Multiscale.Sim Journal Articles Introduction
Reliability Design of Composite Materials Based on Virtual Material Test
- Published: July 2024
- Yamamoto Koji, Department of Engineering, Cybernet Systems Co., Ltd, Japan
Abstract
The importance of improving the product performance by material design is starting to be recognized. For example, weight reduction has been achieved by structural design change, which can be done by shape optimization and topology optimization analysis in CAE. These optimization techniques, based on sensitivity evaluation, have been used over decades and, also have been the solution to overcome the over-reliance on craftsman's intuition and experiences. However, structural design change has its own limit. The need for material design change has been further noticed in improving the product functionality and finding the solutions for environmental degradation.
As an example, large-scale weight reduction to improve fuel efficiency in transportation vehicles can be achieved by using multi-material parts. In electronic boards, traditionally used eutectic solder (i.e. lead-based solder) is restricted by the RoHS Directive [1] due to its toxicity. So, application of lead-free material is required. In such case, new material design parameter is not limited to focus on performance only. It is unnecessary to have better performance than conventional one. Therefore, material design required more careful insight for reliability. Another example is material design concerns related to semiconductor packages. Main reasons of failures in semiconductor packaging are usually due to initial failures by molding process in manufacturing i.e. reflow soldering process and reflow sealing process using resin materials, and wear-out by aging. Fig.1 shows the various factors affecting the sealing process failure. Initial failures due to reflow process often appear as warpage.
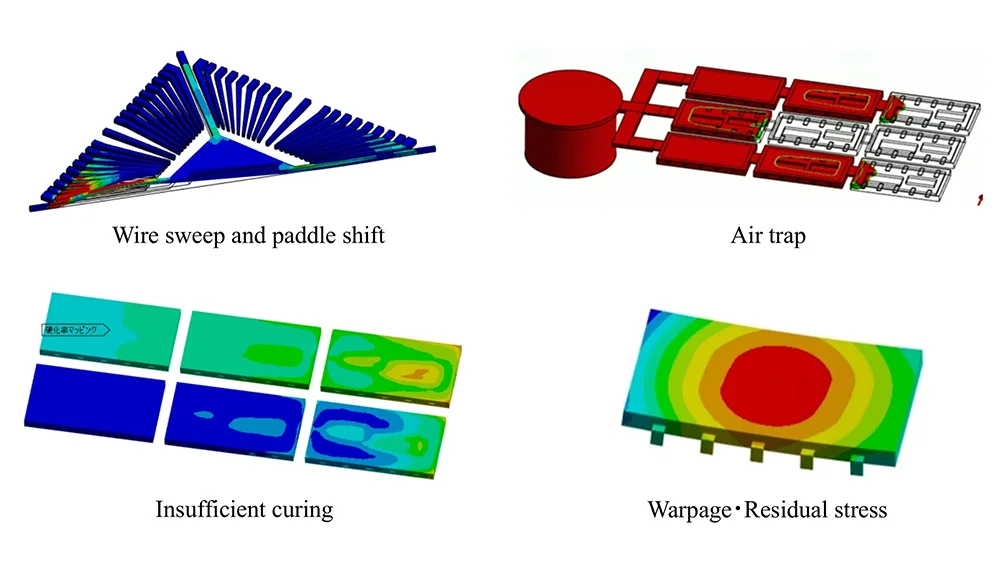
Fig.1 Typical issues in semiconductor encapsulation process
Read the full paper.
Contents:
- Introduction
- Virtual Material Test Using Homogenization Method
- Analytical Examples
- - Prediction of elastic modulus, thermal expansion coefficient and strength of resin with filler.
- - Evaluation of filler-filled resin mounting on semiconductor package.
- Conclusion and references
Multiscale.Sim offers robust virtual material testing capabilities through the homogenization method, and comes with a number of material microstructure templates.
Search for similar contents
Virtual material testing, Homogenization, Multiscale analysis, Reliability design, Semiconductor package, Thermal cycle, Strength, Filler dispersed composites, Warpage
関連情報
関連する解析事例
MORE関連する資料ダウンロード
MORE-
熱流体解析ソリューション ~設計段階からの熱課題をシミュレーションで解決する~
~ツールの導入から熱設計、解析業務の効率化まで支援~
-
多拠点で同時進行デザインレビューを実現する
~Ansys Discoveryで設計検証が効率化~
-
リアルタイム解析で変わる商談提案の革新
~Ansys Discoveryで商談中に即座に検証結果を表示~
-
バイオ医薬のスケールアップに貢献する
~Ansys Fluentによる攪拌槽解析~
-
剥離・接合強度評価ソリューション ~Ansys Workbench Mechanicalで実施できる剥離解析~
-
レーザー集光の高温レンズ歪みを克服するAnsys連携ソリューション
-
周波数応答解析×自動抽出で干渉チェックを高速化
-
直観的な操作で無線/デジタルフィルタの設計・最適化を支援する〜Ansys Nuhertz FilterSolutions〜