解析事例
スモールデジタルツインを使った金型温度の均一化
こんな方におすすめ!
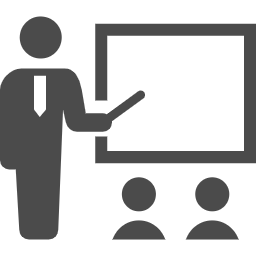
- 生産設備の自動化・知能化にご興味のある方
- 生産技術に関するCAEにご興味のある方
- デジタルツインにご興味のある方
センシングデータを積極的に活用し、製造設備を最適に制御することでマスカスタマイゼーション(少量多品種生産)を目指す取組みが盛んです。一方、センサは適切な位置に配置できない、コストの面で数多く配置できないなどの課題が存在します。例えば鋳造/射出成型等の金型を使った加工方法の品質を上げる為には、温度管理が非常に重要ですが、金型内部にはセンサがつけられず、温度を直接測ることができません。
モデル低次元化(ROM)技術を活用すると3D CAEモデルから実機(設備)とリアルタイムに同期させたバーチャルセンサを実装することができ、アドバンストな情報収集が可能です。 得られたデータ(実測/仮想)で設備の状態を制御することで、安定した品質で生産できる環境を構築することが可能になります。この事例では、リアルセンサでは計測できない金型内部温度のリアルタイム可視化方法や、バーチャルセンサを活用した金型温度の均一化手法などをご紹介します。またCAEを活用して構築したバーチャルセンサをエッジコンピュータに実装する手段など、Ansys Twin Builderを活用することで容易に実現できますので、生産設備の最適制御にご関心がある方にはご参考にしていただける内容になっております。
シミュレーションの背景・目的
誘導加熱による金型加熱システムにおいて、高品質で生産性の高い技術を構築するために、3Dシミュレーションモデルを仮想センサーとして用いるために1DシステムシミュレーションへのROM化(低次元化)を行っている。本検証のポイントは、温度依存性のある電気抵抗と熱伝導率といった非線形が考慮されたROMモデルが構築されて3Dシミュレーションと遜色ない精度で高速に解けている点にある。
3D解析モデルと解析条件
解析モデル
部材の温度依存性(非線形)を考慮するために、過渡伝熱の温度分布を磁場解析に渡し、電気抵抗率を更新しながら発熱量を計算。その時間平均発熱を再度伝熱に渡すフローで表現している。
3D-CAE(磁場-伝熱連成)解析結果
解析結果
- Dynamic ROMでは、連成解析の入出力を学習させてROMモデルを作成できる。
- 今回学習させるデータは以下の2つ。(紫色:電流(入力) 水色:温度(出力))
ROM作成(Dynamic ROM builder)
- プロファイルを読込、ディープラーニングによりROMを生成
- ディープラーニングのため、何を学習させるかが重要。
- Validationの実施し、ROMの精度のチェックを実施。
補足:Validation
- 検証用のデータを作成し、ROMの精度(汎化性)を検証
補足:ROMの再計算
- 計算に時間がかかるため、validation用のデータも含めてDynamicROMを計算すると、精度よくすべての結果が得られた。
システムシミュレーションでの検証
- ROMの動作を簡単なシステムで検証。
- 評価点の温度が室温から500℃に上昇し、キープさせることを目的にする
ROMモデルをエッジ端末上で実行
- Ansys Twin Deployerを用いることで、簡単に制御対象の機器をROMモデルを使って制御することが可能。
関連記事
関連キーワード
関連情報
関連する解析事例
MORE関連する資料ダウンロード
MORE-
Ansys Discovery導入成功の5つのステップ
~シミュレーション主導設計の実現のための秘訣とは?~
-
HPCとGPUで開発サイクル短縮: シミュレーション高速化による流体解析の最新事例
-
熱流体解析ソリューション ~設計段階からの熱課題をシミュレーションで解決する~
~ツールの導入から熱設計、解析業務の効率化まで支援~
-
多拠点で同時進行デザインレビューを実現する
~Ansys Discoveryで設計検証が効率化~
-
リアルタイム解析で変わる商談提案の革新
~Ansys Discoveryで商談中に即座に検証結果を表示~
-
バイオ医薬のスケールアップに貢献する
~Ansys Fluentによる攪拌槽解析~
-
剥離・接合強度評価ソリューション ~Ansys Workbench Mechanicalで実施できる剥離解析~
-
レーザー集光の高温レンズ歪みを克服するAnsys連携ソリューション