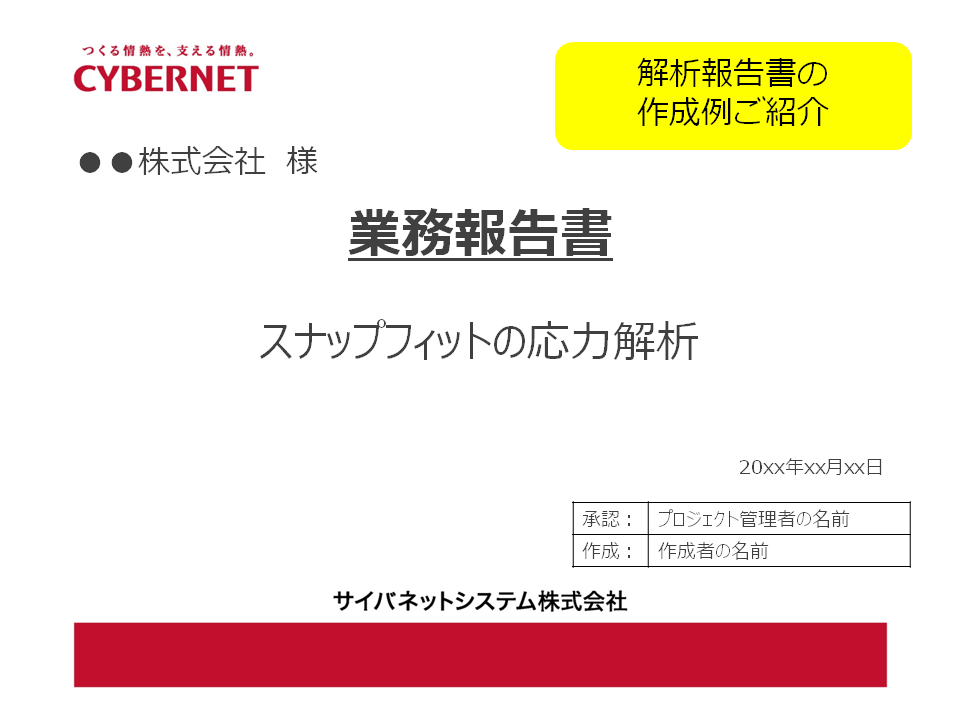
CAEを学ぶ
比べてみる、線形構造解析と非線形構造解析
〜特徴、適用範囲、Ansysのモデル化方法など〜
比べてみる、線形構造解析と非線形構造解析の概要
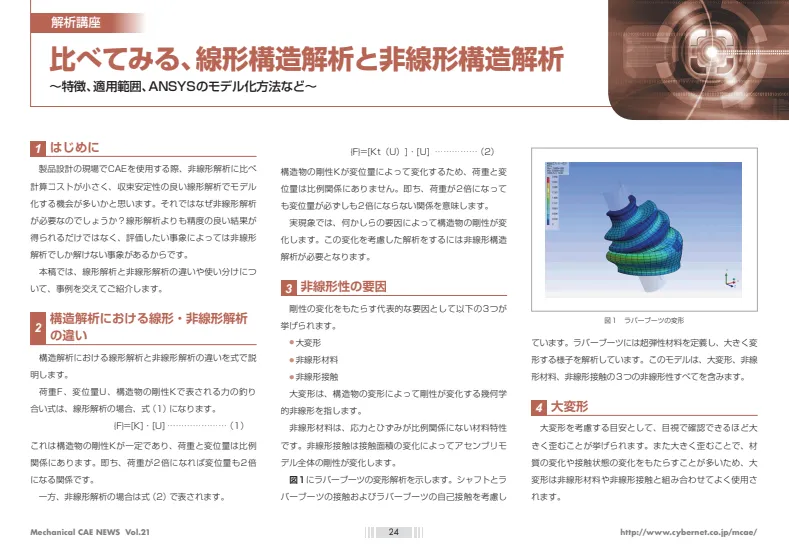
1 はじめに
本稿では、線形解析と非線形解析の違いや使い分けについて、事例を交えてご紹介します。
2 構造解析における線形・非線形解析の違い
荷重F、変位量U、構造物の剛性Kで表される力の釣り合い式は、線形解析の場合、式(1)になります。

一方、非線形解析の場合は式(2)で表されます。

実現象では、何かしらの要因によって構造物の剛性が変化します。この変化を考慮した解析をするには非線形構造解析が必要となります。
3 非線形性の要因
- 大変形
- 非線形材料
- 非線形接触
非線形材料は、応力とひずみが比例関係にない材料特性です。非線形接触は接触面積の変化によってアセンブリモデル全体の剛性が変化します。
図1にラバーブーツの変形解析を示します。シャフトとラバーブーツの接触およびラバーブーツの自己接触を考慮しています。ラバーブーツには超弾性材料を定義し、大きく変形する様子を解析しています。このモデルは、大変形、非線形材料、非線形接触の3つの非線形性すべてを含みます。
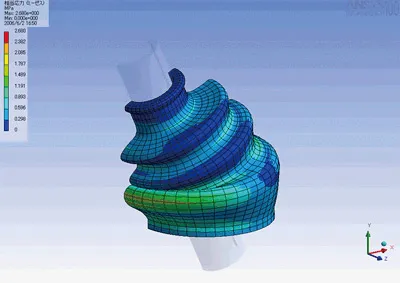
図1 ラバーブーツの変形
4 大変形
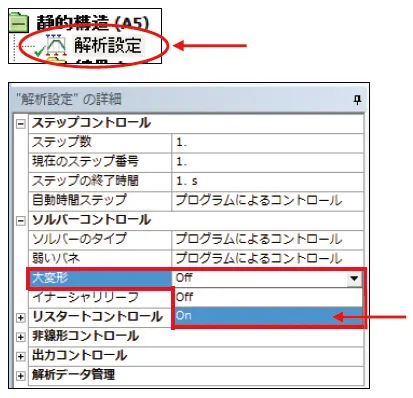
図2 大変形設定メニュー
4-1 大変形の設定
4-2 大変形ON、OFFの比較
回転量が6[°]の変形結果では、大変形ONとOFFでほとんど差は見られません。
回転量が90[°]になると、その差が顕著に現れます(図3-b)。
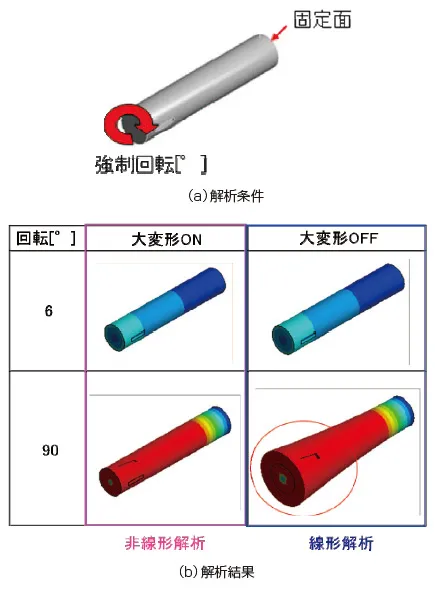
図3 円柱のねじり解析
このように、大変形OFFでも計算結果は得られますが、適切な結果でない可能性があるので注意が必要です。
5 非線形材料
非線形材料は、塑性加工をモデル化したい場合やゴム、プラスチックの材料を扱いたい場合に必要です。非線形材料の種類は多岐にわたり、塑性材料、超弾性材料、粘弾性材料などが挙げられます。ここでは、塑性と超弾性のモデル化について解説します。
5-1 塑性のモデル化
金属加工(圧延、絞り加工、金属によるプレス成型)でよく用います。
Ansys Workbench Mechanicalでは、「エンジニアリングデータ」と呼ばれる設定ツールで(図4-a)、応力とひずみの塑性領域を二直線近似(図4-b)、または多直線近似(図4-c)で定義できます。
※手順の詳細はANSYS Workbench Mechanical 材料非線形セミナーテキスト [5.弾塑性材料]をご参照ください。
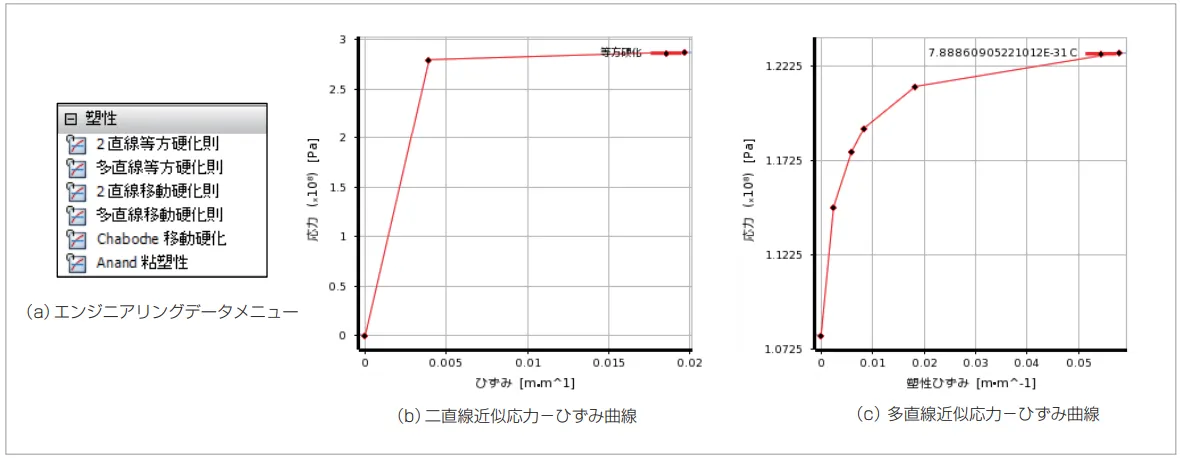
図4 塑性材料の定義
塑性材料の場合(図5-a)、プレスを徐荷しても被加工材は変形したままです。つまり、残留ひずみが計算されています。線形材料の場合(図5-b)、プレスを徐荷すると被加工材は変形前の形状に戻ります。これは残留ひずみが計算されず、荷重の徐荷で応力が0の状態(ひずみが0)になる線形材料の特性です。
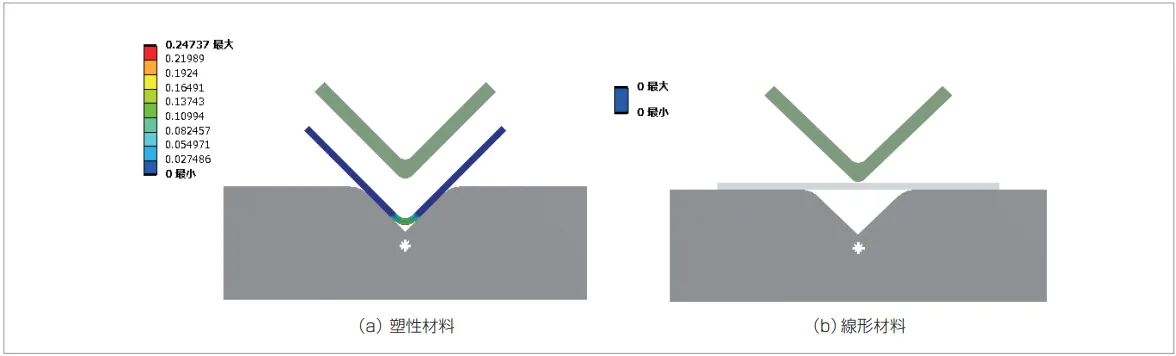
図5 V字プレス加工解析
5-2 超弾性のモデル化
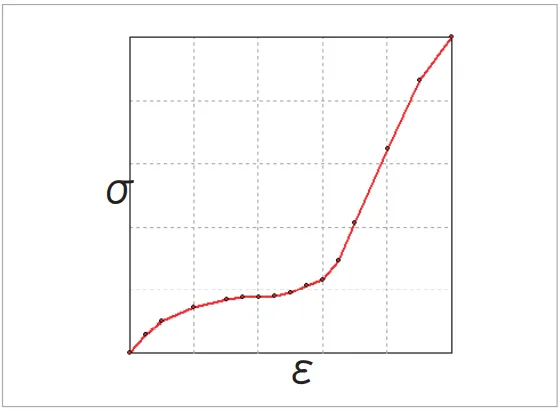
図6 超弾性材料の応力-ひずみ曲線
※手順の詳細はAnsys Workbench Mechanical 材料非線形セミナーテキスト[6.超弾性]をご参照ください。
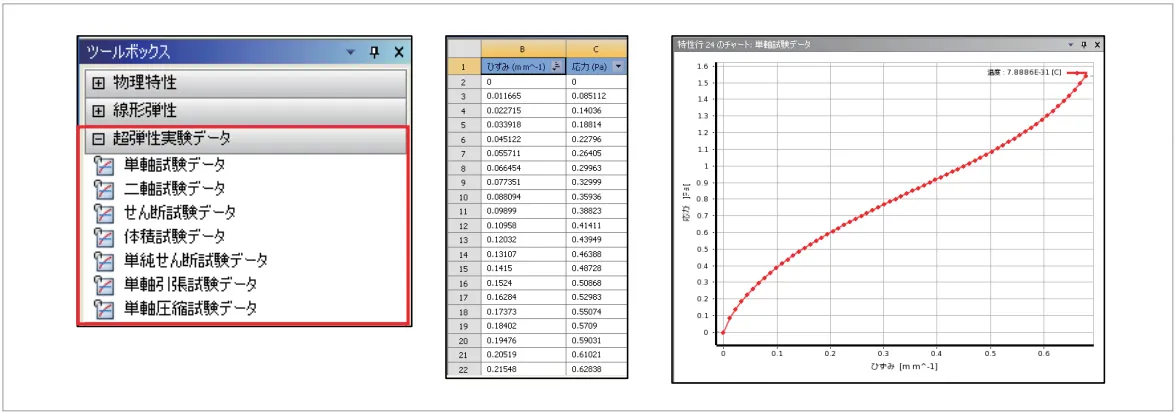
図7 カーブフィッティング機能
の場合は0)のみで、簡単に超弾性挙動をモデル化できます。
5-3 線形材料と非線形材料の使い分け
例えば、次の2つの目的があるとします。
- ある荷重条件に対して、どの程度の残留変形や残留応力が発生するか知りたい
- 塑性に至るかどうか、発生応力と降伏点を比較したい
2.の場合、弾性材料を定義した線形解析を実施し、応力結果と降伏応力の比較で判断出来ます。つまり、塑性材料の定義は不要です。
非線形材料特性を不必要に定義するのではなく、目的と評価したい結果を明確にして使い分けることが重要です。
6 非線形接触
接触面の状態は、線形接触と非線形接触に分類されます。線形接触は、変形過程で接触面積が変化しない(接触面間の剛性が変化しない)状態を表します。接触面間が結合されているケースなどが考えられます。
非線形接触は、接触面が衝突・分離・滑りによって接触面積が変化する(接触面間の剛性が変化する)状態を表します。非線形接触解析の例として、マットの圧力分布解析を示します。腰部を模した人体モデルとマットが接し、重
力によって人体がマットに沈み込みます(図8-a)。その際、接触面積の変化に伴い圧力分布も変化します(図8-b)。
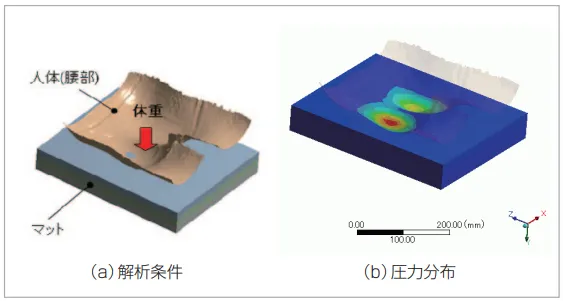
図8 マットの圧力分布解析
【参考】 河内まき子,持丸正明,岩澤洋,三谷誠二(2000):日本人人体寸法データベース1997-98,通商産業省工業技術院くらしとJISセンター.
6-1 接触の設定
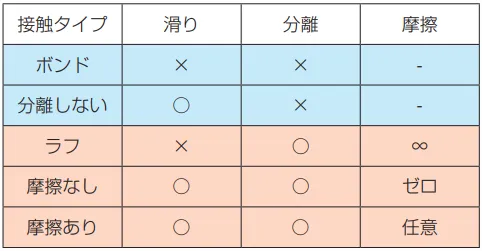
表1 接触タイプ
※接触タイプ適用例
「ボンド」:溶着部
「分離しない」:軸とすべり軸受の接触部
「ラフ」:ゴムストッパーと床面の接触部
「摩擦なし」:潤滑剤のある接触部、氷と物体の接触部
「摩擦あり」:ブレーキパットとディスクの接触部
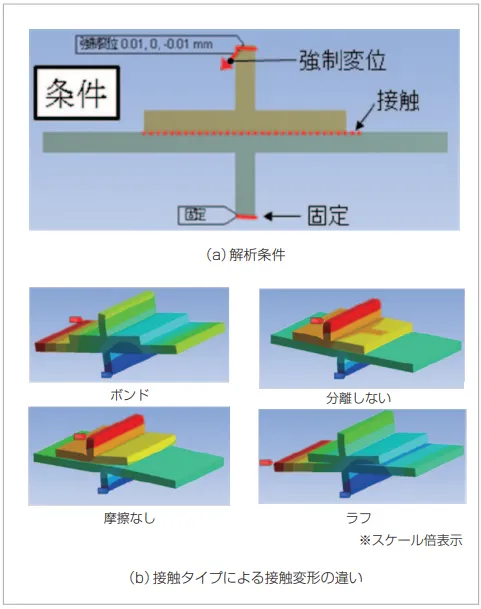
図9 接触タイプの検証
6-2 線形接触、非線形接触の使い分け
7 おわりに
関連記事
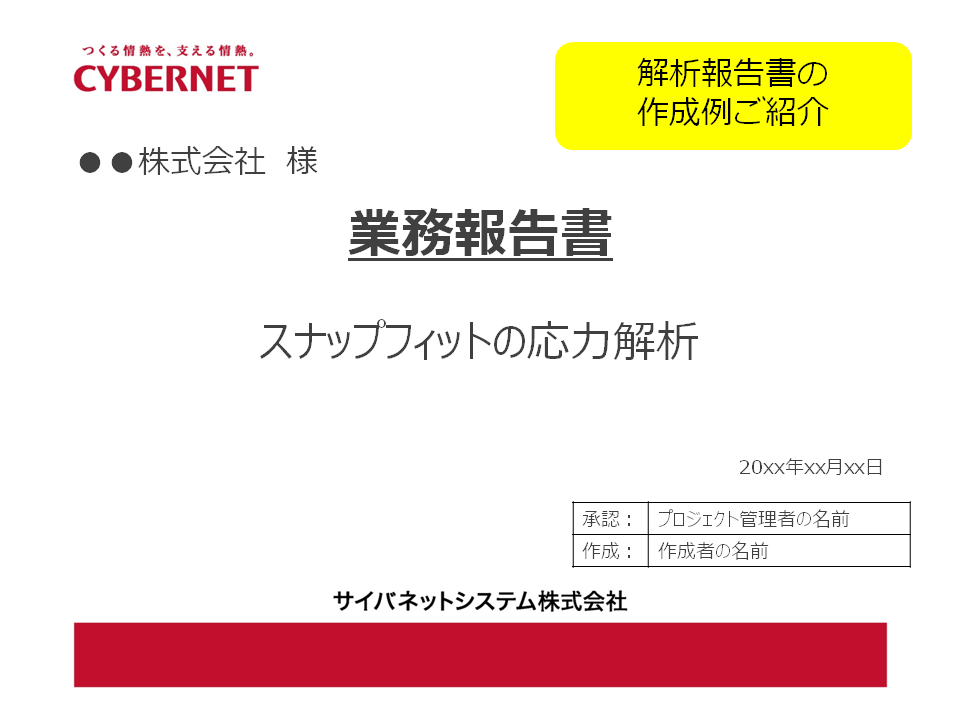
関連情報
関連する解析事例
MORE関連する資料ダウンロード
MORE-
Ansys Discovery導入成功の5つのステップ
~シミュレーション主導設計の実現のための秘訣とは?~
-
HPCとGPUで開発サイクル短縮: シミュレーション高速化による流体解析の最新事例
-
熱流体解析ソリューション ~設計段階からの熱課題をシミュレーションで解決する~
~ツールの導入から熱設計、解析業務の効率化まで支援~
-
多拠点で同時進行デザインレビューを実現する
~Ansys Discoveryで設計検証が効率化~
-
リアルタイム解析で変わる商談提案の革新
~Ansys Discoveryで商談中に即座に検証結果を表示~
-
バイオ医薬のスケールアップに貢献する
~Ansys Fluentによる攪拌槽解析~
-
剥離・接合強度評価ソリューション ~Ansys Workbench Mechanicalで実施できる剥離解析~
-
レーザー集光の高温レンズ歪みを克服するAnsys連携ソリューション