解析事例
ジェットエンジンやガスタービンにおける解析について
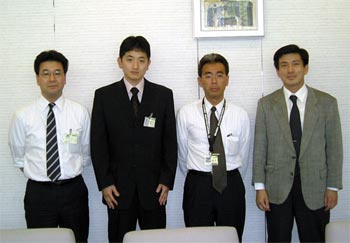
今回のインタビューにご協力下さいましたお客様は、石川島播磨重工業株式会社 航空宇宙事業本部 技術開発センター エンジン技術部の皆様です。
(写真左から永戸 信孝様、柳谷 信孝様、篠崎 正治課長、藤村 哲司課長)
石川島播磨重工業株式会社(以下IHI)様は、1853年に石川島造船所として創業され、その後150年に渡り当初の造船業から橋梁、プラント、そして航空宇宙分野にいたるまで幅広く多彩な事業を展開されてきました。「技術をもって社会の発展に貢献する」を経営理念として掲げ、身近な暮らしを支える技術から、産業分野に利用される技術、そして、地球を離れて宇宙レベルの技術まで、信頼性の高い製品・技術の提供に積極的に取り組まれています。特に1945年に日本で最初のジェットエンジンを完成させ、日本航空機工業の発展に大きな役割を果たしてきた航空宇宙事業は、それら最先端の技術の結集と言えるでしょう。
現在、皆様の所属されるエンジン技術部のある田無工場をはじめ、瑞穂工場、呉第2工場、相馬工場の4工場において、エンジンの製造、組み立て、試験、修理までを一貫して行われています。
(以後IHIの皆様の敬称は略させていただきます。)
まず航空宇宙事業本部での取り扱い製品をご紹介いただけますか。
藤村
主な製品がジェットエンジンやガスタービンのような回転系のものです。例えば航空自衛隊のブルーインパルスに搭載されているF3ターボファンエンジンや、民間航空機用エンジンとしてA320などに搭載されているV2500ターボファンエンジン(写真下)があります。これは、日本、英、米、独、伊の国際共同開発事業として開発、量産されたもので、IHIとしては最前面にあるファンの設計を担当しています。最近ではGEとRSP(Revenue Share Partner)を結んで、CF34など70〜100席ぐらいの飛行機に積む最新のエンジンを開発中です。
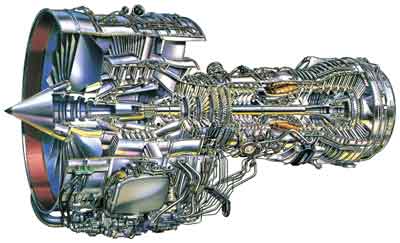
提供:財団法人 日本航空機エンジン協会
そういうエンジンはサイズで言うと様々なのでしょうか。
藤村
F3のエンジンの直径が約60cm、V2500ですと約1.6mですね。今IHIとGEが共同開発している最大のエンジンがGE90でして、その径が約2.5mで、B777に搭載されているエンジンです。これは世界最大級で、推力は10万ポンドになります。ジャンボのエンジンが約45000から50000ポンドですから、それの2倍の推力が一瞬にして出てしまうというものです。そのような航空用のジェットエンジンは、発電用にも転用できますので、それはガスタービンプラント事業部が発電機とセットにして販売しています。非常にコンパクト、低燃費、低騒音、低振動で客先からも好評です。
ガスタービンとジェットエンジンは、構造的には殆ど同じなのですか。
藤村
基本的に、圧縮機、燃焼器、タービンからの構成というコンセプトは変わりません。それぞれに最新のシミュレーション技術を応用して最適化を推進していますので、より軽量で信頼性が高く、長寿命であるものを開発しています。シャフトの回転数は年々上がっていまして、かつては回転翼先端の周速が450(m/sec)だったのが、今は500、600と増加しています。それを上げていくと、ディスクと呼ばれる回転円盤部の強度が非常に厳しくなりまして、シミュレーションを徹底的に活用しています。
そのような解析は技術開発センターの方で行なわれているのですね。
藤村
はい、技術開発センターの他に実際のエンジン開発を担当する部門が、民間エンジン事業部、防衛エンジンシステム事業部、ガスタービンプラント事業部として並列で組織されており、これらの事業部の設計部門でも同様の解析を実施しています。
いわば解析手法やその指針をこちらで作られて、それをもとに設計現場の方がCAEを使われているというような感じでしょうか。
藤村
そうですね。我々の方で、エンジンの構造強度に関わる解析技術の整備・向上や技術支援取りまとめを行うというのが一つの使命です。また、温度の予測は構造解析とは切っても切れないので、温度予測技術も我々が見ています。当然それに対して設計に必要な電算ハードやソフトの利用促進も業務内容となっています。
航空宇宙事業本部全体ではどれくらいの方がCAEをやられているのですか。
永戸
実際のAnsysユーザーは約150名です。設計と解析のボーダーが明確ではないところが殆どで、設計として図面を描く人もCADを使う人も解析をやるということが定着しています。逆に我々のグループは、解析が主業務ですので、全体から見ると特殊な職場ですね。
では、Ansys導入の経緯をお聞かせいただけますか?
永戸
平成3年の3月だったと思うのですが、その頃ホストコンピュータ全盛の時代でNASTRANを利用していました。ただ、プリ・ポストプロセッサーとの互換性やホストコンピュータの使い勝手などが問題でしたので、Ansysを検討しました。Ansysは、ポスト処理の時にデータを変換しなくてもいいですよね。他のソフトですと、変換に時間が結構かかってしまって、それにコストがかかってしまうということがあってUNIXと共にAnsysを導入したわけです。Ansys自体が回転系の部分の計算機能が優れていましたし、非線形としても評価できたということもあります。
では実際はどのような解析を行なわれているのですか。
永戸
基本的にはエンジン全体の構造の各部品すべての構造解析を行っています。ディスクからブレード、フレームまで、殆どの部品についてですね。単品だとズームアップの解析、3次元の詳細なソリッドモデルの解析です。そうはいっても最近は単体のみよりも全体の解析も増えてきています。
篠崎
UNIXマシンを使えるようになったことやコンピュータの性能自体が上がったことで、精度を上げるために大規模なモデルになってきているということが言えますね。
CADの利用や解析モデル作成はどのようにされていますか。
篠崎
CADはUnigraphicsを使用しています。設計者も解析者も基本的に同じですから、Unigraphicsのデータを有効に使おうとしているのですが、我々は航空エンジンの信頼性について細心の注意を払っておりますので、メッシュをかなり細かく切っていかなければならないんですね。それから、最初の概略的なところはテトラで切ってもいいのですが、最終的に寿命を評価するようなところでは、必ずヘキサのモデルを使っています。その6面体メッシュがUnigraphicsのデータですぐに作れないので、今そこが非常に苦労しているところです。
先程のモデルの話で、設計者の方がそのまま解析をされるということですが、メッシュをちゃんと切れるように、設計の段階で解析のことは念頭においてモデリングをされているのでしょうか。
永戸
3DCADが一般的に広まって、効果が随分出ていると思うのですが、CAD/CAM/CAEの中で、CAEの部分はあまり恩恵を受けていないと思います。3次元CAD形状をそのまま使うことが実際は難しいわけですから。基本的には3次元CADは、製品と殆ど同じ物を作るためにあるので、設計者はCAEまで頭が回らないわけです。例えば、微小サーフェスがあると、自動メッシュで切るとやたら細かく切ってしまいますし、それを避けるために構造強度上関係のない穴は無視するとか対策が必要ですね。今は解析前にある程度直してから、解析に行くといったことをやっています。
Ansysで構造解析をする場合に、メッシュはAnsysで切られているのですか。
永戸
3通りありまして、1つは昔から使っているI-DEASとかPATRANでメッシュを切るというのと、Ansysの中でParasolidを読み込んでメッシュを切るというのと、もう一つはAPDLを使ってパラメトリックな解析をやってしまうということです。
APDLを相当使っているのですね。
篠崎
設計段階のパラメトリックスタディでは、いろいろな計算が必要ですから、そこの部分でよく使っています。ある程度トポロジーが決まっていればパラメータの設定だけで解析ができますから便利ですね。その機能は他のソフトにないですよね。
永戸
導入当初の期待以上に非常に使いやすいです。特にFORTRANライクというのが、我々にとってはありがたいです。
簡単にループさせたり、数式を入れることもできますし。荷重条件に圧力分布がついたり、温度分布を仮想的に決めるような場合にも利用しています。
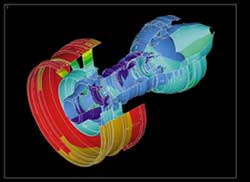
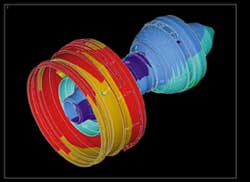
図1.エンジン全体解析シェル要素
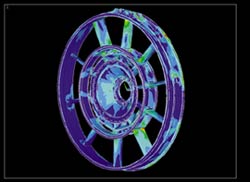
図2.フレームソリッド要素
そうですね。Ansysの場合はAnsysのコマンドを覚えていくと、自動的にAPDLも覚えていくというような感じで出来ますから。
ところで、解析と実験を比較されるとどうですか。
篠崎
構造解析についてはメッシュを丁寧に作りさえすれば、殆ど正確に合います。静解析の分野では問題ないです
こういう風にやれば整合性があるという指針があるわけですね。
藤村
そうですね。静解析や振動解析は並行してエンジン試験を開発途中で行いますので、それと必ず照らし合わしの検証をするわけです。それがノウハウとして積み重ねられていると思います。そういう社内のノウハウは先程のメッシュの細かさについてもそうですし、設計基準という形でもあります。
そのスキルの伝承のようなものは、どういう形で行なわれているのでしょうか。
藤村
設計基準があり、その基準に従って行なっていくということです。今はイントラネットを使って見られるようになっています。
解析の方はこれからですか。
柳谷
解析例は私が担当していまして、整備したものをサンプルとしてイントラネット上で公開しています。あまり言葉で書かれてもわからないでしょうから、過去に行った例えばローターの解析のメッシュはこうですよ、というような形で掲載しています。ある程度はたまっているのですが、まだ十分ではないので、これから増やしていきたいですね。
篠崎
Ansysの使い方に関しては我々の方でイントラネット上にまとめていて、そこを見るとAnsysの情報が大体わかるという公開の仕方をしています。その中にはAnsysでの不具合や、やってはいけない事なども含めて書いています。
約150名が使われている背景には、そういう基盤があるのですね。それで質問もある程度抑えられるんですね。ところで、衝撃解析の例でバードストライクというのがありますが、これは必須なのですか。
藤村
エンジン開発の成否に関わりますし非常にリスクが高いので、ファンを設計する場合には必須です。ファンを設計して、そのファンのブレードを製造して試験をするまでに長期間かかるのですが、そこで不合格になってまた作り直してということは、時間的に不可能です。一度でOKをとるためにはシミュレーションは絶対欠かせないのです。
永戸
バードストライクがなぜ重要かというと、一番鳥を吸い込む場面というのが離陸と着陸の時で、非常に飛行機が不安定な時なので、そこで吸い込んでしまって、離陸の時に急にエンジンが止まってしまうと、危険です。信頼性、安全性、危険の回避という意味でバードストライクはやらなくてはいけないのです。
藤村
具体的にはエンジンの大きさにもよりますが、1.5ポンドの鳥が4羽入っても推力の低下が25%以下のこと、といった規定があるのです。
では実際の解析事例を見せていただけますか。
永戸
これはIHI独自に研究しているエンジン全体をシェル要素でモデル化したものです。モデルは別ソフトで作って解析はAnsysで行いました。軸対称部で、断面を作ってまわすということにはAPDLを適用しています。そういうのは精力的に取り入れていますね。例えばエンジン全体を支えるフレームの部分ですが、ストラットと呼ばれる半径方向にのびた柱が立っていて、それが全体の荷重を受け持つので強度的に厳しくなるために部分的に取り出して詳細にソリッドでメッシュを切っています。付け根の黄色になっている部分です。(図1、図2:エンジン全体解析シェル要素、フレームソリッド要素)
篠崎
全体のモデルをソリッドでモデル化すると節点数が増えますので、シェルで全体の状況を見て、その後ズームアップして詳細にソリッドモデルで計算をしているということです。
永戸
この場合は弾塑性も入れていて、拘束している場所にギャップ要素も入っているのです。エンジン全体を支える部品をピンで支えていて、それが機体の部位につながるようなイメージでして、ピンのところにギャップ要素を必ず入れなくてはいけません。それでギャップ要素の非線形性と、弾塑性の非線形性で、CPUを2つ使って、丸3日ぐらいかけて計算しているのです。
これは構造静解析ですが、非線形や振動解析についてはどうでしょう。
永戸
振動解析はジェットエンジンにとって必須のことですが、代表的なものは翼とディスクを一体で解析するサイクリックシンメトリ解析です。例えばジェットエンジン最前列のファンローター部ではファンブレードとディスク部分を一体でメッシュを切り20何セクターのサイクリックシンメトリで評価しています。
篠崎
振動解析でも、振動応力の評価というのはある程度できないといけません。最近では静止部の振動解析もサイクリックシンメトリを取り入れていますね。
永戸
最近はジェットエンジンも軽量化しないといけませんので、限界設計ということでかなり厳しい条件下で弾塑性の計算もしています。(図3:ボルト/フランジの弾塑性解析)これはその例なのですが、フランジがあって、ボルトとナットの断面を見ています。普通締結構造では、フランジは開かないように厚くしますが、ジェットエンジンの場合は軽量化のためにそういうことを行わないで、開いても機能さえ持てば良いというような設計を前もってするわけです。それで弾塑性を扱っていまして、少しずつ内圧がかかるとともに開いて応力が上がり塑性が始まるということを検証しています。これは、極限状態なので、安全率を考えたときに突発的に負荷が掛かった時にでも、機械としての機能は失っても、壊れたり2次損傷を与えるようなことは起きてはいけないという設計方針なのです。そういう究極の条件を解析しているわけですね。こういう部品と部品の間は全部ギャップ要素を使っているので、これもかなり計算時間はかかっています。
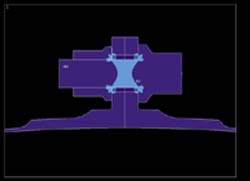
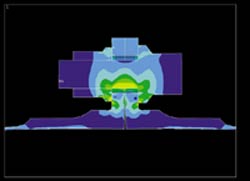
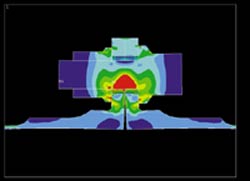
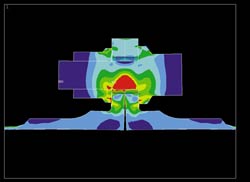
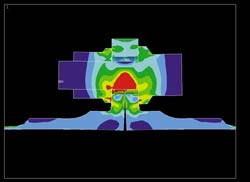
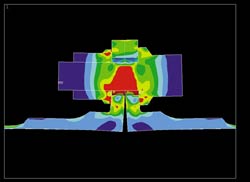
図3.ボルト/フランジの弾塑性解析
今後は材料の定数はある程度用意しておいて、弾塑性の標準的な荷重のかけ方みたいなものを用意しておけば、少し楽になるのではないですか。
永戸
そうですね。材料で言いますと、各エンジンで使う材料が変わってきます。例えば、エンジンの開発のサイクル自体が長いですし、同じクラスでも、作り方、たたき方が違って、強度が変わったりもするので、なかなか材料の標準化というのは難しいですね。
特殊な材料とかもあるのでしょうか。
藤村
普通には使わないものばかりですね。ニッケル系合金やチタンなど高価なものになりがちです。
ジェットエンジンだと、信頼性と言う意味で試験の期間も相当取らないといけませんよね。
藤村
初号機のエンジンが試験に入ってから、型式証明を取るまでが1年程度です。
その後の飛行試験も入れると2年ぐらいでしょうか。
永戸
型式承認を取る前に、耐久試験をやらなければならないのですが、エンジンを作る前に個々の部品でいろいろな試験で確認はしていて、最後にエンジンで成り立つことを確認するためにセルでずっと何日も、あるいは何ヶ月も回しっ放しの耐久試験をして、それで型式承認がおりるという形なのです。
藤村
最後の1年間でいろいろな不適合が起こるようだと困るのです。開発期間がどんどん延びてしまいますから。最初のエンジンが作られるまでの間にシミュレーションや試験を徹底的に実施して、エンジンとして組み立てた後に不適合がないようにしているというのが今の体制です。
篠崎
開発期間が短くなると十分な試験期間が与えられませんから、基本的にはシミュレーションの世界で試験の条件を最小限にしています。シミュレーションにしても、いかに簡単にモデルを作れるか、計算時間を短く出来るかとかいろいろなスタディを行っているわけです。
基本的には設計サイクルの短縮化が、シミュレーション必須の状態にしているのですね。
永戸
シミュレーションの回数が増えれば増えるほど、いいものが出てきている気がします。
藤村
試験は条件が何種類も出来ませんから、一番クリティカルな条件だけに制限されます。ですから様々な条件を検討するにはシミュレーションに頼るしかないですね。
試験にお金がかかるものほど、CAEは重要視されているというところはありますよね。実際Ansysを使われていて、便利だと思われる機能などは他にございますか。
永戸
使いやすいのはポスト処理です。極端な例ですと計算条件が100種類ぐらいある場合もあるのですが、3次元のモデルですと、様々な角度から見たいのでポスト画面がたくさん必要なのです。それを手作業で出力していたら日が暮れてしまうので、APDLで効率化を計っています。
柳谷
コマンドとGUIの両方があるのもいいですね。最初はGUIの方が取っ付きやすいのですが、使っているうちにGUIで探すのが面倒になってくるのです。コマンドに慣れてくれば、そちらの方が早いですから。
永戸
しかし、Ansysの画面で他のソフトと比べて遅れているなと思うところは、アイコン化です。最近はアイコンで大抵のことは出来るようになっていますけど、Ansysはまだメニューを追って行かなければならないですね。よく使うコマンドを登録できるとかという機能があればいいのですが。
Ansys7.0から部分的にですが非常に使いやすい環境を採用し始めています。まだ全ての機能がそのGUIになっているわけではないので、実用化には時間がかかりますが、期待していただければと思います。
他にAnsysやサイバネットに対するご要望がありましたら、お聞かせください。
永戸
汎用ソフトはAnsysでいいのですが、独自の専用ソフトも考えなければならないと思っています。APDLもその手段ですが、今後Ansys Workbenchのようなものでカスタマイズが出来るのであればその辺のサポートを期待しています。それから、やはり3DCADデータを読み込んで6面体の自動メッシュが切れるプログラムを作っていただきたいと思います。今1ヶ月単位でメッシュを作る作業をしていますが、そこは何とかしないと我々も大変なことになってしまいますし。
また、非線形のギャップや弾塑性で計算が何日もかかるということがありますが、モデルはどんどんエスカレートしていくので、PCGなど高速化についてもっと力を入れて欲しいと思います。時代の流れ的には並列処理ですよね。CPUの増設分に対するパフォーマンスを上げて効率化を図って欲しいです。
並列化に関しては、まだCPUの数に比例したスピードが出ていないです。グリットに関しては、DDSという機能がありますが、線形解析の領域では効率出るのですが、非線形の方はまだ十分なスピードアップが実現できていませんので、そのあたりの開発や検証を今後も積極的にやっていきたいと思っています。
永戸
先程話がありましたが、ギャップ要素の収束性も要望としてあげていただきたいです。以前より改善されていますが、いまだに収束させることが仕事になっている人もいますので、そこは何とかして欲しいですね。ポスト処理でも、今後モデルが大規模化してきますので、描画の処理速度もパワーアップしていただきたいと思います。
機能に制限がかかりますが、高速なポスト処理の機能はあります。ただ、絵の表面のデータしか持たせないで軽くしているわけなんですね。大規模でも表面の絵だけだったら早いのですが、Ansysの選択機能は使えなくなってしまうので、良し悪しでしょうか。
いろいろとご要望をいただきましたので今後の開発に反映させていただきます。石川島播磨重工業株式会社の皆様には、お忙しい中インタビューの時間を作っていただき、誠にありがとうございました。この場をお借りして御礼申し上げます。
「Ansys Product News2003 Summer」に掲載