解析事例
Ansys CFXの収束性や精度の良さで、大幅に流体解析の工数を削減
アイシン・エィ・ダブリュ株式会社様は、1969年の設立以来「品質至上」の経営理念のもとに商品作りに取り組まれ、最新の技術と優れた生産環境により生み出されたオートマチックトランスミッション(A/T)の分野で世界No.1の地位を築かれました。現在ではその優秀性が国内外ともに広く認められ、世界17カ国36社のカーメーカーに納入されています。またカーナビゲーション分野においても大きな成長を遂げられ、業界においてNo.1の生産台数を誇っています。さらに近年では、自然・環境との調和を目指した技術の開発を進め、ハイブリッドシステムや電気自動車をはじめとした車の未来を指向した商品開発にも取り組まれています。
今回のインタビューにご協力下さいましたのは、アイシン・エィ・ダブリュ株式会社 技術本部 第1技術部 T/Cグループの山口健主任研究員、森義英様のお二人で、同社の歴史ある、そして核となるAT事業に携わっており、特にトルクコンバータグループにて、Ansys CFXを利用した流体解析に取り組まれていらっしゃいます。
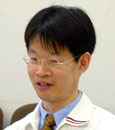
T/Cグループ
山口 健 主任研究員
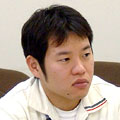
T/Cグループ
森 義英 様
(以後社名はアイシンAW様と表記させていただき、同社のお二人の敬称は略させていただきます。)
まずアイシンAW様の事業紹介と、お二人の実際に関わっておられる研究開発内容についてお聞かせ下さい。
山口
弊社は、乗用車用オートマチックトランスミッション(A/T)、カーナビゲーション、EV(電気自動車)を事業の3本柱としています。我々は、A/Tの開発を担当しており、そのA/Tの中でもトルクコンバータ(T/C)という部品について研究開発を行っております。A/Tには、FF(Front engine Front wheel drive)自動車用とFR(Front engine Rear wheel drive)自動車用に大きく分けられるのですが、T/CはどちらのA/Tにも搭載されます。T/Cは、エンジンからの駆動力を流体(オートフルード)を介してA/T本体側に伝えたり、エンジン振動を吸収する役割を果たす部品なのです。その種類はT/Cの最外径を基準に大きく分けて数十種類あるのですが、取引先に合わせて若干仕様を変えています。そういった細かいところをあわせると今製品化されているのは数百種類くらいありますね。
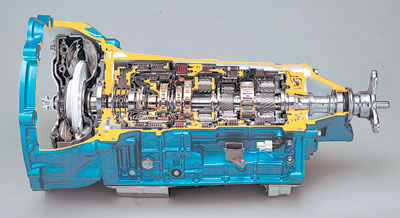
オートマチックトランスミッションのカットモデル
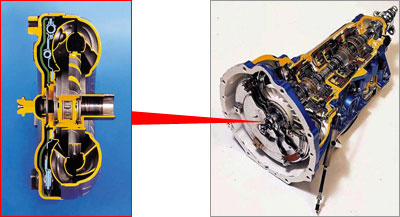
トルクコンバータとオートマチックトランスミッション
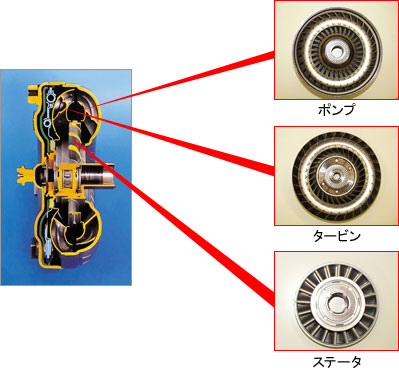
トルクコンバータ 3要素
取引先の会社も様々ですし生産量も多いようですね。国内、国外でどのような取引をされているのでしょうか。
山口
トヨタ自動車様向けのA/Tが大体6割程度、残りが国内の他社メーカー様や海外メーカー様になります。生産量は、03年に400万台を越え現在も増え続けています。現在、全世界のA/Tのシェアは、GMに次いで2位ですが、数年後には世界一になることを目指してがんばっています。
海外との取引というのは、いつぐらいから始められているのですか。
山口
1975年にボルボ社に納入というのが初の海外取引なのではないでしょうか。弊社自体がボルグワーナー(米国)とアイシン精機との合弁会社として始まっていますので、会社創設時から海外に目が向いていたのだと思います。
設計開発は日本で行なっているのですか。
山口
主に日本で行なっていますが、現在は世界中にお客様がいるので、北米やヨーロッパには設計できる人あるいは、実車で評価できる人が何十人も常駐しています。また中国にも生産拠点を計画しており、中国との行き来も盛んですよ。
皆様がいらっしゃる技術本部では、その中にそれぞれの製品を扱うグループが存在するということですね。
山口
はい。A/Tの形式ごとにグループが分かれています。FF車用を担当するグループやFR車用グループ、FFの中にも小さいFFや大きいFFとか、CVTのグループなどいろいろ分かれているのです。1グループ10〜50人ですね。我々のところはトルクコンバータグループでして、15人いるのですが、先ほども述べたように、T/CはすべてのA/Tに取り付けられる部品になりますので、どのグループともやり取りをしながら設計を行なっております。
その中で解析については、どのようなご担当になっているのでしょうか。
山口
社内では様々な解析(コンピューターシミュレーション)が行われていますが、流体解析に限れば、トルクコンバータグループでしか行われていません。他にグループ会社の3名がT/C以外のA/T部品の解析の為に常駐されていますが、まだまだ5人だと寂しいですね。
最初に解析を最初に導入したのはいつ頃ですか。
山口
流体解析の計算ソフトを初めて導入したのは1996年です。その頃は、T/Cの解析ができるCFDソフトというものは、あまりなかったように記憶しております。他社が論文でそのソフトを使っているのを見て、これなら何とか出来るだろうと導入したのがきっかけで、最近までずっと一人でやってきました。2000年にトヨタ自動車様のオーパという車が出たのですが、そのT/Cを初めて流体解析ツールを使って製品化しました。試作品が出来るまでは、かなりドキドキしていましたが、計算通りの性能が出てくれた時は、ホッとした気持ちと喜びでいっぱいでしたね。昨年、この森君も入社して戦力が2倍になった訳ですから、これからは、A/T部品の方にも積極的に流体解析を展開していきたいですね。
では、Ansys CFXの導入に至った経緯をお聞かせいただけますか。
山口
最初に使っていたCFDコードは使い勝手は悪くはなかったのですが、ロバスト性や精度の問題がありました。T/Cの計算は結構特殊な事をしているので、なかなか収束しないとか、時間がかかるなどの問題があったのです。その後、とある学会で海外でのCFX製品の活用事例を聞きまして、試してみようと気になりました。ちょうど今から一年程前になります。Ansys CFXをお借りしてベンチマークをやってみたら結構良かったものですから、それで導入に至りました。それまで、CFXは名前は知っていましたが、見たこともなかったですし、今更新しいツールを使うのはということで躊躇していたことも事実です。
その間他社の製品を検討されたことはなかったのですか。
山口
実際、初めてCFDコードを導入した後は、非常に大変でした。計算が上手くできないのですね。どうやれば計算が動くか四苦八苦していました。また、社内で初めての流体解析ということで、失敗はできないというプレッシャーもありました。そういった経緯もあって実際、設計業務に活用されるようになっても、もっと精度が出る方法があるのでないか、もっと計算時間が短くできないか、ということをいつも考えていたもので、他社のCFDコードを検討するような時間はほとんどなかったわけです。そういったなかCFXに素早く切り替えることができたのは、ソフトの限界を感じていたことと小さな部署なので私が決断したら、すぐそれが反映されるという恵まれた環境にあったと思います。値段が変らなければいいだろう、ということでしたね。ソフトウエアもどんどん新しくなっていますし、ずっと使っているソフトウエアにしがみつかなくても良さそうなのがあれば変えていけばいいじゃないかという考えも今となってはあります。また、実際にベンチマークで使いやすいという感触を持つことができましたから。
グループ会社や関連会社で使用するソフトウエアを統一することもありますが、流体解析ではあまりそのような取り決めはないのでしょうか。
山口
そういう議論はあまりしたことがありません。弊社の場合、自動車メーカーさんとエンジンを含めてパワートレイン系で構造解析のモデルをやり取りするという話は良く聞くのですが、流体解析では他部品との連成で解析するような事は、今のところありませんから、ソフトの統一などは行われていません。解析結果をメーカーさんに提出することはもちろんありますが。
流体解析の場合、その専門性の高さから、最初から最後まで一人の解析技術者が行なうことがほとんどなのでデータをやり取りするということが少ないのでしょうね。それでどちらかと言うと機能最優先でソフトを決定するのですね。
ところでANSYSも昨年から導入いただいていますが、そちらも経緯をお聞かせ頂けますか。
山口
もともとMPCCIを導入して他の構造解析との連成を行なおうと考えていたのですが、CFXとANSYSは開発元が同じなので、一方向だけでなく双方向での解析がやりやすいだろうという判断でANSYSの構造も導入することになりました。T/Cの性能がどれぐらいか、つまりトルクがどれぐらい出るかの計算は、今までの蓄積もあり使えるレベルにまでなったのですが、耐久性の判断ができないでいました。そういった問題に対してもCAEでカバーしたいので、遅ればせながら流体―構造連成を始めたいと思っております。
森
構造の方は私が担当しているのですが、Ansysは比較的画面上で色々指示がでるので操作は覚えやすかったですね。またCFXも覚えやすい印象を持ちました。もともと学生時代はもっぱら流体の実験をやっていまして、流体解析は会社に入って初めて覚えました。
CFXやAnsysの環境や使い勝手についてはいかがですか。トルクコンバータということで大きく形状が変わるというよりは、若干寸法を変更したものの解析を行なうことが多いのですか。
山口
そうですね。T/Cも他のターボ機械と同じで、その若干の変更が流体性能に大きく影響します。特にブレード形状などは。T/C流体性能は、エンジン性能と密に結びついて自動車の動力性能に大きな影響を与えるため、自動車メーカー様からの要求は非常にシビアですね。数パーセント性能が変われば、車の走りがガラリと変わってしまいますから。要求性能を100%満たすものを作るのには、正直、今のシミュレーション技術だけでは、予測不可能なのが現状です。シミュレーションの精度アップにも取組んでいますが、誤差をゼロにすることは、難しいと思います。基本的な形状については、おっしゃるように各モデルとも大きくは変わってないので、逆にメッシュ生成の自動化などは、比較的容易にできました。
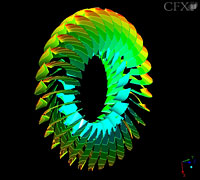
各要素(ポンプ、タービン、ステータ)の
ブレード表面圧力分布
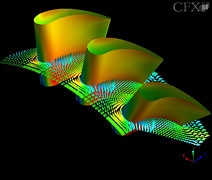
ステータ周りの速度ベクトル
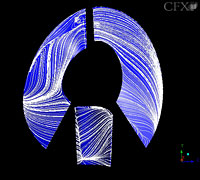
ブレード表面上の流線
長年使っていたソフトウエアから、違うソフトウエアを使うことでの戸惑いなどはありましたか。
山口
戸惑いよりも、かなり楽になったなというのが実感です。先日のAnsys Conferenceでも発表させていただきましたが、CFX上で節点を動かしたり、境界面を直接編集することができないのは残念といえば残念ですが、境界条件の設定方法一つにしても簡単になりましたので、今までの苦労は何だったのか?という感じですね。使い始めてまだ一年程しか経っていませんが、精神的に結構楽になりました。例えば、新規のプロジェクトを立ち上げる場合、一ヶ月の間に計算モデルを数十種類、あるいは、100種類以上作って計算します。これを一人でやるとかなり堪えますよ。今では、自動化プログラムやCFXの活用で、非常に効率的に業務が進んでいます。
現在並列CPUを使っての大型計算を行なわれていると思いますが。
山口
CFDソフト導入時は普通のワークステーションで計算を行なっていましたけれど、その後計算サーバーに移り、CPUの数もどんどん増えていきました。並列計算を行いもちろん大規模モデルを短時間で計算できるようになったことは、事実です。CFXを導入後は、それ以上に解の収束性の良さ、あるいは、設定の容易さ、などがあって、モデル作成から計算評価まで、トータルの時間を考えると今までの半分ぐらいになったように思います。現在行なっている解析が数百万メッシュの解析ですが、もっと大規模な解析も必要になってくると思います。また、バルブやオイルポンプ内の流れなど、T/C以外の部品に対してCFXがどの程度対応できるのか未確認ですが、今後CFXの活用も検討していきたいですね。
機能で収束性や精度で評価頂いていると思うのですが、その他特に評価いただけている機能がありましたらお聞かせ下さい。
山口
SST(Shear Stress Transport Model)乱流モデル、連成AMGソルバー( Coupled Algebraic Multi-Grid Solver)で速度を上げていることなどが挙げられます。実は以前使っていたCFDコードにもSSTが導入されているので、同じ計算モデルで比較してみたのですが、CFXの方が精度も良かったし、計算時間も短かったですね。やはりCFXの売りはそこにあるなと感じました。
デフォルトで2次精度の計算を行なえるようになっているのも大きいですね。
山口
確かにそうですね。他社の製品だと1次精度を行なってから2次精度を行なってくださいと必ず言われますから。また他の機能としてはポストも使いやすいです。ターボ機械用のポスト処理機能が用意されているので、他社のポストにはない機能もありますよね。マニュアルの説明もわかりやすく非常に良くできていると思います。
マニュアルについては今後日本語のチュートリアルを配布しますのでより使いやすいものになります。またGUIの日本語化も進めております。では今後の解析の方向性についてお聞かせいただけますか。
山口
自動車業界を見てみると、流体解析を解析技術者の手を借りずに設計者自らが操作して、設計ツールとして使われている事例が、多く見受けられるようになってきました。こうした流れは、ごく自然のことだと思います。しかし、CFDの活用が遅れている弊社にとっては、流体解析の認知度をとにかく社内で上げることが最重要の課題で、T/C以外の部品へ流体解析の活用し、結果を出すことで、役に立つツールであることをアピールしていかなければいけないと思っています。設計者への展開は、その後でしょうか。
将来設計者向けの解析環境を整える際に、解析結果を正しく評価することの問題が出てくると思いますが、そのあたりはどのようにお考えですか。
山口
マクロ的な評価方法としましては、試験で出てきたトルクの値と計算で出たトルク値を比較して、精度の検証をします。実際、T/C流体性能として求められるのは、トルク値だけなので、それさえ合えば問題ないのでしょうが、現実的に100%一致することはないですから、誤差の原因を突き止めようとすると、実際にT/C内部の流れをミクロ的に見ていく必要が出てきます。現在、ある大学と共同研究という形で内部の流れを調査していますが、なかなか難しいですよ。
実験はかなり難しそうですね。そういう意味でもブラックボックスになっている内部の状態を検証できる流体解析の意義は大きいですね。
山口
そうですね。流体解析ももちろん万能ではないですが、ただ流体解析を使うことで、T/Cのような内部の可視化が難しい部分に対して、その信頼度はともあれ、内部の流れのイメージが付けられるということは、設計をする上で、非常に参考になることですよ。
これからCFXに期待したい機能はありますか。
山口
ハードウェアの進歩で計算時間が短くなってきた今、特にモデル作成に多くの時間が費やされています。A/Tの内部は、非常に複雑な形状ですので計算モデル自体が作れずに、解析を断念したりしていたこともありました。このあたりでのブレイクスルーがあれば、弊社としては、格段に解析が進むでしょうね。究極的にはCAD感覚で、例えば、設計者が画面上で数値を入れたらその欲しい結果を出力してくれるところまで発展して欲しいです。
現時点ではそこまでの自動化には至っていませんが、現在ANSYS Workbench上でDesignModeler(形状作成)⇒Advanced Mesh(メッシャー)⇒ソルバーの統合がなされており、形状変更をそのままソルバーに反映することができるようになっています。ですので、設計者向けのCFDもそう遠い未来の話ではないでしょうね。
最後に今後のサービスについてご要望などあればお聞かせ願えますか。
山口
AnsysとCFXが同じ製品シリーズになりましたが、構造、流体はサイバネットさんとAnsysさんとで分担してサポートをしてもらっていますが、構造-流体連成問題をどちらのサポートに聞けば良いのか戸惑うところもありますので、そのあたりを明確にしてもらいたいなと思います。
ご意見ありがとうございます。製品統合化とお客様サービス体制を合わせて進化させ、より柔軟な対応を早く実現できるよう両社で努力してまいりたいと思います。
アイシン・エィ・ダブリュ株式会社の皆様には、お忙しい中インタビューにご協力いただきまして誠にありがとうございました。この場をお借りして御礼申し上げます。
「CAEのあるものづくり 2005.Vol.2」に掲載
関連記事
関連情報
関連する解析事例
MORE関連する資料ダウンロード
MORE-
Ansys Discovery導入成功の5つのステップ
~シミュレーション主導設計の実現のための秘訣とは?~
-
HPCとGPUで開発サイクル短縮: シミュレーション高速化による流体解析の最新事例
-
熱流体解析ソリューション ~設計段階からの熱課題をシミュレーションで解決する~
~ツールの導入から熱設計、解析業務の効率化まで支援~
-
多拠点で同時進行デザインレビューを実現する
~Ansys Discoveryで設計検証が効率化~
-
リアルタイム解析で変わる商談提案の革新
~Ansys Discoveryで商談中に即座に検証結果を表示~
-
バイオ医薬のスケールアップに貢献する
~Ansys Fluentによる攪拌槽解析~
-
剥離・接合強度評価ソリューション ~Ansys Workbench Mechanicalで実施できる剥離解析~
-
レーザー集光の高温レンズ歪みを克服するAnsys連携ソリューション