解析事例
AnsysやDesignSpaceにおけるFOA(FirstOrder Analysis)の活用
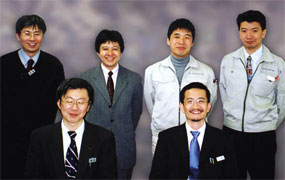
今回のインタビューにご協力下さいましたお客様は、株式会社豊田中央研究所機械分野第14研究領域の皆様です。株式会社豊田中央研究所様は、トヨタグループ全体の事業展開に貢献する研究所として、1960年に創立されました。現在は省資源、省エネルギ、環境保全、快適性・安全性の向上、高度情報化などの課題に応えるべくエネルギ/環境分野、情報・通信/エレクトロニクス分野、材料/バイオテクノロジ分野、そして今回ご紹介する皆様が取組まれている機械/人間工学分野において研究活動を行なわれています。また世界の多くの研究機関、大学などとの連携も進められており、科学技術の発展に寄与されています。
最近では設計者のためのCAEとしてFOA(FirstOrder Analysis)を提唱され、Ansys ConferenceでもAnsysやDesignSpace上でのFOAの活用について発表されています。
(以後、株式会社豊田中央研究所の皆様の敬称は略させていただきます。)
インタビュー
最初に皆様の業務全般ならびにAnsys、DesignSpaceに関係する分野についてご紹介下さい。
小島
当社はトヨタグループの中央研究所という位置付けで、約900人の社員がおり、主に機械、材料、システムの分野から構成されています。私たちはボデー構造やサスペンション機構などを対象にした設計工学の研究をしており、エンジニアリング寄りの内容といえます。私たちの所属する第14研究領域では、「設計者向けCAEとは?」という課題に取り組んでいます。その成果が現在FOAというソフトウェアになっており、これは製品開発の初期段階で用いられる設計ツールです。さらに、詳細なCAEを扱いながら必要十分な設計情報を抽出する技術も含まれます。こういった研究活動を通じて、開発プロセスをさらに効率化するとか、革新的な設計を支援する技術を考えていきたいと思っております。
サイバネットシステムから最初に製品を導入した経緯をお聞かせ下さい。
尼子
15年程前にリモートコンピューティングサービスで、論理回路系ソフトを使い始めたのが最初だったようです。その後ソフトウェアの導入ではPATRANが最初で、その頃から私も担当になりました。その後機構解析のDADSや制御系のMATLABを導入して社内のネットワークで利用するようになりました。Ansysの導入は比較的新しくて5年程前になると思います。
西垣
もともとNASTRANで固有値解析や静解析、MARCで非線形解析を行なっていましたが、やはり動的応答解析も必要になってきたのです。そこで新たなツールとしてAnsysを評価し始めました。Ansysは接触も含め全ての非線形性を考慮した動的応答解析ができるのがたいへん魅力でしたし、我々のところには様々な仕事が入ってきますので、何でもこなせるツールを1つ手元に置いておきたかったのです。何でもできてその場その場でちゃんと迅速に解が出るものをです。Ansysはプリポストの機能もありますし、色々なジャンルの分野に使えますしね。実際に使ってみて座屈解析でもいい結果が出ましたから感動しました。
Ansysは汎用解析ツールですが、逆に市販のCAEで特定の分野の解析機能を追求したツールも多く存在します。研究所という立場から考えて、そのような特化したツールに対するAnsysの有用性というのは何でしょうか?
西垣
それぞれ特定の分野に得意なツールは使いやすく有用な部分もあります。しかしツールを使って計算するのは我々の本当の目的ではなく、内製ツールの補助に市販ツールを使ったり、別のツールの検証や実験の検証などに利用する点で意味があるのです。目的がツールを使うことに特化してはいないものですからそういう点でAnsysは便利なのです。
実際にAnsysを座屈解析以外のどういう分野でご利用されていますか?
後藤
最初はブレーキのローターに埋めこむセンサーの応力解析にAnsysを利用しました。その後ブレーキの摩擦による熱問題を考慮する必要性を感じ、最近になって熱と構造の連成解析の勉強を始めたところです。今は単体で境界条件も簡単な設定で解析していますが、目標はブレーキのアセンブリ全体の過渡解析です。回転しながら擦っていくと接触の問題があります。油圧でピストンが押されてパッドとローターが弾性変形しながら当たるわけです。その際に局部的にどこに当たるかの当たりの大小で熱の発生の仕方が変わってきます。生じる熱変形がどの程度でどのような形態になるのか、それをAnsysで解析したいと思っているところです。Ansysは連成解析を簡単にできるという点で非常に重宝するソフトです。従来、私はNASTRANで静解析や動解析を行ってきたのですが、接触解析となるとMARCやLS-DYNAを使わなければならず、結構重くなってしまうのです。そんな時、尼子さんや西垣さんがパソコンでAnsysを使っているのを見て、これからはそういうパソコンで解析をする時代かなと思いました。ちょっと構えてしまっていた連成解析が身近にできるというところでAnsysを使うようになったわけです。
豊田中央研究所様では、制御系も含めてブレーキシステム全体などを解析する全体像を見る部分と、一方でFOAという概念下で設計者が部分的に簡略化したモデルを解析する、つまりブレーキパットの部分だけを解析するという2つの課題があるのですね。それぞれを橋渡しし上手く仕事が流れるようなプロシージャマップのようなものを何かお考えですか?
鶴見
我々にはCAEツール活用に対して2通りの考えがあり、1つは図面をひく設計者が性能を考慮しながら設計できるツールを使うこと。もう1つは図面ができた後に解析者が実験の代用となるシミュレーションを実施してNGが出たら適切な対策案を見出せるようなツールを利用するというものです。前者が部分であり後者が全体を扱うことになります。つまり解析者と設計者の両方のユーザーそれぞれに対してCAEを展開し、概念設計から詳細設計に至る過程をCAEで支援・連結していくことが必要と考えています。それにはそれぞれのルーチンワークに対し、既存のツールだけでは満足できないのでその部分をカスタマイズすることが必要であり、それらの積み重ねでプロシージャ−マップができてくるのではと考えています。具体的には設計者に向けたFOAでは、簡単操作の裏側に製品毎にノウハウや特殊な解析技術が内包された特化型ツールを提供する必要があります.また解析者に向けたツールでは、例えばボデーの振動騒音問題を考えた場合、単品の部品レベルではなくボデー全体で考えなくてはなりません。そうすると100万自由度を越えるような非常に大規模な計算をすることになります。それを毎回流して対策案を考えるのは難しいし時間もかかり、見る事自体も大変です。ですから、そういう計算に対していかに効率良く対策案を出せるツールを作るかというのが課題となるわけです。
ではFOAの利用も前提にして、設計者に提供するソフトウェアとしてのAnsysの位置付けについてはどのように考えられていますか?
西脇
一つの理想形は様々な機能を持つものがネットワーク上のどこかに存在し、必要に応じて特定の機能をその都度使える、つまりそれぞれの機能だけをモジュール化し、コアの部分にAnsysがあるというような形にできればいいと思います。Ansysを真ん中に置いた展開でもっと軽めのネットワークライセンスになるような...
先日リリースしました新しいプロダクトのAI*Workbenchがまさにその発想ですね。ネットワーク上で個々のソルバーや接触コンポーネント、ジオメトリーリーダー、Plug-inコンポーネントなど、コンポーネント単位でライセンスを振り分け共有ライブラリ化するという環境が実現できます。今年はこれからAI*Solutions として新しいシリーズが出てきます。このような製品群によってこれまでのAnsysの技術をより効果的に効率的に運用できるようになると思います。さて、次にDesignSpaceについてお聞かせ下さい。Ansysは言うなればハイエンドの部類で、DesignSpaceは万人受けする簡単なツールです。そのため一般的にFEMをご存知の解析技術者の方には抵抗感があるようです。ですから正直なところ豊田中央研究所様がDesignSpaceを導入されるということには我々も最初は驚きだったのですが。
西脇
やはり設計工学を扱うという性格からです。研究所といっても白衣を着てすごいことやってるというのではなく、もっと柔軟性を持って技術を追求するのがスタンスなのです。ですから誰もが使えるハンマーや鋸が本当は電動鋸よりも必要かもしれない。それならその必要とされている技術を研究していくことが大事だと思います。むしろそちらの方が研究所の新しい分野ではないかと思っています。そういう経緯で1999年にDesignSpaceを使い始めました。
研究所の位置付けが技術の追求だけではなくプロセスの追求や、適材適所でツールを使う言わば方法論のようなものも研究されていくことだと受け取ってよろしいのでしょうか。
小島
正にそういうところがあると思います。例えば材料分析やCAEソフト等、各社それぞれ技術力、応用力を持っています。またソフトウェアのベンダーにもサービス体制が確立されています。そういう中で我々の主務を考えると、プロセスをどう組み合わせるかということにもなるでしょうし、CADが2次元から3次元になり、ラピッドプロトタイピングやバーチャルマニュファクチャリングなどが出てくると、製品性能や信頼性を維持していた設計ノウハウをどうデジタル化するか、過去の蓄積をどうやって織り込んでいくかというようなことが、我々の研究課題になってきているわけです。そこが一般的なCAEの世界ではまだ提供されていないところではないでしょうか。我々がそういう部分の雛形を作ったり、そのフレームとなる部分をベンダーの方々と協力して開発していければ理想的だと思っています。
それがFOAの起源なのですね。
西脇
あらためて設計というものを見つめ直した時に、何かが足りないと痛切に感じたのです。今では多くのCAEがありますし、設計者用や特定分野を追求した解析専任者用など状況に応じて揃えられてきています。でも、そういう市販CAEだけでは何かが足りないと思っていました。それを足さないと効率良く設計はできないのではと。その概念としてあがったのがFOAではないかと思います。
小島
この数年、安く早く物を作るにはCAEが大きな役割を持つとメディアでもさかんに言われていました。設計者もAnsysやNASTRANを使いこなすような時代が来ると。ところが設計の現場には別のデジタルエンジニアリングが求められてもいたのです。ベテラン設計者のもつノウハウを自然に伝承出来ることも含めて。1999年にミシガン大学の菊池先生が豊田中央研究所に来られて、「First Order Analysis」と言う言葉を始めてお聞きしました。米国の自動車会社ではそういう概念があるのだと。そこで、手探りでこういう形のものかなというのを西垣さんを中心にして作り始め、先生のアドバイスを頂きながら形にしていったわけです。長年、トヨタグループ各社を相手にCAE分野の研究を進めていた我々にも、バックグラウンドとして同じ問題意識がありましたし、名前は違いますがそういう要素技術をずっと蓄えてきていましたので、比較的早いペースで具体化させることができました。
FOAの発想の中で現場における技術伝承が行えるツールを提供することが大事だとお考えですか?つまり、ある意味このFOAが設計者に対して工学的なセンスを与えることを意識して作られたかどうかをお聞きしたいのですが。
西垣
そのとおりです。昔のベテラン設計者は、例えば梁を使った計算に対して応力分布の評価方法などノウハウを持っていまして、詳細CAEと比較しながらより良い評価をしていたのです。しかし、若い設計者は詳細CAEから入っていくものですからどうしてもその結果として出てくる応力分布だけを見てしまい、他の判断との比較検証が柔軟にできないわけです。ベテラン設計者のノウハウなどの伝承もありますし、疑似体験でノウハウを学ぶツールとしてFOAを使ってもらいたいと思います。もちろん最終的に詳細CAEで検証することは絶対必要なのですが、昔の設計者が行っていたように、まず梁で設計を見るところから始めることも重要なのですね。FOAはそういう設計者のノウハウをExcelに入れ込んで技術伝承をしながら使うものなのです。
では設計の流れの中で経験を積んでキャリアアップを行っていく、要はキャリアパスの仕組みについてはどうお考えですか?
尼子
もちろんそういうキャリアパスがあります。設計の担当分野が代わっていくうちに車のボデー全体を知るようになり、いつの間にか車の全てを知るようになる、そういうシステムになっています。
以前、西脇さんがAnsys Conferenceでご講演された中で技術伝承のお話がありましたね。ツールを使う上で運用や設計者の育成などが非常に大事な部分を占めますし、他の企業でも苦労して試行錯誤されているところだと思いますが。
西脇
このままだと「もしかすると次の世代は車を作れないのではないか?」という危機意識はあります。何も知らない我々が材料力学で物を作ることをやってきたのに、もっと若い人は何も知らなくなっているという状況は否定できません。
小島
FOAツールは個別の設計に対応していきます。それは力学をきちんと踏襲する道具であり、例えば何週間も材料力学を思いだしながら苦労して設計計算したものを大幅に短縮できたりするものです。自動車の場合、乗り心地とか、静かさ、運転しやすさ、そして軽くて燃費もいいという多目的な問題を最適化させるというのは、全て力学的に整理されないところが多いと思うのです。そういう意味でのデータや過去の事例をピックアップし、それに準拠する設計計算を行なうという仕事もFOAのねらいとしているところなのです。
西脇
もちろんFOAがあるから技術伝承ができるというわけではなく、本当に技術の伝承をしようと思うと若手と古手の設計者が侃侃諤諤しながらやるのが10年続かないと駄目だと思うのです。技術の伝承はネットワークの中でそんなに簡単にいかないと思いますので、FOAはその中のあくまでもツールであるわけです。
小島
ある人のノウハウでこういう特性だよというのがぱっとモニター上で見えると議論が始まりますよね、そういう議論が逆に伝承になるのと思うのです。
単なる市販ソフトウェアを使いこなすのではなく、FOAのような会社のモノづくりにあったツールも取り入れて、それを使うことで議論も生まれ、技術の伝承も行われるという考え方ですね。
西脇
そこが米国の会社と違う点ですね。米国では設計に関して標準化、可視化を行って全てを残しておく。日本の会社はマニュアルも規格もない、それなのにいつのまにか伝わっていくという文化でしょう。その善し悪しは分かりませんが。
以前SAE(米国自動車技術会)でFOAについて発表されていますし、他にも海外で紹介される機会はあると思いますが、海外でのFOAの反応はいかがでしょうか。
西垣
最初にASME(米国機械学会)で発表したときは、構造解析ではなく設計工学のセッションで話しましたから、新鮮に受け取ってもらえたところはありますね。トポロジー最適化の機能もありますし、Excelのシートを行ったり来たりしながら設計手順も盛り込まれていますのでかなり質問もでました。感触もいいかもしれませんね。CAEをもともとやっている人達よりも設計屋さんに面白いと言ってもらえます。
では設計者の市販のツールであるDesignSpaceに対しては今後どういう機能や可能性を求められていますか。
西脇
設計情報を抽出できるプリでありポストであればいいと思います。応力や変位などの出力結果から設計に直接必要な評価項目を設計情報として外から追加出来ればいいのですが。
西垣
計算結果として応力分布が出て、そこで強度や疲労を考えた時にこれではまずいというのは分かるのですが、そうではなくて断面を切った時に断面に発生するモーメントなどがどうなっているのかが知りたいのです。今言っている設計情報とはそういうものです。
尼子
最近疲労解析機能も入って来ていますが、こういう機能がもっとあっていいと思います。あれも一つの設計情報ですよね。計算していることは応力解析ですが寿命が得られます。ですから振動解析でも固有振動数だけ出てくるのではなく、だったらどうすればいいかという方法まで考えられるようになるといいですね。
設計の評価に必要な出力が柔軟に作成できることがツールの課題ということでしょうか。では今後ツールがどうあるべきか、またツールに対して現場のモノづくり作りはどうしていくべきかについてお聞かせいただけますか。モノづくりへの夢なども教えて下さい。
後藤
我々はトヨタ自動車に一定期間行った経験がありますが、その中の各部門に設計部署があって、そこで書かれた図面をCADでおこしてメッシュを切ってFEAの計算をしています。すると計算して解析結果を出す人と、解析結果を整理してどうすべきかを判断をする人が分かれているのです。さらに試作品を作って解析結果がこうだからこのタイプを作って対策案を出そうとか、実験を手配する人と実験結果から設計屋さんにフィードバックする人もそれぞれ各階層で分かれています。従来は自分の領域を一生懸命やれば良かったのですが、これからはそれら全体の共有化を図れるシステムが欲しいですね。設計の上流から下流までを通して、簡単にマウスをクリックするだけで今の設計状況やアイデアを見ることが出来、それに対して各階層の人が自由に意見を出すことで、クオリティのいいモノづくりに発展するというのが理想です。身近な問題ですと、部品と部品の境界部の条件入力に苦労しています。解析する方も設計する方も境界部の力や拘束の入れ方がよくわからないですよね。ですから結局不確かな中で解析していることになり、安全率も大枠の数値で決めざるを得ません。アセンブリにした時にその部品に対して働く力と拘束力の違いを正確に出せるといいですね。FOAもその辺をデータベースツールとして追加していこうとしていまして、それが技術の伝承という原点に繋がってくると思います。Ansysそのものに対する要望だと、階層が深く解りづらいので階層毎に色分けして見やすくするとかアイコンを付けるとかでGUIを改善して欲しいです。
小島
汎用化の対語として特化とかスペシャライズがありますが、FOAはなんにでも使えることを目標としているのではなく、これしか使えないという特化したものです。特化させることで、製品毎の設計ノウハウを織り込むことができ、非線形でも非定常でもここだけと限定でき、コンパクトになります。
そうすると今後のCAEにはカスタマイズできたり効率的に運用できるフレームワークの提供が注目されてくるとお考えですか。
小島
そう思います。昔はコンピュータセンターに大型のマシンがあって、1ライセンスの汎用プログラムが動いていたわけですよ。今はみんなの机の上に軽々おける個人用のマシンがあるわけですよね。そうすると昔と同じようにフルシステムをそこに入れる必要はない。入れるものも個人の仕事にあったものに変らなくてはいけない。AI*Workbenchなどフレームワーク的なものは共通化するとしても、自分達が使いたい機能だけを寄せ集めていくようなスタイルです。これからはエンジニアリングソフトも違った概念が求められるのでしょうね。
ではソフトを提供する側もカスタマイズする部分のお手伝いがきちんと出来たり、カスタマイズされたものがバージョンアップされてある程度の期間運用していけるサポートが大事になっていくわけですね。
西垣
設計者は操作の習得に時間を割けません。とはいえ無責任に、このボタンを押せばいいというツールでは困るのです。操作の習得は簡単だけれども、入力しているものの意味を試行錯誤しながら使えるものが必要です。DesignSpaceでも、例えば簡単に境界条件を変えさせて、変えたらどうなるかというのを試せるなど、敢えて設計者に考えさせるツールであるといいと思います。そうすると、設計者は危なくなく使えるし、詳細CAEの人も安心してそのツールを使ってもらうことができますよね。簡単な操作だけれども危険だということをしっかり認識し、許容値があるということを理解して使っていけばいいと思います。司
設計者用ツールも今後は使う側の育成まで考えたツールになっていけば理想的なわけですね。では、最後にサイバネットシステムに対するご要望をお聞かせ下さい。
後藤
カスタマイズ作業を一緒に出来るといいですね。カスタマイズというとどうしても凝り固まってしまって、作る人は一生懸命作るんだけど、もらった人は実は頼んでいたものと違っていて困惑してしまうという事があるのです。ですからじっくり共同研究などもできるようにしてツーカーの関係になれれば、本当に作って欲しいもの等がわかると思います。
尼子
AI*Workbenchが出てくると、ある意味で研究的な使い方もできると期待しています。APDLでできる以上のことが可能になるでしょうし具体的に共同研究もできますよね。
これからAnsys社がやろうとしていることは、ソルバーもプリポストもコンポーネントとして自由に組めるようなプラットフォームです。それらによって私どものご提供できるサービスの幅も広がるでしょうし、皆さんもノウハウの注入ができるなど色々と幅が出てくるわけですよね。今後そういうツールをもとに一緒にモノづくりの探求が行なえればと思っています。
First Order Analysis(FOA)
株式会社豊田中央研究所様が提唱されているFOAについて、その考え方と、具体的なサンプルをご紹介します。
FOAとは
開発効率のさらなる向上を目的に、設計構想段階において、設計者自らが短時間・簡便に、設計案の創出・評価が行える設計支援ツール
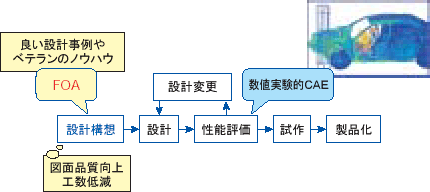
FOAの特徴
設計者自らが、
- 設計案の力学的な成り立ちを理解できる/説明できる。
- ベテランの設計ノウハウを共有できる。
- 自分のノートパソコンで解析できる。
Example1
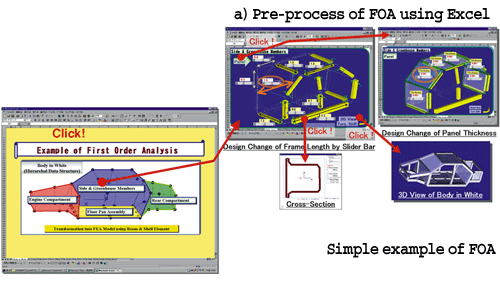
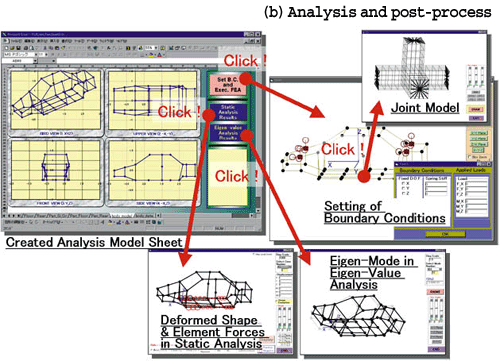
Example2
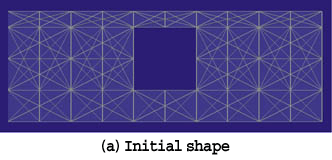
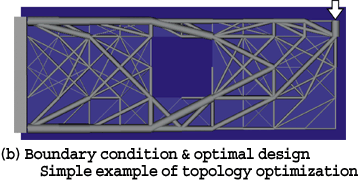
株式会社豊田中央研究所の皆様には、お忙しい中インタビューの時間を作っていただき、誠にありがとうございました。この場をお借りし御礼申し上げます。
「Ansys Product News2002 Spring」に掲載
関連情報
関連する解析事例
MORE関連する資料ダウンロード
MORE-
熱流体解析ソリューション ~設計段階からの熱課題をシミュレーションで解決する~
~ツールの導入から熱設計、解析業務の効率化まで支援~
-
多拠点で同時進行デザインレビューを実現する
~Ansys Discoveryで設計検証が効率化~
-
リアルタイム解析で変わる商談提案の革新
~Ansys Discoveryで商談中に即座に検証結果を表示~
-
バイオ医薬のスケールアップに貢献する
~Ansys Fluentによる攪拌槽解析~
-
剥離・接合強度評価ソリューション ~Ansys Workbench Mechanicalで実施できる剥離解析~
-
レーザー集光の高温レンズ歪みを克服するAnsys連携ソリューション
-
周波数応答解析×自動抽出で干渉チェックを高速化
-
直観的な操作で無線/デジタルフィルタの設計・最適化を支援する〜Ansys Nuhertz FilterSolutions〜