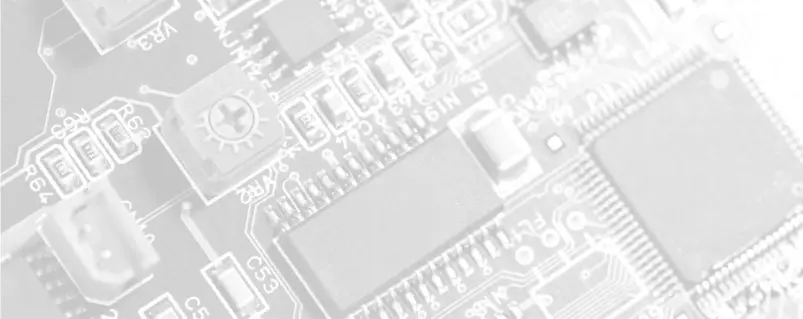
ソリューション
半導体封止材とは? 種類と市場動向、設計ソリューションを紹介
半導体封止材とは? 種類と市場動向、設計ソリューションを紹介の概要
半導体封止材とは?
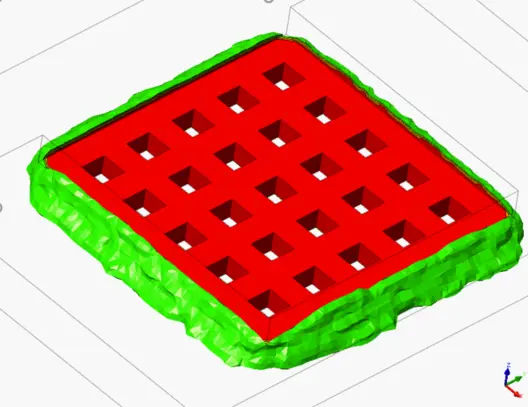
半導体封止材イメージ
半導体封止材は、半導体チップやデバイスを保護し、外部からの振動や衝撃、ほこりや環境変化から守る役割を果たす部材です。半導体チップには微細な加工が施されており、簡単に変形してしまう恐れがあります。例えば、ワイヤーボンディングは金属の細い線のため衝撃に弱く、保護する必要があります。封止工程はモールディングともいわれ、半導体チップを樹脂で固めて保護します。
半導体封止材には、主にエポキシ樹脂、シリコーン樹脂、ウレタン樹脂などが使われます。これらの樹脂は、高い耐熱性、耐湿性、耐衝撃性、電気絶縁性などの特性を備えており、半導体チップをさまざまな環境から保護できます。
半導体封止材によって、チップの信頼性や耐久性が向上し、不具合を防止します。半導体封止材は電子機器の進化において不可欠な要素であり、特性や要求に応じてさまざまな種類が存在します。
半導体封止材の歴史と進化
その後、半導体封止材の外形や材料、加工装置などの標準化が進み、技術は確立していきました。標準化が進んだ結果、生産拠点は台湾などの東南アジアにシフトしていきます。
現在半導体封止材には、高速動作や高密度集積に対応するための熱伝導性や耐久性、小型化への対応が求められています。また、無線や光による通信、MEMSセンサやアクチュエーターなどに対応できる封止材も求められています。
半導体封止の工程と種類
ここでは2種類の封止工程を紹介します。使用する封止材の種類についても解説します。
封止材の工程
現在は金型による樹脂封止(モールド封止)が主流であり、封止手法としてはトランスファー方式とコンプレッション方式があります。
トランスファー方式
多くの半導体はトランスファー方式で製造されています。トランスファー方式では、溶融した樹脂を金型のキャビティに流し込みます。その後、樹脂を硬化させて製品を取り出します。
樹脂の流し込みを行う際に、半導体チップやワイヤーボンディングに圧力がかかり変形する恐れがあります。また、封止硬化後のそりや未充填部に起因する不良が発生する場合もあります。これらの問題を防ぐために、温度や圧力のコントロール、ゲート位置やゲート数、複数個取りのレイアウト配置など、さまざまな条件を設定する必要があります。
コンプレッション方式
コンプレッション方式は、溶融された樹脂をキャビティに入れておき、半導体チップを浸した後に硬化させる方法です。
樹脂の流動が非常に少ないため、チップやワイヤーボンディングへの影響が抑えられます。またゲートやランナーの設置が不要であるため、トランスファー方式と比較して廃棄する樹脂を減らすことも可能です。

モールディング(封止)工程
各種封止材の種類
半導体封止材の種類は、その用途や性能によってさまざまです。一般的に、小型・軽量・薄型の半導体チップには、低密度で低熱膨張率の封止材が使用されます。また、高性能な半導体チップには、高耐熱性や高電気絶縁性などの特性を持つ封止材が使用されます。
樹脂封止材としては、シリコーン系、エポキシ系、ポリウレタン系のものなどが開発されています。それぞれの封止材の適用領域や使用例ついて解説します。
エポキシ系
半導体の封止材としては主にエポキシ樹脂が用いられます。エポキシ樹脂をベースとして、硬化剤や離型剤、難燃剤、着色剤およびシリカが配合されています。エポキシ樹脂は、熱を加えると硬くなる熱硬化性樹脂です。エポキシ樹脂は、電気絶縁性が高く、機械的強度に優れ、寸法安定性も高い特長があります。耐水性、耐薬品性、耐熱性にも優れているため、半導体の封止材として適しています。ただし、紫外線に弱い、硬くてもろい、耐寒性が弱いといった弱点には注意が必要です。
シリコーン系
シリコーン樹脂は耐熱性に優れ、紫外線やオゾンに強い素材です。エポキシ樹脂に比べて光透過率が高く、劣化が遅い特徴を持っています。しかしシリコーンは低分子シロキサンを含有しているため、それが接点障害の原因になる恐れがあります。電気製品の部品で使用するシリコーンは接点障害を起こしづらいよう改良されています。LEDの封止などに用いられます。
ウレタン(ポリウレタン) 系
ウレタン樹脂は、耐水性や耐衝撃性、絶縁性などに優れた素材です。エポキシ樹脂に比べ柔軟であり、高い耐寒性があります。封止材として使用するために、本来弱いとされる耐熱性や難燃性について、強化する材料を混ぜて特性を改良したグレードが使用されます。
半導体封止材の価値と市場動向
半導体を活用してデジタル技術が進化しています。デジタル技術は、ビジネスや生活、人手不足対応のための自動化などさまざまな分野で必要とされています。しかし、ますます増える半導体の一方でエネルギー消費を抑えるための技術開発が必要です。
半導体封止材の市場動向
将来の最先端半導体を製造するためには、半導体チップの高精度化だけでなく、封止の技術も高める必要があります。デバイスごとに封止する形状を変えるなどの多様化が求められていくでしょう。従って半導体封止材も技術開発を進めつつ、大量の需要に対して供給できる体制を整える必要があります。
半導体封止材に関する最新状況と課題
具体的には、複数の半導体チップをまとめて封止することで高集積化を実現します。例えば、スマートフォンのモバイルAP(Application Processor)は、CPUやDRAMなどの半導体チップを製造し、最終的に封止工程で一つのパッケージに統合します。この方法はSiP(System in Package)といわれ、それぞれのチップをチップレットといいます。
課題
このような技術の進化に伴い、新たな課題が浮上しています。以下に、半導体封止技術の進化における課題をいくつか紹介します。
高集積化に伴う熱対策
複数のチップを1つのパッケージに集積することで発熱量が増加します。そのため、効果的な熱対策が重要であり、過熱やサーマルストレスを軽減する方法が必要です。
環境への配慮
電子機器の環境負荷に対する意識が高まる中、封止材やパッケージの素材選定や廃棄物の管理において環境への配慮が必要です。
抵抗上昇、絶縁性低下
高集積化によってチップ内部の信号伝達経路が狭くなるため、信号の遅延や抵抗の上昇、絶縁性の低下といった課題が生じる可能性があります。
データセンター向けの技術開発
性能向上のためにチップの統合が進む中、2.5Dや3D半導体に対応した封止材の開発が求められます。最適なデザイン(設計)を実現することが課題です。具体的には、どのチップをどこに配置するのか、多様化するデザインに対して封止材が対応していく必要があります。
モバイルパッケージへの対応
小型化や薄型化が常に求められ、5G(第5世代移動通信システム)による高速通信の採用が進むモバイルデバイス向けのパッケージは、小型化とともに信号減衰への対応が求められます。よって両面封止や小型パッケージなどの開発が課題となります。
車載用半導体への対応
自動運転技術の進化に伴い、車載用半導体の需要が増加しています。また車載半導体の品質は人命にもかかわるものであり、量産時のコスト管理と合わせて確実な信頼性確保が課題となります。
サイバネットシステムの半導体封止設計ソリューション
サイバネットシステムでは、各工程で懸念される複雑な技術課題についてシミュレーション可能なツールを提供しています。
熱硬化性樹脂による封止解析
PlanetsX は、マルチフィジックス解析ツール「Ansys」の統合操作環境「Ansys Workbench」のアドオンツールです。Ansys Workbenchならではの使いやすい連携解析環境を生かして、射出成形の際の樹脂流動解析だけではなく、そこに線形構造解析を連携させることで成形過程を考慮したプラスチック部品設計が可能になります。また解析を専門としない技術者であっても比較的容易に樹脂流動解析に取り組めることも特色です。
PlanetsXは金型や製品の3Dデータを解析環境に取り込んで利用することが可能です。プラグインやリーダーにより、さまざまな3D CADデータフォーマットに対応しています。データを取り込んだのちのメッシュ生成を支援する機能も備えます。
ソリューション例
以下では、半導体封止における主な解析の事例を紹介します。
温調設定の検討
樹脂のタブレット(粉状封止材)をポット内で溶融するためには、硬化反応率と熱伝導の影響を考慮する必要があります。不適切な条件を設定すると、必要以上の圧力が必要になり未充填などの不良が発生する場合があります。PlanetsXでは、製品や工程の設計時点で、ボット内の樹脂の温度分布や粘土などを伝熱解析でシミュレーションしながら最適な温調設定が検討可能になります。
流動状態の不具合解析
封止材を成形する際に、樹脂の流動性が悪ければ、未充填やボイドが発生しやすくなり、それが製品のショートや割れといった問題の原因となり得ます。Ansys MechanicalとPlanetsXを連携させれば、製造前に封止材料と微細形状の成形性を同時に確認できます。インジェクションやトランスファーといった成形の方式の違いによる影響も比較できます。
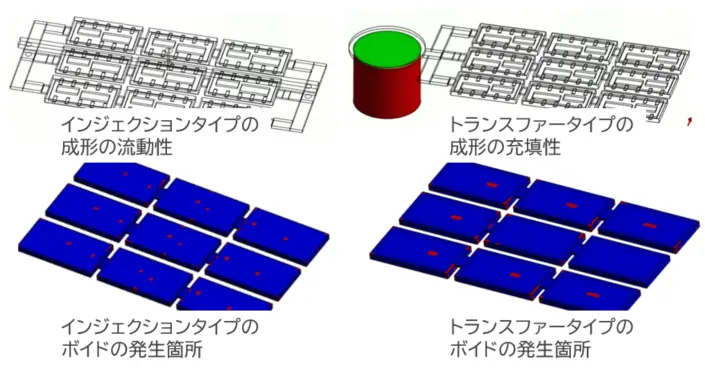
充填圧力による流動評価
硬化状態の不具合解析
射出成形時、未硬化の樹脂を残した状態の部品は、使用時に硬化と収縮が起こり、それが変形や応力発生につながります。また切削など後加工時の不具合の原因にもなります。PlanetsXの熱硬化反応解析によって、充填や冷却プロセスにおける硬化反応を計算し、成形完了後の再加熱と追加硬化(ポストキュア)の検討が可能です。
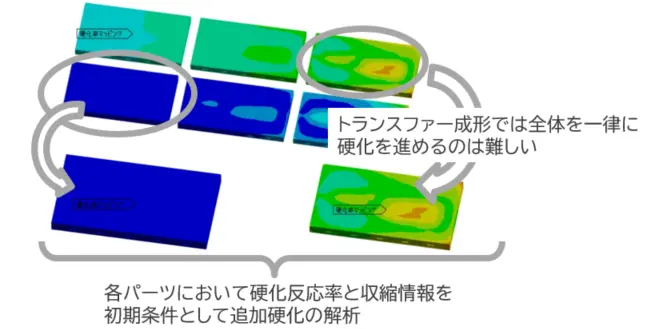
PlanetsXの熱硬化反応解析
素子など内部部品の不具合解析
封止材を成形する工程で、樹脂の粘性が作用して半導体チップの素子やワイヤーに過度な力(粘性抵抗)がかかって変形をきたす不具合が発生する場合があります。PlanetsXは成形時における樹脂の流動抵抗を考慮した内部部品の変形を解析します。成形後の変形を可視化できるので、部品が組み込まれた後の干渉を確認することも可能です。ワイヤーの変形解析においては、非線形の変形も考慮できます。
半導体利用中の不具合解析
半導体部品が完成すると電子基板(PCB)上に実装され、さらにそれが電気製品やセンサ、自動車用部品に組み込まれます。製品の中で半導体部品が機能する際には、発熱によって繰り返し熱荷重がかかり、かつ同じ製品であっても寿命にばらつきがでる場合があります。理由の1つとして、封止内部部品の残留応力のばらつきが考えられます。例えば、多数個取りの半導体の場合、取り出す部品が金型内のどこに配置されているかで残留応力に違いが出ます。そこで成形時の残留応力を考慮した状態で応力解析を行い、さらに材料のS-N線図を物性値として入力しておくと、半導体部品が一体どのくらいの寿命となるのかが予測できます。