Release Information
CMAS 2019R2
1. Ansys2019R2 support
Multiscale.Sim now supports Ansys Workbench 2019R2 and Ansys Mechanical 2019R2. Please note that the operation procedure has slightly changed due to changes in Ansys 2019R2 Workbench and Mechanical GUI.
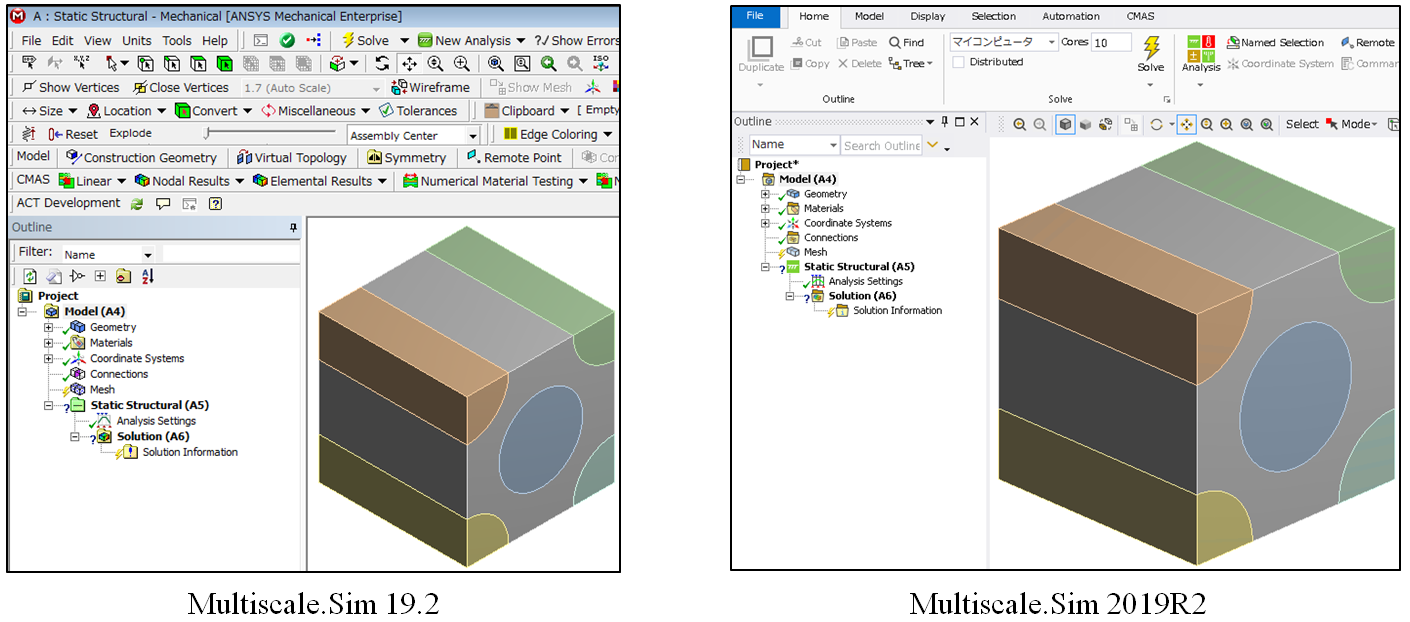
Figure 1. Old & new versions of Multiscale.Sim GUI menu.
2. Template to create microstructure
There are some improvements and new function for filler dispersed composite and short fiber dispersed composite models (hereinafter called dispersed model).
2.1 New model
2.1.1 Aggregated model
Aggregation factor now can be specified for dispersed model. Aggregation state was not considered in the old version because each particle was arranged randomly. In this version, we can specify degree of aggregation (refer figure below).
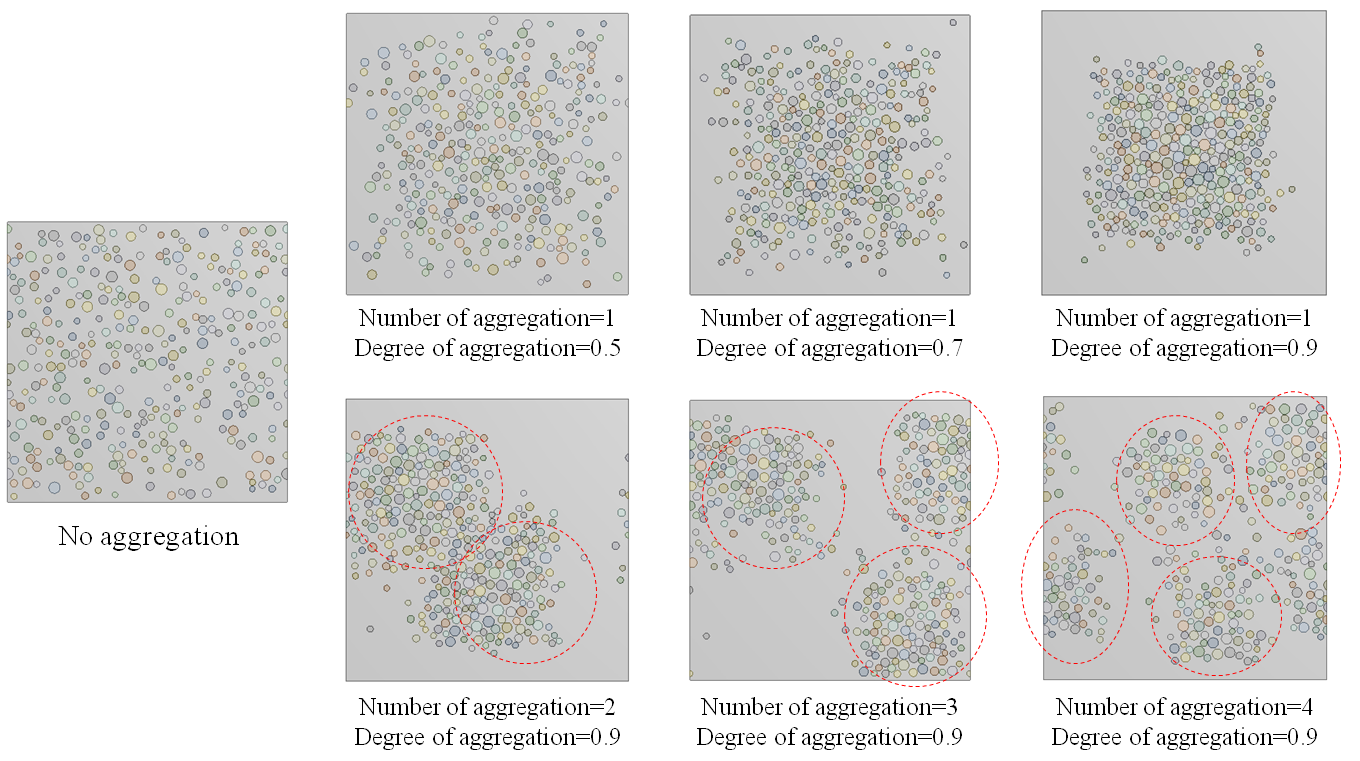
Figure 2. Comparison of overview of micro models created based on difference aggregation factors.
2.1.2 Circle dispersed model
A model with many circles distributed in a rectangular region can now be created. Please note that homogenization analysis does not support two dimensional models. It will be used for general Ansys analysis.
2.1.3 Closest packing model
A model in which spherical particles are packed to the limit of the unit cell can now be created.
2.2. Improvements
2.2.1. Performance
2.2.1.1. Support for parallel computing
New version supports parallel computing for creating micro model which previously took a long time. Dispersed model creation is now expected to be much faster as shown in figures below.
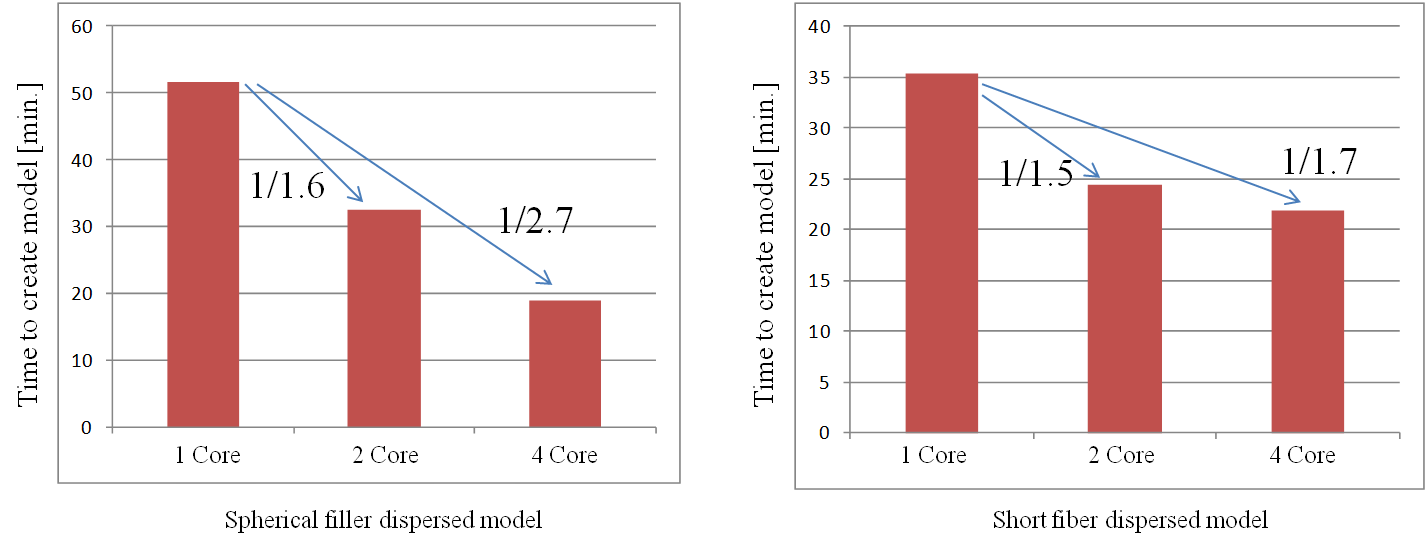
Figure 3. Sample comparison of time taken to create microstructural model between old and new versions.
2.2.1.2. Improvement in packing algorithm
Packing algorithm for dispersed model has been improved drastically. We can create a complex model in a short time in addition to parallel computing. We can also achieve a higher volume fraction of filler because number of iterations can be increased.
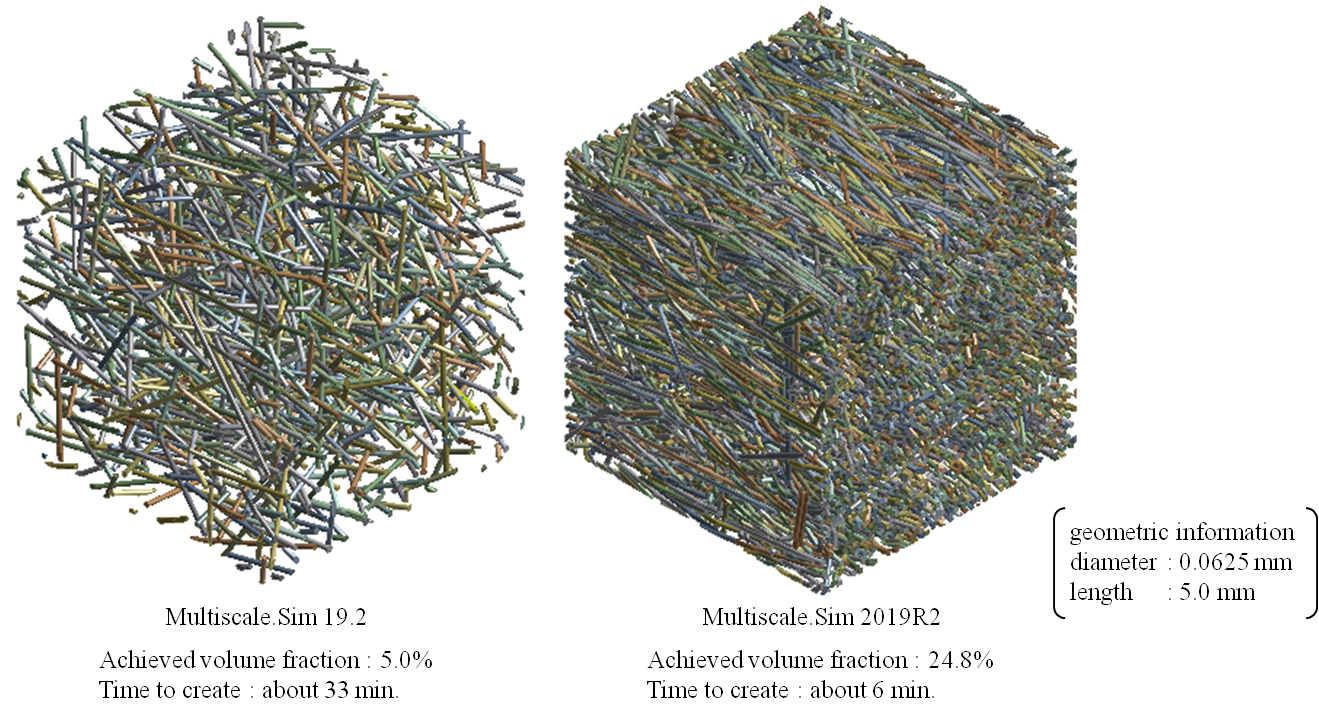
Figure 4. Sample comparison of achieved volume fraction of fiber between old and new version (parallel computing option has been set to off in the case of new version). 2.2.2. Random seed
2.2.2. Random seed
Value of random seed can now be specified in the case of dispersed model creation. The same model can be created each time by deliberately specifying the same random seed value. We need to turn off parallel computing option when creating the same micro model.
2.2.3. A robust model for meshing
The particle dispersion model no longer creates extremely small areas on the exterior surface. Meshing operation will be more stable and successful as a result of this improvement.
2.2.4. Model extraction during production process
In the case of a dispersed model, sometimes it could take a very long time to create the model, and it would fall into an infinite loop depending on geometric conditions. New version allows to create the model during production process by stopping the program. At this point, overlapped region is maintained in the case of filler dispersed model and deleted in the case of short fiber dispersed model.
This model does not exactly match with geometrical parameter you specified. However, you can get a rough estimate of equivalent material constants or review the correction policy based on this information.
3. Hyper elastic homogenization for Workbench GUI
Nonlinear homogenization has now been implemented in the Workbench environment. We can get macro scopic stress strain curve for any kind of deformation mode considering hyper elastic effect. Moreover, material constants for anisotropic hyper elasticity can be identified by curve fitting its response.
関連情報
関連する解析事例
MORE関連する資料ダウンロード
MORE-
剥離・接合強度評価ソリューション ~Ansys Workbench Mechanicalで実施できる剥離解析~
-
レーザー集光の高温レンズ歪みを克服するAnsys連携ソリューション
-
周波数応答解析×自動抽出で干渉チェックを高速化
-
直観的な操作で無線/デジタルフィルタの設計・最適化を支援する〜Ansys Nuhertz FilterSolutions〜
-
流体機器設計の新たな一歩
~Ansys Discoveryで加速する設計改革~
-
筐体の冷却性能を構想設計から見える化 (手戻りを削減できる)
~Ansys Discoveryで始める電気筐体製品の設計改革~
-
若手でもすぐに使えるリアルタイム解析 (勘と経験からの脱却)
~Ansys Discoveryによる30名規模メーカーの設計改革~
-
構想設計ですぐにリアルタイム検証 ~解析専任者ゼロでも使いこなせるAnsys Discovery~
~解析専任者ゼロでも使いこなせるAnsys Discovery~