Release Information
PlanetsX 3.1 Release Information
PlanetsX 3.1 was released in February 2014.
The following three items are the Release Highlights.
- New features have been added
- The solver performance has been improved
- Warp (Structure-linked) Analysis features have been improved
- Specifying thermal load separate from the temperature distribution obtained from Polymer Processing - Injection (PlanetsX) Analysis
- Analysis using the Engineering Data (without resin materials database) is now supported
- Transferring a fiber orientation anisotropic property to Warp Analysis is possible while using different meshes in Polymer Processing - Injection (PlanetsX) and Warp Analysis
- Specifying the fiber orientation anisotropic property and initial strain are possible simultaneously
- It is possible to apply the temperature-dependence of the linear expansion coefficient of the resin database
- Curing Reaction Analysis features have been improved
Detail of PlanetsX 3.1 Release Highlights
New features have been added
Prediction of bonding wire deformation in the resin sealing step of an IC chip is now possible. Viscous resistance,
which is proportional to the size of the object in fluid, flow rate, and viscosity of resin are now able to be
calculated. It is possible to load that resistance on the object in the Structural Analysis.
You can get the general deformation prediction of an elongated object flow path structure*1 including the
reliability evaluation of electronics packaging.
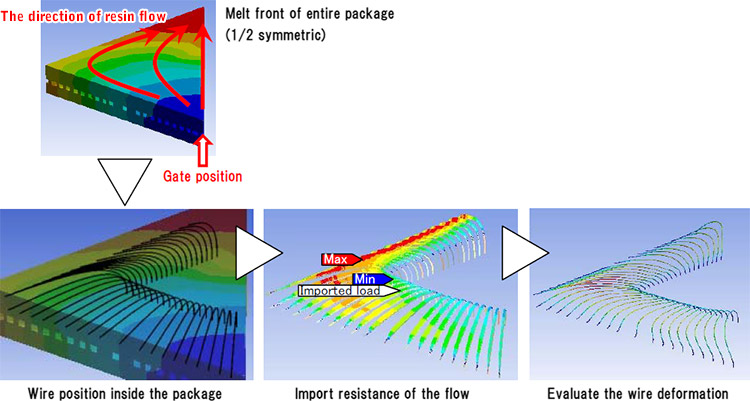
Direct coupled analysis for the temperature between structure region and resin region is now possible. As a result, it is possible to evaluate interactively how the insert material is heated by the resin over time along with the filling process. It is possible to obtain more realistic solutions by taking into account a result of the influence of the heat capacity of the mold such as how the resin is cooled/warmed by the mold.
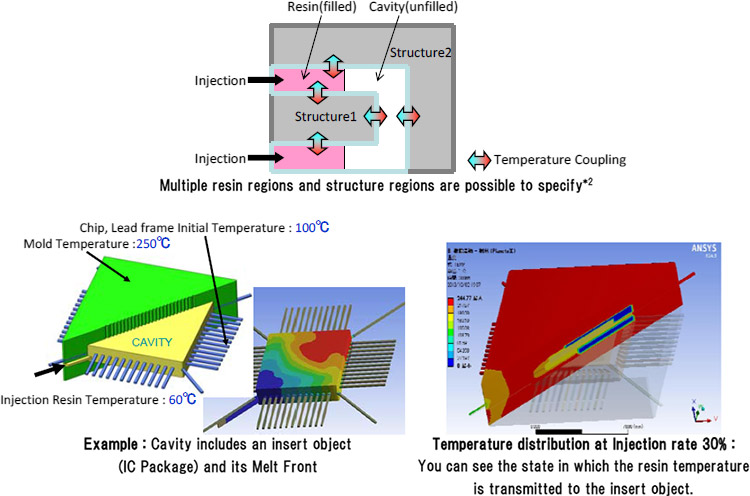
It is possible to specify the different temperatures and the interfacial heat transfer coefficient in each mold.
It is easy to specify, for example, when a cavity side and a core side temperature are different, or a temperature
is controlled by time in actual molding cases.
It is possible for users to specify the room temperature value that affects the calculation for warpage (shrinkage) (Fixed at 20 in the previous version). Warpage is determined by temperature contraction due to cooling and hardening shrinkage of the resin. Specifying the room temperature means that users can arbitrarily specify the endpoint of this interval.
The solver performance has been improved
Parallelization processing was effective only in some optional features*3 in the previous version, now it
is effective in all optional features and basic functions of PlanetsX. As a result, it is possible
to reduce the calculation time by utilizing fully the ability of the user's computer.
Special license for parallel computation is not required*4, and there is no limit to the number of
cores*5.
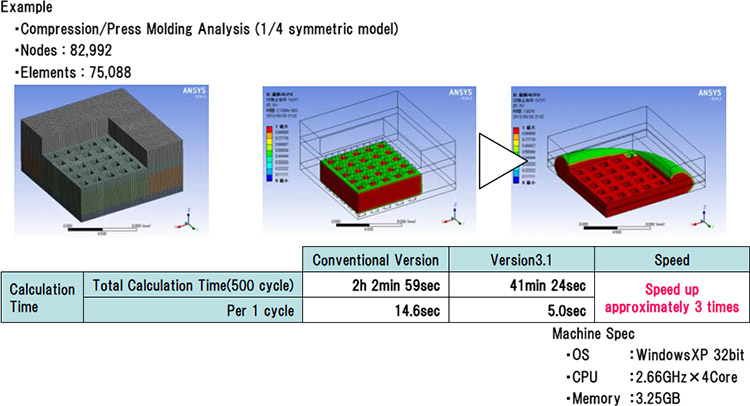
Reducing the number of calculation cycles, without sacrificing accuracy, have been achieved by carrying out a review of time steps of holding pressure and cooling phase.
It is possible to specify time steps arbitrarily at any time in an analysis.
Warp (Structure-linked) Analysis features has been improved
Warp Analysis was expressed by converting to the temperature difference with a strain equivalent to the volumetric
shrinkage ratio obtained by Polymer Processing – Injection Analysis (PlanetsX) and using this
temperature difference as a load in a structural analysis in the previous version.
In version 3.1, it has been improved to a technique that eliminates the process of converting to this temperature
difference, given strain corresponding to the volumetric shrinkage ratio directly into a structural
analysis*6.
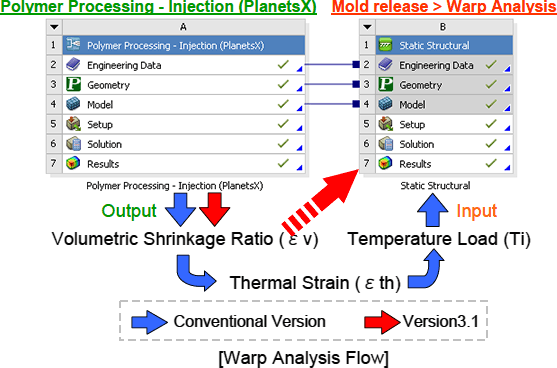
Since the thermal load label used for the transfer of volumetric shrinkage ratio in Structural Analysis has become
free by the improvement described above, now can give the thermal load independently from the temperature
distribution obtained by Polymer Processing - Injection (PlanetsX) Analysis.
In addition, the "No Setting" feature is added for the resin database in the Warp Analysis settings, now
users can perform Warp Analysis using the properties from the Engineering Data.
Enhancements of the above two have been made for Warp Analysis using the results of the Fiber Orientation Analysis.
If the linear expansion coefficient of the resin database had a temperature dependence, the effect is now taken into account when performing Warp analysis*7.
Curing Reaction Analysis features has been improved
It is possible to enter a value for the initial cure rate as a calculation start point that was fixed at zero in the previous version. Versatility has increased since the analysis can be set at various levels between uncured and cured state for the initial setting resin by utilizing this feature.
The fields for determining thermal conductivity and specific heat at "uncured-state" and "completely cured state" have been newly added respectively in the resin database and curing rate dependence is now taken into account during the calculation. Because thermophysical property of the resin varies greatly in the vicinity of the gel point, analysis considering the curing rate dependence of thermophysical property is possible to get closer to reality. In this case, the specific heat and the thermal conductivity of uncured and completely cured state are required to measure independently as input data respectively. By using these linear interpolation equations in the solver, it is now possible to predict thermal conductivity and specific heat considering the curing rate dependency at any temperature.
Only one division Spencer-Gilmore expression was supported up to now. PlanetsX version3.1 supports Spencer-Gilmore equations of up to division 2, Tait equation, and Second-order approximation formula as the same specification to the thermoplastic resin. As a result, flexibility to the measurement data fitting has been enhanced. However, the PVT data of uncured state and completely cured state are required to measure independently as input data respectively as before. By using these linear interpolation equations in the solver, it is now possible to predict the PVT considering the curing rate dependency.
*1 The object has small pressure gradient in the flow direction and small projection area to the
flow.
*2 Must be kept in separate groups structure parts and resin parts respectively using multi-body
feature.
*3 Fiber Orientation Analysis.
*4 Additional parallel computation license for the Ansys is required for Warp Analysis and Mold Cooling
Analysis
because these use the Ansys solver.
*5 Effect of parallelization and the number of cores (scalability) are not necessarily proportional.
*6 Uses the Ansys solver customized dedicatedly.
*7 By this, Warp Analysis under the same conditions may have different results. The result of version3.1 can
interpreted as a value more realistic.
関連記事
関連情報
関連する解析事例
MORE関連する資料ダウンロード
MORE-
Ansys Discovery導入成功の5つのステップ
~シミュレーション主導設計の実現のための秘訣とは?~
-
HPCとGPUで開発サイクル短縮: シミュレーション高速化による流体解析の最新事例
-
熱流体解析ソリューション ~設計段階からの熱課題をシミュレーションで解決する~
~ツールの導入から熱設計、解析業務の効率化まで支援~
-
多拠点で同時進行デザインレビューを実現する
~Ansys Discoveryで設計検証が効率化~
-
リアルタイム解析で変わる商談提案の革新
~Ansys Discoveryで商談中に即座に検証結果を表示~
-
バイオ医薬のスケールアップに貢献する
~Ansys Fluentによる攪拌槽解析~
-
剥離・接合強度評価ソリューション ~Ansys Workbench Mechanicalで実施できる剥離解析~
-
レーザー集光の高温レンズ歪みを克服するAnsys連携ソリューション