解析事例
コンロッドの疲労解析 ~形状および材質の影響~
コンロッドの形状や材質が寿命に及ぼす影響を評価
コンロッドの疲労解析 ~形状および材質の影響~の概要
こんな方におすすめ
- 形状や材質の違いで変化する寿命を定量的に評価したい方
- より高い疲労寿命を持つ製品の検討を行いたい設計者の方
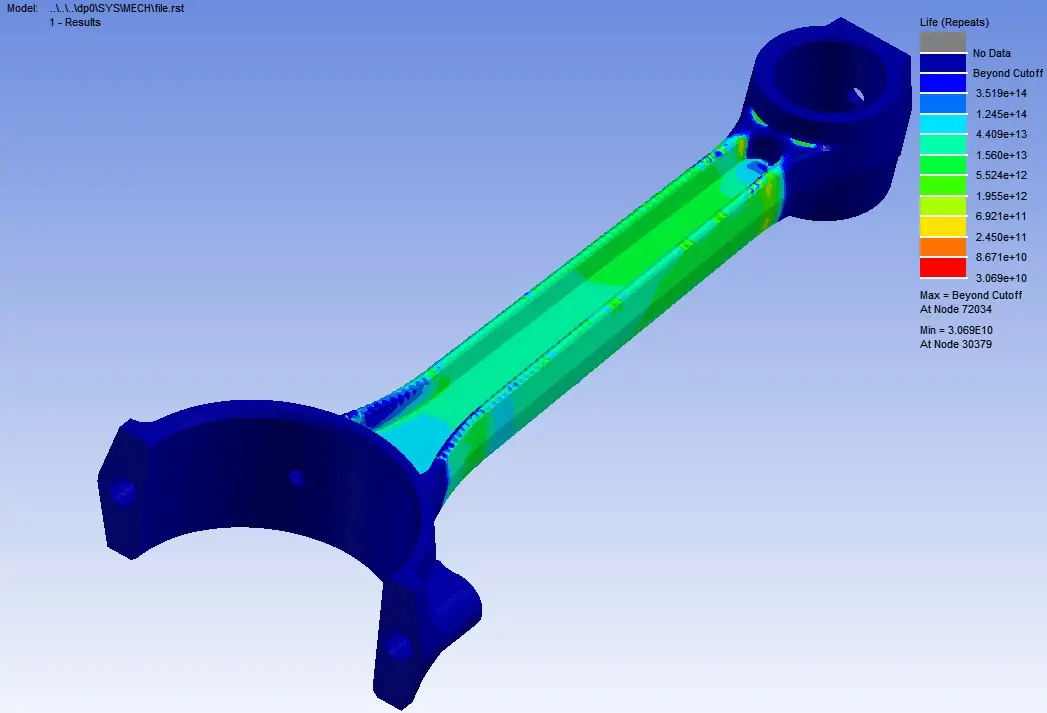
解析概要
疲労寿命を実際の耐久試験で確認するには高額な試験装置や非常に長い実験時間を必要とします。検討する製品の形状や材料が変わった場合にはその都度、耐久試験を繰り返す必要があり、検討の幅を狭めざるを得ません。疲労解析に置き換えて疲労寿命の予測をすることはそれらのコストや時間を削減し、検討の効率化に繋がります。そこで本稿ではAnsys Mechanical(以下Mechanical)とAnsys nCode DesignLife(以下nCode)の連携により、コンロッドの形状や材料を変えた場合の疲労寿命の変化を疲労解析で求めた事例を紹介します。
疲労解析とは
疲労解析とは、対象製品の実際の使用状況を模擬した構造解析の応力・ひずみ結果と材料固有の疲労寿命性能データ(SN線図、EN線図)から、疲労寿命や損傷度を予測する解析です。この解析は通常であれば多額のコスト、時間を要する疲労寿命評価の効率化に役立ちます。
使用ソフトウェア
- Ansys Mechanical 2023 R1
- Ansys nCode DesignLife 2023 R1
背景/課題
コンロッドの設計において、寿命を最大にするような形状と材料を検討したい。
形状や材料を変えた場合にその都度疲労試験を行うことはコスト的に難しい。
疲労解析を実施することで事前予測し、設計検討を効率的に行う。
解析目的および解析手法
解析対象
(図1)のコンロッドに両振り荷重が作用する場合の応力疲労寿命を疲労解析により評価します。形状と材料の変更によりどの程度疲労寿命に影響を及ぼすのかを確認します。
(図1)解析モデル
解析手法
Ansys Mechanicalの静的構造で応力解析を実施、その応力結果に基づいてnCodeで疲労寿命解析を行います。
(図2)解析システムリンク
解析の仕様
解析モデル
下記の3ケースで疲労解析を実施し、疲労寿命の差を評価します。
- 形状:A、材料:構造用鋼
- 形状:B、材料:構造用鋼
- 形状:A、材料:アルミニウム合金
2種類の形状を(図3)に示します。
形状A 形状B
(図3)
材料物性
構造用鋼とアルミニウム合金の物性値を下記に示します。
疲労寿命はSN線図(応力-寿命線図)に基づいて算出されます。
- 構造用鋼(SAE1045相当)
- ヤング率:207 GPa
- ポアソン比:0.3
- アルミニウム合金(A7175相当)
- ヤング率:71 GPa
- ポアソン比:0.33
- SN線図
構造用鋼 アルミニウム合金
解析条件
エンジンのコンロッドを想定し、材料は構造用鋼とアルミ合金が割り当てられ、材料の違いによる疲労寿命の違いを評価されます。
メッシュを(図4)に示します。高次要素を用いており節点数は約9万8千でした。
(図4)メッシュ
静的構造解析の解析条件を(図5)に示します。クランクシャフトに取り付けられる側の受け部を固定し、ピストンから受ける力を想定してコンロッドの長手圧縮方向に軸受荷重を設定します。
また、(図6)にnCodeにおける荷重設定を示します。両振り荷重を想定しています。
(図5)静的構造解析条件
(図6)nCode荷重設定
解析結果
解析結果
MechanicalおよびnCodeによる疲労解析で得られた結果として疲労寿命結果を示します。
- 静的構造解析後の応力分布
- 疲労解析時の疲労寿命
静的構造解析の結果を(図7)に示します。
(図7)Mechanical応力解析 相当応力結果
左:ケース①、中央:ケース②、右:ケース③
nCodeによる疲労解析の結果を(図8)に示します。
(図8)nCode疲労解析寿命結果
左:ケース①、中央:ケース②、右:ケース③
※寿命結果の単位は[サイクル]
解析結果の評価
(図7)では軸受荷重によりコンロッドの各部位に応力が生じていることが分かります。ケース②では穴付き形状としたことによりその穴の縁の部分で応力値が大きくなっています。ケース③はアルミニウム合金材料に変更していますが、形状と荷重値が同じ為に応力値には差が生じません。
(図8) では軸受荷重が繰り返し作用した場合に、何回で疲労破壊に達するかという疲労寿命の結果となります。ケース②は穴付き形状とすることでケース①と比較して応力値が増大した為、疲労寿命が小さくなっています。また、ケース③ではアルミニウム合金材料が構造用鋼よりも疲労寿命が短い為、ケース①と応力値が同じでも疲労寿命が小さくなっています。
本解析の効果
想定される荷重条件下において、コンロッドの形状と材料を変更した場合の疲労寿命の変化を確認することが出来ました。
Ansys Mechanicalで応力解析を行い、その結果からnCodeで疲労解析を実施しましたが、両方のアプリケーションをWorkbench上でリンクさせることで簡単な操作で応力解析から疲労解析までをシームレスにかつ容易に行うことが出来ました。
関連記事
関連キーワード
関連情報
関連する解析事例
MORE関連する資料ダウンロード
MORE-
Ansys Discovery導入成功の5つのステップ
~シミュレーション主導設計の実現のための秘訣とは?~
-
HPCとGPUで開発サイクル短縮: シミュレーション高速化による流体解析の最新事例
-
熱流体解析ソリューション ~設計段階からの熱課題をシミュレーションで解決する~
~ツールの導入から熱設計、解析業務の効率化まで支援~
-
多拠点で同時進行デザインレビューを実現する
~Ansys Discoveryで設計検証が効率化~
-
リアルタイム解析で変わる商談提案の革新
~Ansys Discoveryで商談中に即座に検証結果を表示~
-
バイオ医薬のスケールアップに貢献する
~Ansys Fluentによる攪拌槽解析~
-
剥離・接合強度評価ソリューション ~Ansys Workbench Mechanicalで実施できる剥離解析~
-
レーザー集光の高温レンズ歪みを克服するAnsys連携ソリューション