解析事例
DesignSpace での解析時にはアダプティブメッシュを標準で使用。設計者が使うのであればメッシャーが強力なことがより重要
今回のインタビューにご協力していただいたお客様は、株式会社日立製作所自動車機器グループ事業企画本部情報システム部の佐藤雅之様(写真左)と梅村茂正様(写真右)です。株式会社日立製作所自動車機器グループ様(以下日立自動車機器)は、オルタネータやスタータ、インジェクター等から、自動料金収受システムを含む車載マルチメディアシステムまで、自動車の電装部品ほとんどを手がけている会社です。佐藤雅之様と梅村茂正様は日立自動車機器の中で、CAD ・CAE 等のソフトウエア選定に関わる業務をされており、その中でDesignSpace を設計者用CAE ソフトウエアとして検討していただきました。現在は本格的に導入していただき、既に日立自動車機器内の多くの部署で利用していただいています。
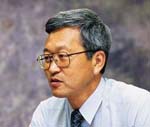
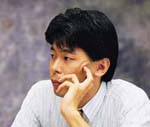
(以後、佐藤様、梅村様の敬称は略させていただきます。)
日立自動車機器の製品カタログを見せていただきましたが、ほとんどの電装製品を扱われていますね。
佐藤
私どもは、日立の中でも自動車機器グループとして、自動車業界のTier1メーカ*になるという目標を基に、日立の技術をいろいろな形で自動車関係に応用していこうということで研究開発を進めています。
ほとんどの自動車会社に製品を提供されているのですね。
佐藤
日本だけでなく、ヨーロッパやアメリカなど全世界の自動車メーカさんとお付き合いがありますね。それから、自動料金収受システムなどの道路交通システムの情報系製品まで幅広く提供しています。初めは家電製品の設計開発を行っている中で、自動車電装部品であるモータの開発を行っていました。その後徐々に手を広げ、現在ではグループとして独立しています。電気自動車用のモータなどもかなり昔から実用化しています。
その中で、佐藤さんと梅村さんはどのような業務に携われておられるのですか?
佐藤
我々は、グループの事業企画本部情報システム部に所属しておりまして、グループ内で使用する基幹機械系ソフトウエア、例えばCAD とかDesignSpace の様なソフトウエアの選定と普及業務を行っています。最近は日立の中でもコンカレントエンジニアリングなど情報システムを利用した仕事の仕方が必須となっています。そのような業務目標に有効なソフトウエアの選定も行っているのです。
かなり責任重大な業務ですね。
佐藤
その通りです。CAD ・CAE だけでなく、CAM ・CAT も含まれますが、我々はどの様なプログラムが世の中に存在するのかを常にウオッチして、我々の製品設計や生産に対して利用可能か、有効なのかをを調べなくてはいけません。その中で有効なソフトウエアについてトライおよび確認し、良いものであれば工場として採用していくというような業務になります。ですから選定を誤ると会社中で大変な問題となってしまうわけです。
その中でDesignSpace を選んでいただいたわけですね。
佐藤
その通りです。選定は梅村が一人で全部行いました。
DesignSpace 選定の経緯をお話しいただけますか?
梅村
経緯はCAD の選定から始まるのですが、自動車業界は一般的にUNIX 系ワークステーションの3D- CAD を使用していますし、我々もUNIX 系の3DCAD をいくつか使用していました。しかし全設計者に使ってもらうという目的から数多くそろえる必要があったため、基幹3D- CAD としてSolidWorks を選びました。当時としてはかなりの冒険だったと思います。しかし、かなり慎重に選びました。自動車業界とのおつきあいからCAD データが利用できなければならないし、工場や設計者の人に使ってもらう上で問題が起きてはいけませんし、効率が上がらなければ意味がありませんからね。
そこで解析ツールをどうするかという話が上がったわけですね。
梅村
UNIX 系の3D- CAD であれば、普通有限要素法の構造解析プログラムはオプションとして存在しますがSolidWorks にはそのようなオプションがありません。そこで、従来の解析プログラムにデータを変換して計算する必要が有りました。しかし設計者が個々に3D- CAD を使い始める事により、3D モデルを設計者自身が作成できるようになるわけですから、あとはSolidWorks の3D データに対して、解析に必要なメッシュ・境界条件等を簡単に設定できるような解析プログラムさえあれば設計者でも解析が可能と思いました。それがDesignSpace 選定の始まりです。
何年前ぐらい前から始めたのですか?
梅村
選定はDesignSpace のバージョンが確か2 のときだったはずです。それからスタートして、その後バージョン3 が出てきてウイザード機能が採用されて、使いやすくなったと思いました。そして評価用に正式に購入し始めたのは、バージョン3 からです。我々情報システム部門と主要な設計部門に数本です。まだアセンブリが機能として無かった時期です。自動車機器グループとしては、DesignSpace にアセンブリ機能が無ければ意味がないことは既にわかっていたのですが、今後アセンブリ機能が入ってくるという前提で、評価してもらいました。もちろんアセンブリ機能はできるだけ早く必要だったので、並行して開発要求を出しておりました。
実際に評価後の選定のキーとなった機能は何でしょうか?
佐藤
一番大きいのはメッシャーが強力であったことですね。設計者に使用させることが前提でしたから、メッシュが切れなかった場合はどうするか、という対策に頭を使わせたくなかったのです。この様な作業は設計者にとって無駄ですし、この様な作業が必要であると、設計者が使わなくなってしまうことは目に見えていました。メッシュはどのようなモデルでもとりあえず切れてくれなければならない。切れたならば、解析中に止まってはならない。解析作業が途中で止まった時のための対策を知らなければ使えないソフトウエアでは意味がなかったのです。
かなりの数のモデルを評価されたのでしょうか?以前解析事例としていただいていたオルタネータのカバーなどは、単体部品といってもかなり複雑だったようですが。
梅村
評価したモデルの数はそんなには有りませんが、フィレットを付けてみたり、微小エッジを追加してみたり、一つの部品上でもかなり細かく変更して評価していました。
他のソフトウエアも評価されていたと思うのですが。
梅村
もちろん行っていました。他のソフトには、解析の専門家として魅力のある機能を持つものもありました。ただそのような機能は、専門的に解析を行う上では融通性のある機能だと思いますが、使用者へのトレーニングを含めて考えると無理があります。使用者は設計者ですから、どのようなメッシュを切れば良いのか等を考えさせるのは負担が大きいです。ですから自動でメッシュのコントロールを行ってくれるアダプティブメッシュは重要な機能として評価しました。この機能を始めに開発を約束してくれたのは、DesignSpace だったと思います。この機能の搭載を約束してくれたことが、選定に対してかなり大きな意味を持っていました。我々日立自動車機器では、このアダプティブメッシュを標準で使用してもらうようにしてもらっています。時間のかかる解析にはなりますが、メッシュ作成に試行錯誤する時間ほどではなく、計算中は別の仕事をしていればいいわけですから。
DesignSpace のWizard 機能を含め、トレーニングが少なく済むため、設計者への手離れが良いと我々も多くの担当者から伺っています。
梅村
他の汎用ソフトだとこうはいかなかったと思います。シェル要素とかビーム要素とか、バネ要素はこう置き換えるなどのトレーニングは不可能です。従来のCAE だと、トレーニングを含め導入後1 年以上は効果が出ないケースがよくありますよね。しかしDesignSpace だと、昨年だいたい50 名ほどトレーニングを受けてもらいました。やる気のあるなしにもよりますが、次の日からもう結果を出している人もいます。昔と比較すれば格段に早いですよね。
我々がDesignSpace をご紹介するときに、お客様がFEM の経験者や専任者の方ですと、ビーム要素があるかとかバネは使えるのかなどFEM固有の機能の話になるときがあります。設計者の方であればそのような置き換えは行わないのでしょうが、どうしてもFEM をよくご存知な方であれば自分で使用するときのことを考えてしまうようですね。
佐藤
そうですね、我々の会社の中でも経験者と未経験者では評価が極端に異なっています。しかしこれは設計者の道具ですから、これを専任者が行っている解析すべてをまかなおうと考えているわけではありません。
実際業務として使い始めたのが、昨年末ぐらいからですね。
佐藤
そうですね。バージョン5 から本格的に導入を始めました。今は38 本入っています。
かなりの数ですね。設計の方が実際に行われている解析事例を何か見せていただけないでしょうか?
梅村
これはエアフローセンサーと呼ばれる、ホットワイヤー型のセンサです。(写真1 )自動車の燃料の混合比を制御するために、空気の流量計が必須なのですが、空気中にワイヤを置いて、そのワイヤに電流を流すと、抵抗から発熱し暖まります。ワイヤ周りの空気に流れがあるとワイヤー温度が下がる訳です。つまり、流速が早いと温度が下がり、遅いと温度が高くなる。このワイヤーの温度を一定に保つように電流を制御すると、その電流値から、逆に空気の流量を算出できるという装置です。
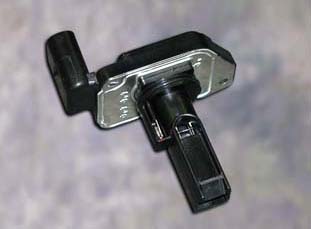
写真1
佐藤
このセンサはエンジン近くに取り付けられます。ご存じのようにエンジンは温度の変化が非常に激しい。このセンサ周りもエンジン動作時は120 ℃近くになりますし、エンジン停止時も、厳寒地では−30 ℃近くまで下がってしまいます。さらに、本センサは単一材料ではなく、樹脂や金属など大きく線膨張係数が異なる材料の部品が組み立てられたパーツです。異種材料が組み合わさったパーツを今お話ししたような温度差の中で使用すると、熱応力が発生します。自動車で使用されるパーツですから、この温度差が何回も繰り返されるので、熱サイクルでの疲労寿命が問題になります。この解析事例は、温度差による応力の高さを計算し、長期的な疲労寿命を予測するために行いました。(図.1 、図.2 )」
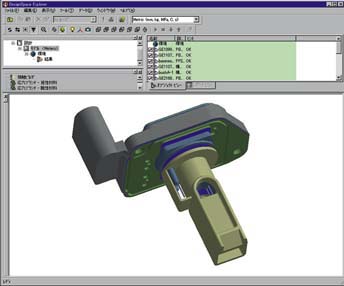
図1
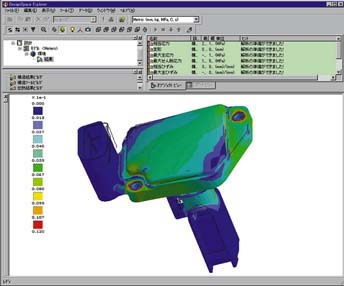
図2
実際にこの様な解析が設計者の中で行われてきて、いろいろ予測しなかった問題等有りますか?
梅村
とりあえず答えが出るのも善し悪しだと言うことがわかりましたね。つまり間違った条件を設定しても、答えが出てくる。そしてそれらしい結果が表示される。すでに40 本近くのDesignSpace が設計部門にインストールされていて、設計者が自由に使用できる環境にあるわけですから、我々のような経験者がすべての解析結果を確認することは不可能に近いのです。設計者はそれを正しい結果だと信じて、設計に利用してしまうことが非常に怖いと思っています。この前設計者が解析した結果をみたときに、パーツ同士が離れていなければならないモデルが、くっついて解析されていました。DesignSpace のアセンブリに使うボンド機能が働いてしまったのです。その部分はCAD の作図段階で微少な隙間をあけていたのですが、DesignSpace の接触トレランスに引っかかるほど微少な隙間だったので、ボンド機能が働いてしまい、結合状態で解析されていたのです。
佐藤
結果がおかしいと我々に相談してくれたから、解析条件がおかしいと解ったのですが、これが相談されずにそのまま他のところへ報告されると思うと、怖いと思います。設計者の人は解析が正しく行われたかどうかはゆっくり見ないですし、注目している部位の数値にしか興味がないことが多いわけですから、全体的に軽く見て、「まあこんな物か」で終わってしまうことが多いですからね。
梅村
昔は裏でこっそりデータを見ては、注意をしていたのですが、最近はユーザが増えてチェックし切れていないです。
そのような注意を含めたノウハウのような情報は、社内で管理したり公開されていますか?
佐藤
はい。いろいろなノウハウ的な内容や注意事項も含めて、イントラネットできるだけ公開するようにしています(図.3 )。後はいかに読んでもらうかが問題ですけどね。このようなベースを作って、後はみんなでどんどんやってほしいと思っています。我々は次を探さなければならないわけですから。
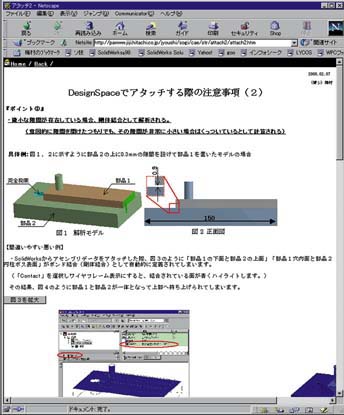
図3
使用されている設計の方からの要望等は多いですか?
佐藤
いろいろあります。特に接触解析で、今は接着か滑りかのどちらかしかできませんが、離れたりとか途中で接触したりとかの解析ができないのかと言うような問い合わせは多いですね。それから特異点の問題。やはり特異点の問題は有限要素法を使用している限り避けられなくて、その説明を設計者にしなければならないことがあります。
あれを納得させるには時間がかかりますね。
佐藤
何か特異点除去装置のような機能が有れば楽なのですがね。
梅村
それからポスト機能がもう少し豊富だと良いのですが。ブランチ機能を使用してモデル変更したり条件変更したりして解析が複数できるのは良いのですが、比較するときに同時に絵が出ないことが寂しい。さらにグラフが出なかったり、リストが出なかったりとか有りますね。
佐藤
メモリー不足やディスク不足で泣くときもあります。この辺の制限も無い方が良いですね。
ポスト機能は早く改善すべきところですね。設計者の方に使っていただくわけですからなおさらですよね。ところで、最近はAnsys の方もご購入いただいているようですが。
佐藤
Ansys/Ls- Dyna ですね、まだ買ったばかりですが、部品の衝撃解析に使えないかと考えています。
車の衝突時での影響などを評価するためですか?
佐藤
いいえ、部品の動作時での影響です。電磁バルブであるインジェクターという燃料を噴射する部品があるのですが、この部品は燃料噴射のタイミングでバルブががちゃがちゃとぶつかっています。その当たっている部分で応力がかかったりします。またスタータでは回転と同時にギアが飛び出しリングギアに当たってクランキングしますから、そのような衝撃を受ける部品の解析に利用しようと考えています。この様な解析は複雑なのでさすがにまだ設計者が簡単にとは言いませんが。
今後の展望や夢とかは有りますか?
佐藤
夢と言われると難しいですが、樹脂流動の分野も取り組みたいと思っています。さらに、樹脂流動による分子の配交性とかそのようなことまで考慮した解析までやれたらなと。成形された物にさらに何かが被さり製品ができあがる。その課程で温度の状態が変化して応力が発生してさらに残留応力となってなど、こんな風に製造プロセスとリンクした解析が簡単にパパッとできれば良いのですね。
大変ありがとうございました。
株式会社日立製作所の皆様には、お忙しい中インタビューの時間を作っていただき誠にありがとうございました。この場をお借りしお礼申し上げます。
「Ansys Product News2000 Autumn」に掲載
関連情報
関連する解析事例
MORE関連する資料ダウンロード
MORE-
剥離・接合強度評価ソリューション ~Ansys Workbench Mechanicalで実施できる剥離解析~
-
レーザー集光の高温レンズ歪みを克服するAnsys連携ソリューション
-
周波数応答解析×自動抽出で干渉チェックを高速化
-
直観的な操作で無線/デジタルフィルタの設計・最適化を支援する〜Ansys Nuhertz FilterSolutions〜
-
流体機器設計の新たな一歩
~Ansys Discoveryで加速する設計改革~
-
筐体の冷却性能を構想設計から見える化 (手戻りを削減できる)
~Ansys Discoveryで始める電気筐体製品の設計改革~
-
若手でもすぐに使えるリアルタイム解析 (勘と経験からの脱却)
~Ansys Discoveryによる30名規模メーカーの設計改革~
-
構想設計ですぐにリアルタイム検証 ~解析専任者ゼロでも使いこなせるAnsys Discovery~
~解析専任者ゼロでも使いこなせるAnsys Discovery~