解析事例
冷蔵庫の設計開発におけるAnsys DesignSpaceの活用
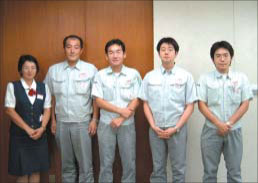
今回のインタビューにご協力下さいましたのは松下冷機株式会社 冷蔵庫事業部 技術グループ 機構設計チームと松下電器産業株式会社 松下ホームアプライアンス社 技術本部冷機研究所 商品開発グループの皆様です。(写真左から松下電器産業株式会社冷機研究所所属の大和 一恵技師、松下冷機株式会社冷蔵庫事業部所属の田中 逸雄主任技師、杉本 一章様、江坂 拓南様、伊藤 嘉浩様。以下社名は松下冷機様と表記させていただきます。)
松下冷機株式会社冷蔵庫事業部様は、事業理念として「地球環境との共存」と「食文化向上への貢献」を掲げられ、完全ノンフロン化の実現、省エネやリサイクルの徹底推進などに取り組まれるとともに、冷蔵庫による新鮮で健康な食生活の提案を進められています。これは、日本で業界をリードしてノンフロン化を達成し、2003年を含め省エネ大賞を4年連続で受賞、内 経済産業大臣賞を2年連続で受賞したことにもあらわれています。
(以後松下冷機様の皆様の敬称は略させていただきます。)
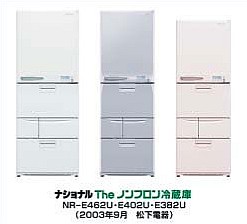
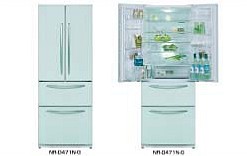
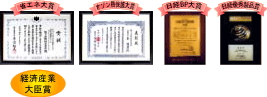
まず、松下冷機様の事業紹介と技術グループにおける業務内容についてご紹介ください。
田中
現在、事業としては大きく、完成品の「冷蔵事業」と「フードソリューション事業」、コンプレッサーなどの「デバイス部品事業」からなり、私たちは家庭用の冷蔵庫を設計から製造まで一貫して行う冷蔵庫事業部になります。松下冷機全体の事業の中でも、家庭用の冷蔵庫がメインの事業となっております。また国内では神奈川県藤沢市にも工場を持っています。海外では、松下グループとして冷蔵庫工場は、中国、タイ、台湾、マレーシア、フィリピン、インドネシア、またデバイス部品関係はタイ、マレーシア、中国、シンガポールに工場があります。草津工場の従業員は約1000名で、日産約4,200台の生産能力があります。
日本国内・外と工場をお持ちであるとのことですが、設計や技術開発はこちらが主に担当されているのでしょうか。
田中
基本的には全て我々の設計チームが設計をしています。海外に関しては、現地で開発も行う動きもありますが、現時点ではほとんど国内で開発していますね。設計も開発も人件費がかかります。開発費用を押えていく上で海外での最適地設計も取り組み始めておりますが、最新技術の共有化などの問題で現時点では一極集中で行っています。もちろん海外での販売を考えると、国々の生活スタイルの違いに敏感に対応しないといけませんので、今後は現地開発がさけて通れないし、更に進めてゆかねばならないと考えています。しかし、国内でのインフラ進化、蓄積があっての展開であると判断しています。
冷蔵庫というと、最近は開発がバラエティに富んでいるようですし、開発期間も短くなっているような気がしますが。
大和
新製品を発売する時期は大きく春と秋の2回です。その中で各シリーズ機種は1年サイクルとなります。
田中
冷蔵庫は大物の樹脂成形部品がほとんどですから、金型を作るのにも物理的に2ヶ月以上かかります。しかしそういう期間も含めて冷蔵庫は現在、8ヶ月前後で開発しています。
当然それは問題があった時の対応の時間を含めてですか。すごく短いですよね?
田中
市場ニーズに合った商品をタイムリーに開発するには開発期間をいかに短くするかがカギとなります。これは当然開発コスト削減にもつながります。我々設計チームでも開発期間短縮化に対して過去からいろいろな取り組みをしてきましたが、現在ではその短期開発の中でいかに設計品質を向上させるかに重点をおいて取り組んでいます。ところが今の開発期間では全てを試作に頼っていると間に合わないことがあります。当然、試作は3次元データを利用した光造形なども活用していますがその時間さえない場合があります。そこで試作を造らずにデータで判断できるような手法が必要になってきます。このときA N S Y SDesignSpaceのようなツールは絶対不可欠なのでしょうね。設計プロセスの中では新規部品の基本形状を決め込む時などが何度となくありますが「どちらの形状のほうが強度的に優れているか」などの判断をするためのツールとしてはAnsys DesignSpaceで今のところ十分だと思っています。
ではそのAnsys DesignSpace(以下DesignSpace)の導入の経緯についてお話いただけますか。
大和
従来は、解析専任者がいました。解析者は設計者から形状を入手し、解析モデルに落とし込んで結果を提出する。それをまた設計者が形状に盛り込む。このような流れを繰り返していました。しかしこれでは、商品化の開発ステップに連動できないという問題があって、もっと設計者自身が形状を検討する中で解析を使っていこう、という流れに変わってきたのです。そこで設計者が3次元CADを導入するタイミングにあわせて3次元CADと連携がとれてしかも簡単に操作できる解析ソフト、つまりDesignSpaceを導入することになったのです。
その簡単なソフトということですと、DesignSpace以外にもいくつか候補があったと思いますが。
大和
いろいろ候補はあったのですが、最終的に設計者が使いやすい解析ソフトということで3つが残りました。その中でタイミングよくDesignSpaceのバージョンが6.0に上がり、機能が非常にわかりやすく使い易くなったこと、採用した3 次元C A D との連携が取りやすかったことからDesignSpaceに決まりました。もともと解析ソフトは入っておりましたが、解析操作が複雑なため、設計しながら解析を行なうことはなかなか容易ではありませんでした。そこで、今回導入する解析ソフトについては、とにかく解析操作を意識せず、自分でやりたいことがCADの操作の延長で、しかもボタン一つで操作できるほど容易であることを理想としており、DesignSpaceはその目的にあっていたのです。
田中
弊社の場合は、冷蔵庫すなわち‘冷やす箱’を作っていますから、流体系、熱系の解析は、古くから取り組んでいたのですが、機構設計分野での応力や機構系解析は取り組みが遅れておりました。また3次元CADの導入も松下グループの中でも後発でした。そこで追いつけ追い越せでがんばって推進している中で、導入したのがDesignSpaceでした。3次元CADの方はSolidEdgeに決めたのですが、これとの連携もありまたDesignSpaceはそのほかのCADにもいろいろなインターフェースを持っていて柔軟性が高いように判断しました。この点も決め手の一つになったと思います。
ちなみに、メインCADをミッドレンジのSolidEdgeとした決め手はございますか。色々CADもあると思うのですが。
田中
機能的にはハイエンドCADがいいのはわかっていますが、操作が難しいため2〜3人が覚えて、その人がバリバリ使っても3次元は成功しないと思うのです。広く設計者みんなが使いこなしてこそ初めて成功して行くものでしょうから、ユーザーインターフェースが重要ですし、価格面もあわせるとミッドレンジということになりますよね。また冷蔵庫の扉を開いていただければわかると思うのですが、庫内の壁を構成している部品は真空成形という技術で造っているプラスチック成形品なのですがR形状とR形状が繋がっている形状が大部分のため3次元化の障害になっていました。しかし、それを薄肉化を含めモデル化できたのが当時のミッドレンジではSolidEdgeだけだったのです。ただミッドレンジのソリッドモデラーですと意匠面での3次元形状ではやはり限界があるので、データ互換性のある同じEDS社のUnigraphicsを併用しています。
DesignSpaceはUnigraphincsにもつながりますけれども、そういうところも考慮されていたのでしょうか。
大和
そうですね。その頃、モデルはまだI-DEASも使用していましたし、DesignSpaceはParasolidデータも使えるので、I-DEASで作成した形状がそのまま利用できることも決め手の1つになりました。
先ほどお聞きした内容ですと、工場も国内外に点在しているようですが、設計のデジタルデータ、つまり3次元CADモデルやDesignSpaceの解析結果などを工場の方に送って、情報共有するようなことはあるのでしょうか。
杉本
例えば、新しい設計の際、それが本当に構造上十分なのかを判断するツールとして、出図前に、工場部門に前の形状と比較した解析データを提示します。今まではなかなか確証を持って説得しきれなかったことをDesignSpaceや光造形を用いることによって自信を持って言えるようになってきたので、助かっていますね。そういうDR(デザインレビュー)への活用を積極的に行っています。
例えばこれはハンドルの強度の解析なのですが、次の機種で違う構造体にする時に、この解析結果と前機種の実物がありますので、実験して十分な設計であることを検証した上で、新しい形状と照らし合わせて変化量などを指標として使うようにしています。
江坂
冷蔵庫には、断熱材であるウレタンを発泡させるという特有の工程があります。断熱材が急激に膨張するのを冶具で押さえ込んでウレタンを洩れないようにするのですが、その際にドア自身にかかる負荷を検証した事例です。冷蔵庫のドアの面材には鉄板を使用するのが普通なのですが、アクリル樹脂を使ってこれまでにない斬新なデザインを採用した機種では、いろいろな応力条件に対してアクリル樹脂が耐えるのかどうかを検証しました。あえてアクリル樹脂を使ったのは、"クリーン"というコンセプトを外観意匠で実現するためで、厚みを持たせたアクリル樹脂に起こる光の屈折を効果的に見せることで、透明感や奥行き感を表現しました。構造的な課題でどうしても薄さの限界を狙わないといけない時があり、その際に上記の解析を実施しました。内容は、治具の押さえる力でアクリル樹脂が割れないための板厚検討です。部品としてはアクリルパネル単品に対して解析しています。部品を組み立てた構造体だと解析条件が複雑化し時間と労力がかかるので、まず単品での解析をすることで設計のあたりをつけました。設計者は限られた時間の中で開発しないといけないので、CAE解析を電卓代わりに使いたいのです。即決断しなければならない時に、すぐに計算して...という様に。普段は、解析専用のモデルを作って解析をする時間的なゆとりはないので、こういった形で欲しいところだけピックアップして相対評価をしています。解析結果は、設計者本人の判断を助けるだけでなく、関連部門への説明にも使用します。特にコンター図は、起こっている現象を視覚的に理解してもらいやすいという点で重宝しています。
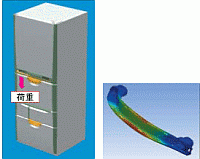
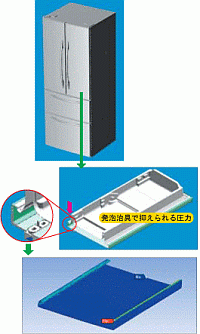
伊藤
これは、冷蔵庫ドアに取り付けられているフレーム部品で、ドアを引き出した状態でも垂直方向にかかる一定量の負荷に耐えられるよう設計されています。従来はこのような格子形状を多く入れて補強してきましたが、これではお客様が冷蔵庫扉を開けたときに見栄えがよくありません。そこでこの格子形状を廃止することによる影響を解析することにより、お客様から見えない部分でどのような補強をするかを検討したものです。この題材は、従来のフレームという測定できるものがあるために相対比較をしやすく、DesignSpaceを使っていく中で、大きな効果が出たケースです。
田中
失敗して設計変更をすれば何百万円というロスが発生するわけですから、この解析で事前にある程度方向性がわかって、ロスを無くせただけでもDesignSpaceの投資分を充分回収できたと思います。
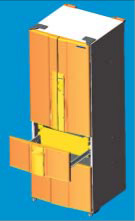
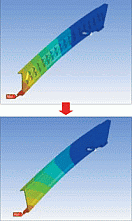
格子をとったかわりに厚みはどれくらい増やしているのですか。
伊藤
厚みは変えていません。これが最良の形状かどうかはまだ未知数ですが、最も負荷のかかるポイントをフレームに取り付けたローラー接続部周辺に絞込み、ローラー周辺の絞り形状を何パターンか検討し、解析しました。その形状により、お客さまから見える位置にある格子形状を廃止しても大丈夫だろうという予想を立てられたわけです。この格子形状がないだけでも金型加工工程が大巾に減り金型費も削減することができるんですよ。
今までカンや経験に頼っていたものを解析することによって実証して、周りの方への説得がしやすくなったなど、そういう面で実感はございますか。
伊藤
やはり一番の効果はそこですね。どれだけ手計算をしても周りの人はなかなか納得してもらえませんが、CAEでの解析結果を3次元データとして見せることにより納得してもらえることはよくあります。それに自分自身でも納得して説明することができます。
手計算をしていても、計算方法や条件面で本当にこれでよいのかという不安は付きまとってしまうのです。相対的な評価だけでもこういったツールで実証できるのはすごく便利だと思います。ちなみに、主力機種に関しては、現在は全て3次元で設計を行うようになりました。
ところで設計者の方が解析に取り組まれる際に、どこの会社でもお聞きするのが社内利用の促進や設計部門と解析部門との情報共有をどう進めるかなどといった問題があるということですが、松下冷機さんではどのような取り組みをされていますか。
大和
ちょうど松下グループの中で、CAEの競技大会を全社的に実施しようという動きがありました。課題は簡単な形状で、解析の基本操作であるメッシュ作成、材料物性値・境界条件の設定、解析結果の表示を流れにそって一通り行なうことができ、最後にそれを使って初期の形状を軽量化していくといったものでした。これを導入教育の一環として利用し、この機会に設計者の方にDesignSpaceを、一度触ってみてくださいと声をかけました。周囲の色々な方にも協力をいただいたおかげで、半強制的ではありましたが全員に参加してもらうことが出来ました。しかし、急に参加することになったものですから最初は難色を示す人もおりましたが、いざ競技が始まると皆さん真剣に取り組み、目的をもって2時間程度集中して解析を使ったことが良かったのか、少なくとも解析の印象だけは実感していただけたようでした。それがきっかけになったと思います。
田中
自信もついたと思うんです。設計者がCAEの競技会に出るなんていうことは、今までは常識的な考えではなかったのですが、実際参加してみて、私たち設計者も上位入賞することができました。
このとき、設計上で使う解析に必要なのはCAEの専門的な知識が大事なのではなくて、本当に重要なのは設計スキルだというふうに思えたのでしょう。
大和
設計者はほとんど直前に操作を覚えて参加したのですが、結果として基本操作だけをにわか仕込みで覚えた彼らが競技参加者の上位の成績を占めることとなり、ずいぶん認識も変わったと思います。その後2回目の競技会でもやはり彼らが上位入賞しました。これにより、CAEはすぐに使える! 更に設計におけるCAEの必要性を納得して頂けたと思います。その後は、競技の参加も半強制的に参加しているのではなく、皆さん本当に真剣勝負となってきたと感じています。
杉本
弊社の設計者は解析することに対して、抵抗はありません。逆に新しいことをやりたいという思いの方が強いです。だから3次元もすっと入れたのではないでしょうか。ただ、最初のやり方がわからないだけなのです。その時に競技大会のような取り組みがあって、1時間程度でしたけれども、操作の方法だけ覚えて競技に参加し、あとはそのやり方プラスαを聞きながら覚えていく、自分で触って慣れていく、そういうやり方でみんなが使えるようになっていったわけです。
江坂
その競技大会が良かったのは、課題があって、それから結果を出す方法を1から順に教えてもらったのです。例題があってその回答集というようなものがあって一連の流れを1つのシンプルなモデルで体験できたというのが大きいですね。そこで自分で境界条件を設定して、ボタンを押したら、こういうふうに解析が走って、結果が出ますよと。出た結果はこうやってExcelの資料に持っていけますよ、という一連の業務の流れが理解できましたから、あとはそれが多少複雑になっても、やることは一緒だとわかって、とても効果があったわけです。

社内競技大会(CAEの部)の様子
杉本
DesignSpaceについては応力解析だけはわかるようになってきました。次は、他の機能も使いこなせるようチャレンジしてゆきたいです。
ではおそらく次は熱応力の問題のトライアルだと思うのですが。
大和
そのとおりです。今回から競技会の課題に熱の問題を取り入れていこうと考えています。一度に全部やると混乱しますので、これまでは強度解析に絞っていましたが、既に強度解析は修得できたので
次のステップに進もうと考えています。
田中
今まで線膨張が絡むところは、ほとんど見られていないのです。
冷蔵庫は特に外装面と庫内面で温度が違います。30℃以上の高外気温でも冷凍室内は−18℃以下になっていますから、冷蔵庫扉の表と裏の温度差だけでも50℃以上の差が出てくるのです。それで扉自身がバイメタル現象により変形してくるのですが、その辺の解析がまだ未開拓の部分で、カンと経験と実験に頼っている部分です。そういったところに熱要素をどう取り入れるかが課題ですね。
伊藤
熱を始めたら、今度はアセンブリの解析データが必要になってくるので、どのタイミングでその解析に着手するかということも、非常に大切になってきます。冷蔵庫のドアの収縮を考えようとしたら、最初から解析用のデータを作っていかなければなりませんよね。ある程度の詳細な設計も必要になりますし。板が2枚合わさっているだけのものではなくて、中にはウレタンがありますので、ただ単純に温度を組み合わせてやれるというものでもないと思うのです。それが今一番やりたいところでまだ手を出せていない状態なのです。
田中
確かにDesignSpaceでは無理なのかもしれないですが、DesignSpaceは突破口で設計にもCAEがかじれるというところですから、そこからAnsysに広げていければいいのではないかなと思います。
では現在のソフトウェアの機能についてご要望や問題などがあればお伺いしたいのですが。
杉本
先に何度かでましたが、今は相対評価的な使い方しか行っていません。それは絶対値として解析結果と実験結果が十分整合がとれているデータをまだ蓄積できていないからです。本当はミッドレンジのソフトでも絶対値で評価できるぐらい信頼性が上がってほしいという思いが私たち設計者側にはあるのです。それと冷蔵庫は大半が樹脂部品なのでRが多いのです。そうなるとなかなかメッシュが上手く切れません。薄肉の所が上手く切れないとか、負荷がかかるところはメッシュを細かく切らなくてはいけないとか、解析ソフトとしてのノウハウが要求されますよね。でも使うのは設計者ですから、誰が使っても同じメッシュ、同じ結果が出るようなツールが理想なのです。そういうものが本当は設計者に一番使い易いソフトではないかと思います。
杉本
DesignSpaceでメッシュが切れなかった場合や、複雑な操作が必要になってくると、設計者は時間的に対応することができなくなってしまいます。経験がある解析者なら手早く行なえるようなノウハウ的な操作を、解析が初心者の設計者にも容易にできるようにしていきたいです。
現時点でメッシュの制御を自動で行うための対策としてはアダプティブH法を使ったメッシュの収束機能があります。これはベースの形状のメッシュが切れた場合に使えるのですが、応力を評価したい場合は、最大応力値がある程度収束した位置に来るように繰り返しメッシュを切りなおしてくれるのです。ただ1回の解析よりも時間がかかりますし、薄肉の形状やRが多いものについてはメッシュが困難であるのも事実なんです。
大和
解析者は、精度良く解析するために、いかにきれいにメッシュを切るかといった作業は当たり前と思っておりますが、それは解析者の常識であって、設計者にとっては全然当たり前ではないんですよね。
ある部位のメッシュを切るためにノウハウをマスターしたところで、次の商品化となると前に解析した人が同じ部品を設計するとは限らない。それでも過去のノウハウと同じ解析結果を出さないと評価できない。そのためには、メッシュの切り方で解析結果が変わるようであればダメだと思います。メッシュによる結果のばらつきを抑えるためにはある程度は自動化していくことも必要ではないかと思ってます。他にも、解析者だけがあたりまえと錯覚しているところがありますから、そんな溝を埋められるともっと設計者に解析が活かせるようになるのではないかと思っています。
杉本
もっと設計者に使いやすくなってくると、DesignSpaceに対してどんどん設計者から要求が上がってくると思います。それが今メッシュという壁で踏み込めないのです。是非改善してほしい所です。
まずその壁を取っ払ってあげれば次のステップにいけるでしょうし。
田中
DesignSpaceからAnsysの世界へも入っていけますよね。
DesignSpaceのメッシュで苦労していると、Ansysなんてまだまだ雲の上のようなイメージがしてしまいますから。
大和
Ansysシリーズのプロダクト全体は、大変整っていると思います。
それこそ、DesignSpace、Ansysの壁はなくなりそうですし、非線形解析や、連成解析などへの展開も今後は期待できそうだといった思いはあるのですが、最初の入り口付近でのメッシュ切りが壁になり、ソフトへの信頼性が下がるともったいないですので、そこは早く強化していただきたいところです。
杉本
例えば自動メッシュで切れない時に、このデータのメッシュを切ってくださいと依頼して、その方法を教えていただくようなことは可能なのですか。
通常のサポートの中でメッシュを切れないモデルをいただいて、我々の方で検証することはもちろん可能です。上手くいかない場合は、ラインの分割数を変えてみたり、Parasolidに落としてみて、形状自体が問題なのか、データの種類が問題なのか等を確認していきます。それでも解決できなければ今度は開発元の技術サポートとともに対応させていただきます。そうやって、バージョンアップの改善項目として取り上げていくこともできますから。ではそのほかに、サービスやサポートの面でもご要望がありましたらお聞かせ下さい。
江坂
マニュアルを例題と解き方みたいな形で書いてもらえると、理解しやすいと思います。例えば、応力解析のプロセスがあって、その中で各機能が説明されていれば、わかり易いのですよね。
田中
保守料なども含め高価なソフトウェアを使っている以上、やはり結果を出さなければいけません。どれくらい使い、稼動させていて、効果を出しているか?というところに対して、まずDesignSpaceで結果を出せないと次のAnsysに進めないのです。ですから、まずは既存のユーザーがいかにソフトを使えるかという部分を強化していただければありがたいと思っています。
大和
まだ全ての機能を使いきれていないのが現状です。それでもソフトはバージョンアップして年々良くなっていますよね。新機能の説明はバージョンアップセミナー等で行なっていただいておりますが、我々が特に説明していただきたいのは、マニュアルに書いていないような隠れた部分です。その中でも、解析結果を用いた第三者に見せる機能のところはいろんな事例を紹介していただき、機能ともども教えていただきたいところです。DesignSpaceのアニメーション機能を使ったプレゼンテーションの方法もあればよいですね。
ありがとうございます。そういったマニュアルやセミナーのご提供も今後検討させていただきます。ソフトの方で問題はまだまだあるかもしれませんが、我々のサポートの方で出来る限り対応しまして、実際の機能面で足りないところは、開発のスタッフの方に要望として出させていただきます。DesignSpaceで希望されている機能というのは、どこのお客様でも同じような面がありますので、そういったところは開発も早いと思いますから、我々も今後も努力させていただきたいと思います。松下冷機株式会社の皆様にはお忙しい中インタビューにご協力いただきまして誠にありがとうございました。この場をお借りして御礼申し上げます。
松下冷機株式会社の皆様にはお忙しい中インタービューにご協力いただきまして誠にありがとうございました。この場をお借りして御礼申し上げます。
「Ansys Product News2003 Autumn」に掲載
関連情報
関連する解析事例
MORE関連する資料ダウンロード
MORE-
コントローラ&センサのデータ駆動型シミュレーション
~データ駆動によるロボットのモデリングと制御設計~
-
EMCのお悩みありませんか? ~EMCソリューション~
-
炭素回収・利用・貯留におけるCO2の削減 ~Ansys Fluentによるソリューション~
~Ansys Fluentによるソリューション~
-
仮想環境で実現するマシンビジョン設計~Ansys Speosによるカメラ&照明最適化ソリューション~
~Ansys Speosによるカメラ&照明最適化ソリューション~
-
構想設計ですぐにリアルタイム検証 ~解析専任者ゼロでも使いこなせるAnsys Discovery~
~解析専任者ゼロでも使いこなせるAnsys Discovery~
-
流体機器設計の新たな一歩
~Ansys Discoveryで加速する設計改革~
-
筐体の冷却性能を構想設計から見える化 (手戻りを削減できる)
~Ansys Discoveryで始める電気筐体製品の設計改革~
-
若手でもすぐに使えるリアルタイム解析 (勘と経験からの脱却)
~Ansys Discoveryによる30名規模メーカーの設計改革~