Nuhertz FilterSolutions〜