導入事例
公差マネジメントによる設計プロセス改革 ~紙図面から3DCAD対応、そして3DAへ~
澁谷工業株式会社
澁谷工業株式会社様は2021年秋に3次元公差解析ツールCETOL 6σを導入。2022年にはさらに追加のライセンスをご導入いただきました。公差設計を急速に進められた背景、公差解析ルール導入後の変化、そして今後の設計現場の展望についてお話をお伺いしました。
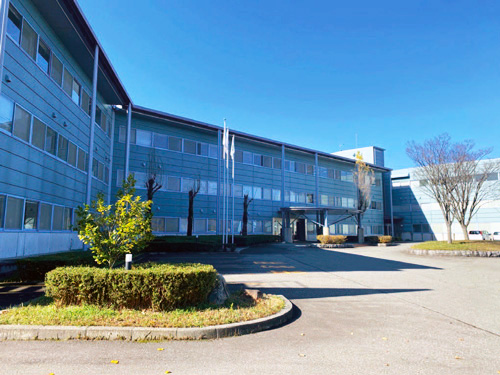
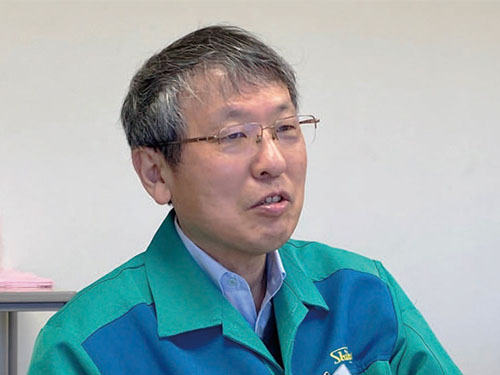
今回お話いただいた方
プラント生産統轄本部 製薬設備技術本部
本部長 執行役員
宮崎 隆 様
澁谷工業株式会社Webサイト
https://www.shibuya.co.jp/index.html
1. 澁谷工業における製品開発
1.1 澁谷工業の沿革
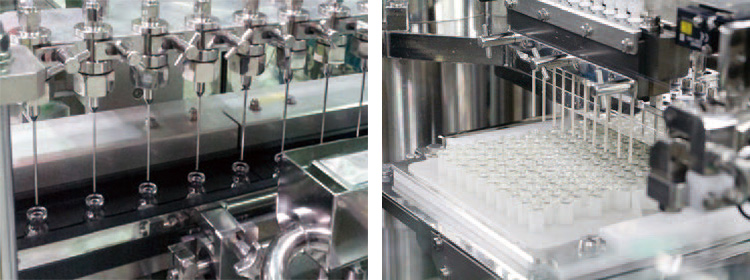
1.2 CAEで効率よく環境に配慮した製品開発を
主力のボトリングシステムについては、ペットボトルの充填機械の設計製造を実施しています。最近は薄くて潰しやすいペットボトルが使われていますが、昔のペットボトルはお湯で滅菌する必要があったため、耐熱性を上げるためには肉厚が必要でした。しかし、無菌の中で充填すれば耐熱性が不要になるので薄くできます。これは無菌であるからこそ実現できる手法であり、薄いので手でぐしゃぐしゃと潰してコンパクトに処分することもできます。そのような環境に配慮した製品の実現にも、弊社の技術が貢献しています。
サステナビリティに関する活動について
弊社はサステナビリティ基本方針をサステナビリティ委員会※1にて策定しており、ここで「環境に配慮した製品・サービスの開発と提供」を目指すことを宣言しています。
弊社のお客様にはSDGsへの課題があり、その目標達成を実現できる設備機械を提供する必要が増しています。世の中におけるSDGsの声も本当に大きくなっていますので、「自分たちはこのままでいいのか」と感じ、このような組織化にもつながっています。御社の提供するソフトウェアを使って効率よくお客様の課題にお応えできる製品を我々の手で作る。それが今の時代はSDGsにも繋がるという構図です。
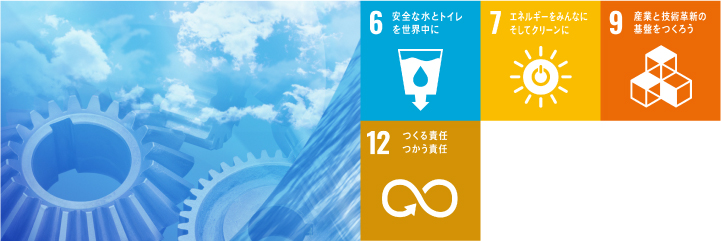
2. 公差解析ツール初期導入と追加導入の経緯
2.1 3次元CADをもっと活用するために
CETOL導入の背景とは
元々、SOLIDWORKSを持っていたこともあり、SOLIDWORKSとCETOLを連携させて使っています。ツールに よって得意不得意がありますが、弊社の仕事にはCETOLの得意な部分が充分マッチするということがわかって います。一方でCETOLが不得意なところに関しては、SOLIDWORKSやAnsys SpaceClaimなどを活用した方がよい作業ができる場合もあります。適材適所でツールを使い分けている状況です。
CETOL導入の際、他のツールと比較しましたか
導入の時の決め手とは
2.2 次世代対応のための先行投資
2022年に追加ライセンスを導入された背景とは
今はCETOLを製薬システムの設計で、徐々に使い始めていますが、そのうちボトリングシステムの設計現場でも必要になると考えています。ボトリングシステムは機械がとても大きくて同じ部品がたくさんあります。部品の数が多ければ多いほど、微調整などを排除して組み立ての効率を上げることが重要になりますので、本来は製薬システムよりもボトリングシステムの方が部品設計において公差の恩恵を受けられるはずです。近い将来、公差は避けては通れないと思っています。
3. 公差解析ツール導入後の変化
3.1 累積公差※2を把握し、調整箇所を明確化
公差解析ツールの導入後の変化とは
“調整すべき箇所を公差解析ツールで明確化しよう” という意識に変わったと感じています。現在組み立て中のユニットも、従来の設計であればさまざまなところで調整が必要になっていたと思います。今回 CETOL を使用した装置では、部品公差だけでは目標は達成できないというのが、まず明確に数字として見えてきました。つまり、「こんな公差で作れるはずがないだろうというくらいいじめないと無理だ」というのがよくわかったということです。従来の方法ではあちこち調整が必要な設計になっていたものを、「ここだけ調整すればいい」というように、調整箇所が明確な設計をツールによって実現できました。
従来であれば、「これぐらいの誤差だろう」と勘で設計して、実際に組み上げたらaとbのユニットが全然合わず、「ここにもシム※3入れなきゃいけない」「この辺を削らなきゃいけない」という状況に陥っていたと思います。今回はそうではありませんでした。積み上げていく中で公差による誤差が累積していきますが、「一番先端のここだけをその吸収用に調整できるようにしておこう」、それ以外は「誤差で縛れ」というように、調整箇所を局所的にできました。同時に、作れない誤差ではなくて、現実的な誤差で縛ることができました。
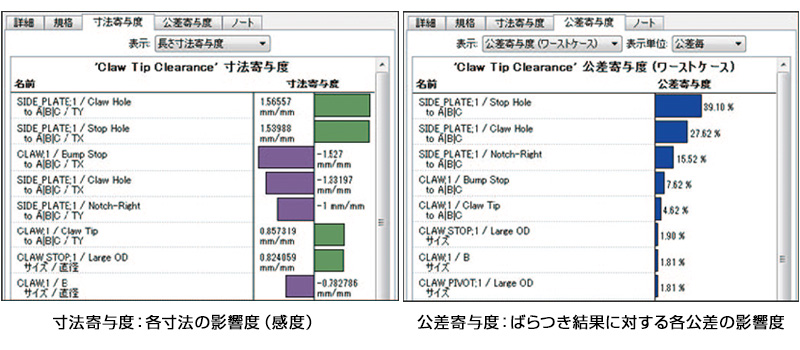
よく使われるCETOLの機能とは
「寄与度※4」ですね。寄与度のグラフなり数字なりが次々と出てくるのは、設計者にとってとても新鮮なようです。「ここがダメなんだ」「こうしよう」「ああしよう」と、その場ですぐに決められるので、そういった機能は強いですね。
3.2 全体プロセス、設計期間に対するツールの影響
設計期間は短縮できたのでしょうか
全体プロセスのうちCETOLを適用した設計期間は2か月程度ですが、これを含むシステム全体が完成するまでの期間としては1年半~長ければ試作機からなので2年くらいの期間がかかります。公差解析の実施により設計検討の期間が多少伸びたとしても、組み立ての期間が圧縮される方が我々としてはメリットが大きいと思っています。
公差を実施する上お役に立てたサービスとは
3.3 公差設計を進める起爆剤に
先日もかなり複雑な機械部品の公差設計にトライされていましたよね
あのようなアプローチになってしまったのも、公差設計にまだ慣れていないからだと思います。もう少し「公差設計とは何か」を理解できていれば、最初からモデルをもっとシンプルにして、そこからアプローチできると思います。そういう点で、我々はまだまだこれからですね。とはいえ、手書きではとても無理ですし、勘で公差を入れても全然話にならないので、CETOLがこれから公差設計を進めていくためのよい起爆剤になってくれることを期待しています。
4. 澁谷工業における公差解析事例
4.1 公差により部材の分割方法を変更
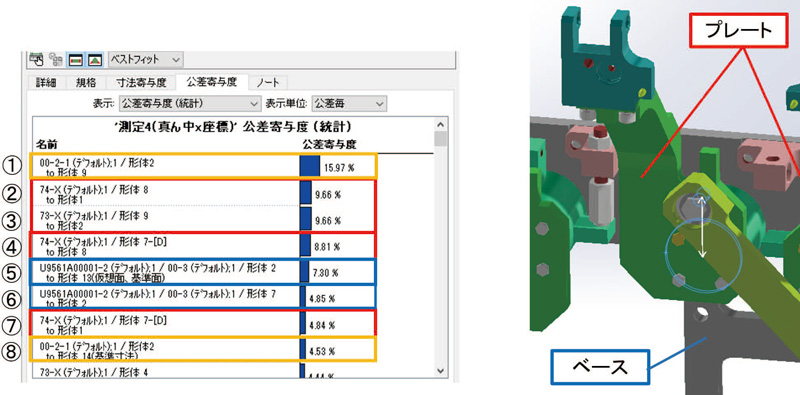
最初、この部品の作り方は違う加工方法でしたが、公差を見て部材の分割の仕方を変更しました。例えば、ボス※5に対してアームが出っ張っていますが、これはアームをボスに溶接する構成になります。これでは傾きなどの位置合わせが面倒です。そこで、出っ張り(削り出し)を作った部材にボスを溶接すると、基本的にはすべての位置関係が最初に決まるので、最後仕上がった時にさらっと削れば、それで位置がすべて決まります。公差の配分が見えるので、設計変更を判断しやすいです。
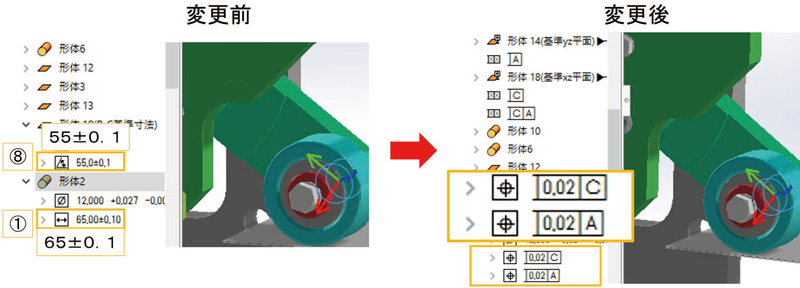
この変化はツールの効果になるのか、それともツールがなくても気づけたのでしょうか
ツールはこれでも大丈夫という検証、根拠づけに役立っています。特に、弊社の製品は部品の数が多いので、百個の部品に対して百回解析をするのはとても大変ですよね。そうなると根本的な設計方法から変える必要が出てきます。
このようなプロセス検討はどなたがされていますか
4.2 量産品だけじゃない公差の効果
公差が必要になるのは量産品なのではという印象があるようですが
5. DRでの迅速な意思決定をツールで実現
5.1 澁谷工業流“miniDR”とは
弊社の機械は複数の人間で設計することが多いので、このユニットの議論をしている最中に「あっちのユニットはどうだろう」とか。このユニットに関連することだから一緒に考えなきゃいけない場合は、声かけて一緒に話すとか。そんな感じで気軽にDRを実施しています。
このようなminiDRを実施する土壌が以前からあったので、そこにうまくCETOLのスピード感がはまったのかもしれません。3次元CADを使い始めてからはスピーディーなDRを重視しています。
5.2 DRにおけるツール活用の現状
画面を見ながら「ここをもっと詰められないか」「ここは攻めすぎだからこっちはもう少し甘くして、こっちに振ったらどうか」といったコメントが出たら、持ち帰らずにその場で設定変更してすぐにパパっと答えが出てくるので、それはありがたいと感じています。
6. 公差教育の課題とは
他社では教育の課題が多いようですが御社では
教育らしい教育といえば、新入社員の時に公差設計の入口を教える程度です。実際に「一次元レベルの手計算で積み上げて計算したらこうなる」という初歩的な内容を練習させています。
これだけでは不十分なので、その先を変えていくのも、CETOLに期待しているところでもあります。
CETOLの操作に慣れている設計者が2名いますが、その2人はCETOLの操作を実施しているのみです。DR でシミュレーションが必要と言われた場合は、また別の担当者も関与することになるので、そのような仲間が波及効果で公差のことを意識してくれるといいなと感じています。「こういうツールでやれば、自分の悩みは簡単に解決できるんだ」というように。そのプロセスの中で、操作しながら経験を積むことで公差設計とは何かをしっかりと理解してもらえるようになると思います。
7. 未来の設計者CAE実現に向けて
7.1 現状の一番の課題とは
それに対して、御社の製品を使うことで昔だったら手計算で何年もかかった計算が簡単にできるようになってきていますよね。Ansys Discoveryなどをはじめとした“設計者CAE”を、もっと普及させなきゃいけないと感じて、弊社でも今いろいろと動いています。
7.2 未来へ向けたノウハウの蓄積
ノウハウの蓄積に向けて実施されている取り組みとは
最初はAccessで行っていましたが、それをもう少しプログラムに長けた人に預けてWebから確認できるようにしました。Webからはイメージデータを検索することができなかったので、中間ファイルを立ててキーワードなどを埋め込んで、それをWeb上から検索して、イメージが見えるような仕組みを作りました。そういうシステムを下地にすれば、ノウハウの蓄積というのは、そんな難しいことではないかもしれません。
7.3 弊社へのご要望
弊社に今後期待することやご要望について
次にお願いしたいこととしては事例の提供です。「こんな事例が世の中にあるんだ!」と驚くような。その事例の中から我々が何を感じるかが大事だと思いますが、情報は探し出すしかないので、常に我々の業務に適したものを探しています。御社の得意なソフトウェアの分野でやったらこういう答えだったけど、いやいや世の中こんな手法もあるよねというケースもあるでしょうし。リアルなもの=事例だと思います。
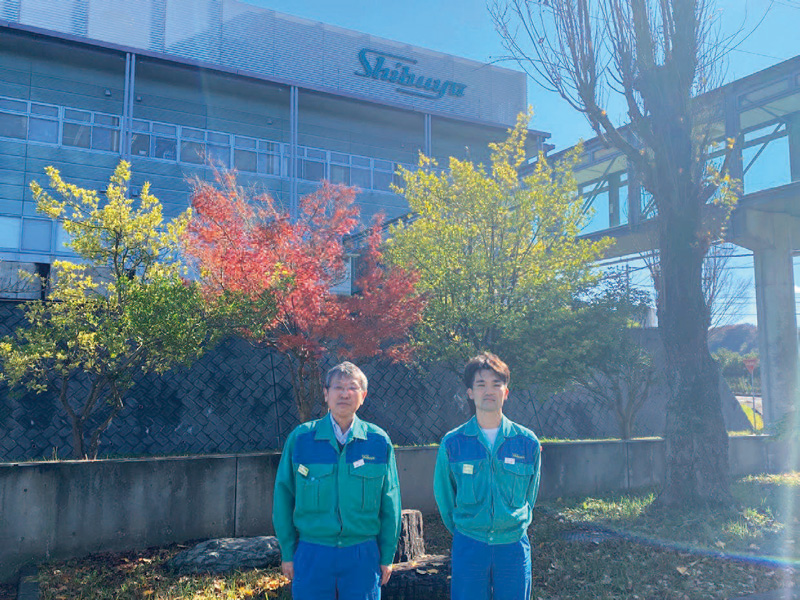
この度は公差解析に関する貴重なお話をお伺いさせていただき、誠にありがとうございました。弊社も驚きを与えられるような新たな解析事例や、最新の情報をお届けできるよう努めてまいります。
注釈
※1 サステナビリティ委員会:シブヤグループにおけるサステナビリティ基本方針を定め、持続可能な社会に貢献する取り組みをされている委員会。
(参照:https://www.shibuya.co.jp/outline/sustainability.html)
※2 累積公差:評価、解析箇所に関連する公差を積み上げた値
※3 シム:部品の位置や傾きを調整する際に使用する詰め物
※4 寄与度:解析箇所に対する影響度の大きさを示す指標。設計見直しなどの際に修正が必要な寸法(形状)や公差を把握できる
※5 ボス:部品の組み合わせや、部品同士を締結する際に使用される結合部分
※本事例のPDF版は下記よりダウンロード可能です。