解析事例
ヤマハ株式会社 様:シミュレーションと測定データを組み合わせて、ゴルフクラブ製品開発の手戻りを削減
概要
ヤマハ株式会社様は、ピアノやキーボード、ギター、管楽器などの楽器事業や、オーディオ機器やコミュニケーション機器などの音響機器事業、電子デバイスや自動車内装品などの部品・装置事業等の様々な分野に事業展開をされています。
今回お話を伺った長井様は、ゴルフクラブをはじめとするスポーツ用品の設計開発を担当されています。ゴルフクラブの開発において丸紅情報システムズ様が提供される3D測定システムARAMISと、Ansysのシミュレーションを組み合わせて課題解決に取り組まれました。
使用ソフトウエア
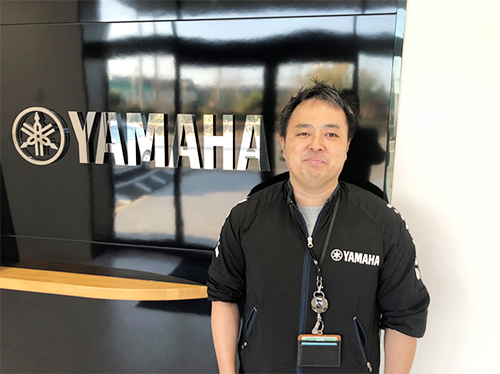
今回お話をお伺いした方
ゴルフHS事業推進部 長井 康晴 様
ゴルフクラブ開発からレッスンの開発まで幅広く対応する「ゴルフHS事業推進部」
長井様が所属される部門とご担当業務についてお聞かせください。
当部門には H:ハードウェア開発と S :ソフトウェア開発があり、ハードウェアは主にゴルフクラブの開発、ソフトウェアはフィッティングやレッスンなどの開発が中心です。開発グループはAT(AdvancedTechnology)チームとNT(New Technology)チームに分かれています。
私が所属するATチームは先進技術を用いて、将来的な性能向上や新しい材料・設計手法の開発、解析手法の改善のための開発をしています。
その中で、私は設計手法や解析手法のサポートに関わっており、ゴルフクラブ(特にゴルフヘッド)の設計を主に担当しています。
ゴルフクラブの開発・製造における課題
製品をリリースするサイクルはどのくらいですか?
開発にあたっては、最新モデルの不満点を改善しながら次のモデルのコンセプトを検討します。リリースしてすぐ不満点がわかれば良いですが、もちろんすぐにはわかりません。時間をかけて徐々に明らかになった不満点を調整しながら開発するため、かなり厳しいスケジュールになります。
タイトなスケジュールで開発されているのですね。ゴルフヘッドの設計では、どのようなことを意識するのでしょうか?
例えば、体積は460ccまで、ヘッドの長さは5インチ×5インチ以内などです。
レギュレーションは年々厳しくなっており、最近では、ゴルフクラブの長さが以前の46.75インチから46インチに制限されたり、慣性モーメント(ヘッドが回転しようとする力)は5900g·cm2以内になったり、反発係数の値なども制限されています。レギュレーションを守った上で、飛距離を出したり、慣性モーメントを極力大きくして球をバラつかないようにしたり、お客さまにもわかるような性能を出す必要があります。
厳しいレギュレーションを守って開発しなければならないとのことですが、開発期間中に設計変更が起こることはありますか?
定期的にATチームが特許定例会で情報を収集していますが、設計段階で特許の問題にぶつかることもあります。特許の出願は主に海外メーカーが多いのですが、海外メーカーが出願した特許が日本でも制約を受けることがあります。
海外メーカーは十分な人材と高度な技術力を持ち、積極的に特許を取得しています。他社の特許への対応は、大きな課題の1つです。
ゴルフクラブ開発で求められるQCDとは?
ものづくりのQCDでいうと、一番大事なものはどれでしょうか?
ゴルフクラブの製造会社は、台湾を中心に全世界で5社程しかありません。世界中のゴルフギアを販売する会社は製造を外部委託しており、5社のどこかで製造しています。
当社もその中の数社を利用しています。材料費は製造委託先が使用する材料の量に応じて決まります。コストダウンの余地があれば検討されます。コストダウン意識はとても高いのですが、製造プロセスに当社は介入できないためコントロールは難しいのです。
開発の人件費の面で、残業を削るとか、どのように効率良く開発するかを検討してコストを下げることはできるかな、とは思います。
コストは大事なもののコントロールが難しいのですね。QとDはいかがですか?
自由度が最も高いのはQです。コントロールできる面で注力しているのはQでしょうか。
レギュレーションの制限の中で飛距離を伸ばすことは大前提で、その上でどのような付加価値をつけて他社と差別化するかが重要です。
自分の狙った位置に飛ばせて、なおかつ打球音が良いとかですね。ヤマハ社内にはデザイン研究所があり、良い打球音を実現するための設計が行われています。
Dについて、制約がある中で考えていらっしゃることはありますか?
リソースが少なく、ドライバー、フェアウェイウッド、ユーティリティ、アイアンなどたくさんの種類の開発、評価までを10人に満たない人数でやらなくてはなりません。
もちろん品質を突き詰める方向にリソースを使いたいのですが、開発スピードの短縮はできるに越したことはないと思います。そのために開発ツールの選定も非常に重要と考えています。
解析と測定を組み合わせて、開発の手戻り削減に貢献
Ansys(解析ツール)とARAMIS(測定ツール)を利用されていますね。導入経緯を教えてください。
試験設備は日本になく、モノで評価することもできません。
開発の手戻りの足かせとなっていた部分を、フロントローディングで解決したいという思いがありました。
Ansysの導入は2012年頃です。
サイバネットさんは、日本国内におけるAnsysの販売・サポート実績が豊富にあり、以前よりお付き合いがあったことから導入を決めました。
最初は振動解析をしていて、そのうち反発係数の解析が重要視され、強度解析も実施するようになりました。
当時の強度解析は不十分で、想定外の破損が生じるなど問題が多発しました。
特にボディ全体の強度を確認する必要があると感じていたのですが、強度を適切に評価する手法が確立されていなく、サイバネットさんに相談
しました。「解析は設定した条件でシミュレーションし、品質向上のための検討を進めることができるものの、実際に発生している現象そのものは把握できません。まずは実験で何が起きているか、どんな挙動が発生しているかを確認してから解析を進めた方が良いのではないでしょうか」とアドバイスをいただきました。
併せて、非接触でひずみが測定できる丸紅情報システムズ様のARAMIS※を紹介いただきました。
導入して試験測定した結果、見たかった現象を確認できるようになりました。
確認できた現象をもとに、さらに解析の精度を上げることができています。
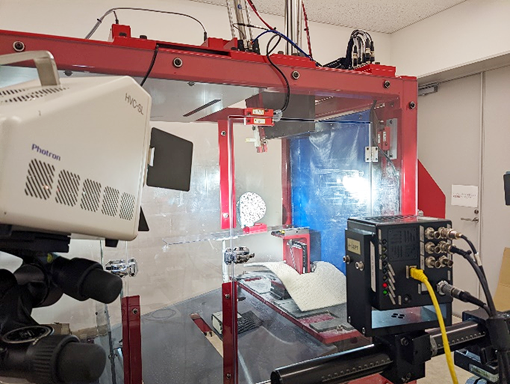
図1 ARAMISを使ったゴルフヘッドの試験測定の様子
新しい製品ごとに、改めて試験測定するのでしょうか?
特に粘弾性材料や高分子材料などの非線形材料では、そのままの物性値が使えない場合があります。
したがって、これらの材料に対する測定と再現が重要です。
測定と再現の経験を積み重ねると、衝突時のゴルフクラブの変形挙動が構造によってどう変わるか、などの理解を深めていけるのかなと思っています。
測定ツールと解析ツールを併用した製品開発にして みて、どのような効果がありましたか。
つまり、開発の手戻り削減に貢献します。
コンター図で赤い部分がダメだと判断でき、明確に不良箇所がわかります。
従来は衝突時の応力で判断しており、ミーゼスか主応力かどちらが適切かなどと議論していましたが、その議論はもう必要ないですね。
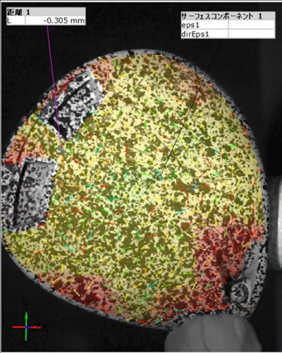
図2 測定結果(Before)
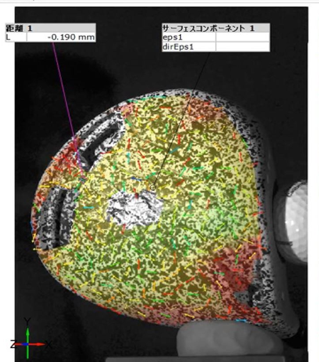
図3 測定結果(After)
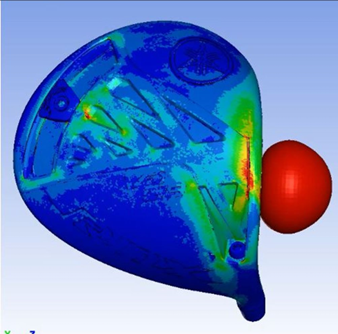
図4 ゴルフヘッド衝突解析結果(Before)
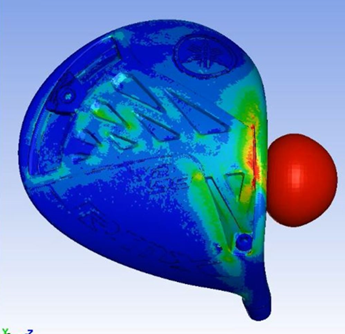
図5 ゴルフヘッド衝突解析結果(After)
試行錯誤して見えてきた新たな開発手順、今後は社内展開へ
新たな開発手順を構築されつつありますね。社内展開や教育はどのように考えていらっしゃいますか?
マニュアルができれば、測定ツールや解析ツールを活用した手順が広く展開され、他のチームメンバーも新たな取り組みを試みることが増えるでしょう。まずは文書マニュアルを制作していますが、いずれ教育用動画コンテンツの制作も検討しています。
また、個人的には疲労解析の手法を身につけているところで、こちらも文書マニュアルを作成し、いずれ他チームのメンバーにも展開していきたいと思います。
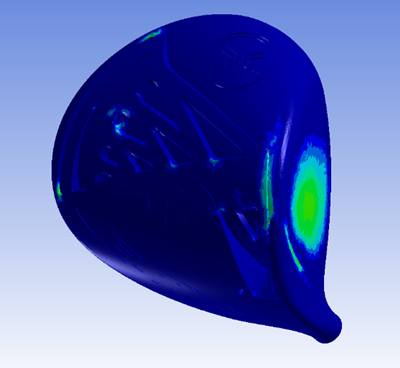
図6 ゴルフヘッドの疲労解析
最後にサイバネットへの要望があればお聞かせください
一方で、新たな取り組みに消極的な人々も一定数います。新しい技術や開発手法などを社内に普及させる方法について、サイバネットさんと一緒に考えていきたいです。
ヤマハ株式会社 長井様には、お忙しいところインタビューにご協力いただき誠にありがとうございました。
Ansysをゴルフクラブの製品開発に活かしているお話を伺うことができました。今後も可能な限りのご支援をさせていただければと思います。
どうぞ宜しくお願いいたします。
注釈
※ 丸紅情報システムズ様ARAMIS:
高精度の3Dモーション及び変形解析システム。リアルタイムでの変形測定や、材料特性の取得およびコンポーネント試験における印加時の挙動と負荷状態を評価可能。数値シミュレーションの妥当性評価にも活用可能。