解析事例
株式会社本田技術研究所様:乗用車用廃熱回収技術のトップランナーを目指すホンダ!
~ シミュレーション技術を活用したランキンサイクルシステムの研究。実用化へのチャレンジ~
概要
今回のインタビューでは、株式会社本田技術研究所様(以下、本田技術研究所)にご協力いただきました。CO2削減は自動車メーカーにとって大きなテーマです。本田技術研究所では、2020年までに二輪車・四輪車・汎用製品のCO2排出量原単位を2000年比で30%低減すること目標とし、さらに“ Triple Zero” ※1 を目指してその後もCO2排出量低減の取り組みを進めています。昨今自動車の電動化が進んでいますが、EV(電気自動車)が普及するには課題も大きく時間がかかります。CO2排出量低減のために電動PU(電動パワーユニット)のみならず内燃機関や車両の技術も含めトータルでCO2削減の研究を進めていく必要があります。そのひとつのアプローチとして廃熱回収※2 技術の研究があります。
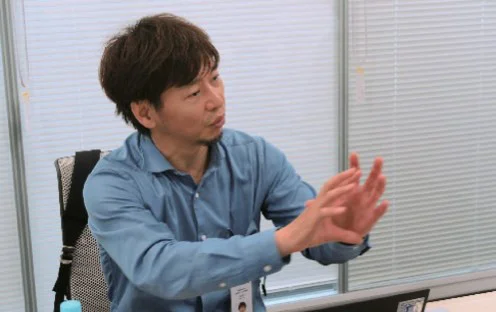
今回お話をお伺いした方
株式会社本田技術研究所 先進技術研究所
主任研究員 土佐 真一 様
1.乗用車に廃熱回収を搭載する研究への挑戦
このプロジェクトの目的を教えてください。
土佐
廃熱回収がCO2削減に有効な技術であることは言うまでもありません。例えば発電所のコンバインドサイクルや温泉発電などに利用されているバイナリ発電、船舶やF1でターボジェネレータが使われています。さらに近年では大型車にも使われ始めています。一方、乗用車については2000年代後半あたりから本田技術研究所も含め様々な企業・研究機関で廃熱回収が研究されています。しかしいまだに適用された事例はありません(注:オフサイクルクレジット獲得目的の適用事例を除く)。その理由として、回収効果と搭載性課題のバランスを見極めることが容易ではなく、適用価値を判断できないことが最大の問題だと考えています。乗用車は過渡運転のため最適仕様や最適制御を設定するのが容易ではありません。加えて、車としての基本性能を維持するために既存のシステムや部品への影響も明確にする必要があります。単に発電するための部品を追加するというだけでは済まされません。
10年以上この研究をされてきた方々からお話を伺ってみると、システム改良を積み重ねてようやく出力目標は達成できるようになったものの、それが定常運転であることや搭載性課題も挙げられた結果、適用判断には至らなかったそうです。このように、回収効果を明確にすることも、課題を明確にすることも容易ではないのが乗用車用廃熱回収研究だと思います。私たちのプロジェクトではこの問題に挑み、本格的に部品やシステム研究を始める前の基礎研究段階において、価値と課題のバランスを見極めようと思っています。
2.シミュレーション導入による検討期間の短縮
どのような理由で、研究プロセスにシミュレーションを導入されたのでしょうか。
土佐
1つの理由は、先に述べた問題に対する検討期間の大幅短縮です。シミュレーションの活用なくして短期間で答えを出すことは不可能です。従来のように試作と実験を繰り返し、徐々に回収効果を高めていく手法だと最適システム設定に至るまでに相当な年数がかかってしまいます。私たちのプロジェクトでは、テストはするもののできるだけ最小限にとどめ、得られたデータを解析し、デジタルツールを駆使してバーチャル最適仕様を構築して早期にゴールが見えるようにしたいと考えています。別の理由として、論理的アプローチができるようになると考えています。
CAEのモデルを作成するには、システム、部品、現象に対する理論的理解が必要ですし、データサイエンスで解析するには説明変数は何か?データは足りているか?など、自ずと論理的に思考するようになります。そして、バーチャルの最適仕様と現状との差分も明確となり、バーチャルで最適化したものを現実にするためには何を開発すべきか?といったアプローチを描きやすくなります。
このように、ゴールを早期に見つけ、そこに至るまでのアプローチを描くことが狙いです(図1)。
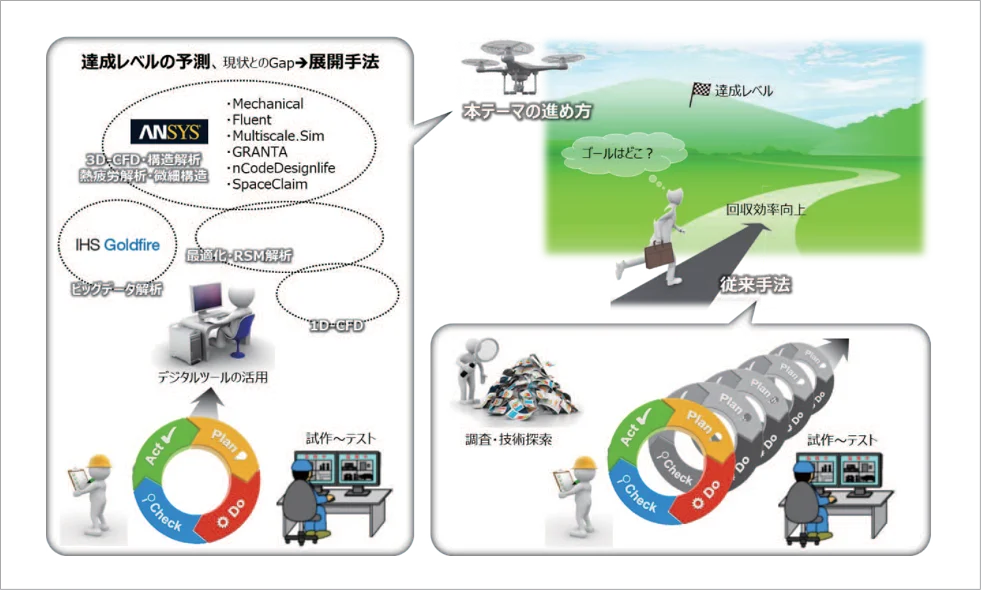
図1 アプローチ方法の概念
3.Goldfireを活用して膨大な特許検索作業の大幅な効率化を実現
土佐様から見たGoldfireの活用メリットを教えてください。
土佐
膨大な情報から欲しい情報を精度よく探れることです。この研究テーマを立ち上げた当初から廃熱回収技術に関する情報はある程度持っていました。当プロジェクトではいくつかある廃熱回収の技術の中からランキンサイクル※4 を取り入れることを決めましたが、最初からランキンサイクルにフォーカスしていたわけではありません。いろいろな廃熱回収技術の中から、乗用車に適用できる可能性がある技術を選定していきました。第一段階のスクリーニングで3つの技術に絞ることができました。
当初は検索で得られた約2万件の文献を母集団として他社の俯瞰解析ツールでマッピングしてみましたがうまくいきませんでした。キーワード検索ではノイズが多かったことが原因です。ちょうどその頃に利用を始めたGoldfireで抽出した結果を俯瞰解析ツールに取り込んでマッピングしたところ、マップ上に種々な廃熱回収技術が分散して現れ、データ解析に適した俯瞰図を得ることができました。そこからデータ解析を進め、例えばある外燃機関システムは乗用車への搭載が容易ではなく乗用車向け研究としては収束している状況が読み取れ、またあるエネルギー交換技術についてはまだアカデミックな研究段階で実用化には遠いといった状況がわかりました。このように、技術ごとの特許件数の推移などから着目すべき技術を選定していきました(図2)。
Goldfireと俯瞰解析ツールを使った分析によって技術内容の詳細な知見がなくても、技術動向がわかることで廃熱回収技術のスクリーニングができ、初期の意思決定には十分利用できます。このような有効な分析ができたのはGoldfireのセマンティック検索※5 機能が精度よく先行技術を抽出することに適していたからだと思います。
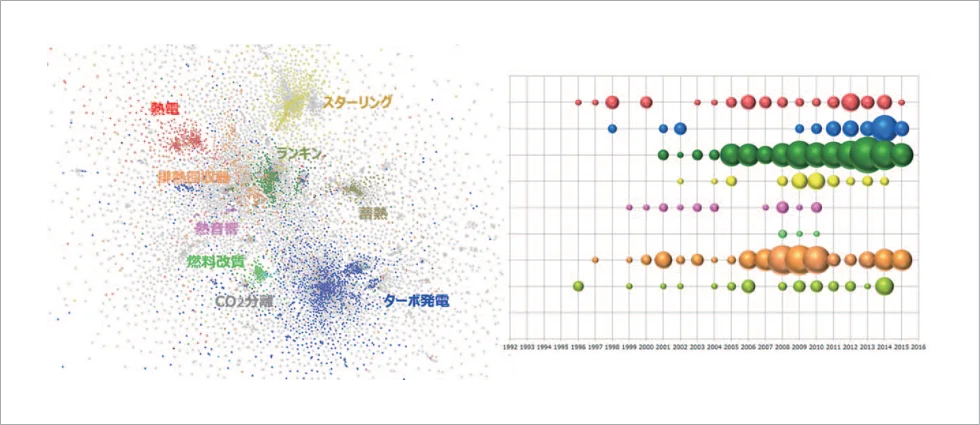
図2 ビッグデータ分析ツールを使用した技術動向の調査
Goldfireは初期のスクリーニング以外でも活用されたのでしょうか。
土佐
はい。例えば廃熱回収技術候補をランキンサイクルに絞り込んだ後の特許検索に使いました(図3)。最初に情報収集するときに検索精度を高めておき、ノイズが少ない母集団でマッピングしたほうが成功することが先の試行錯誤からわかっていたからです。ただし、適切なクエリーで検索する必要があったためサイバネットシステムにサポートしていただき、クエリー作成のコツを教えていただきました。得られた俯瞰図を分析した結果、プレーヤーが限られていることに気づき、キープレーヤーだけの特許を抜き出して調査することで従来技術がどの範囲にあるのかを理解できました。また、キープレーヤーが絞り込めたので、直接会って話すことで貴重な情報を得ることもできました。
それ以外にも反復クエリ機能で最新関連情報のパトロールや発明段階での技術調査でもGoldfireを活用しています。特許出願に向けて発明届を作成している段階で、Goldfireを使い従来技術を調べて、発明アイデアとどこが差分なのかを確認しています。これにより知財部門とのやりとりもスムーズになって手戻りも少なくなり、効率よく特許出願ができるようになってきています。図3は特許オーバーヘッド分析例です。
最後にGoldfireの利用用途をまとめますと、研究初期段階における技術動向調査、特定の技術の動向やプレーヤー・既存技術範囲の把握、発明段階での技術調査の3つが主な目的となっています。
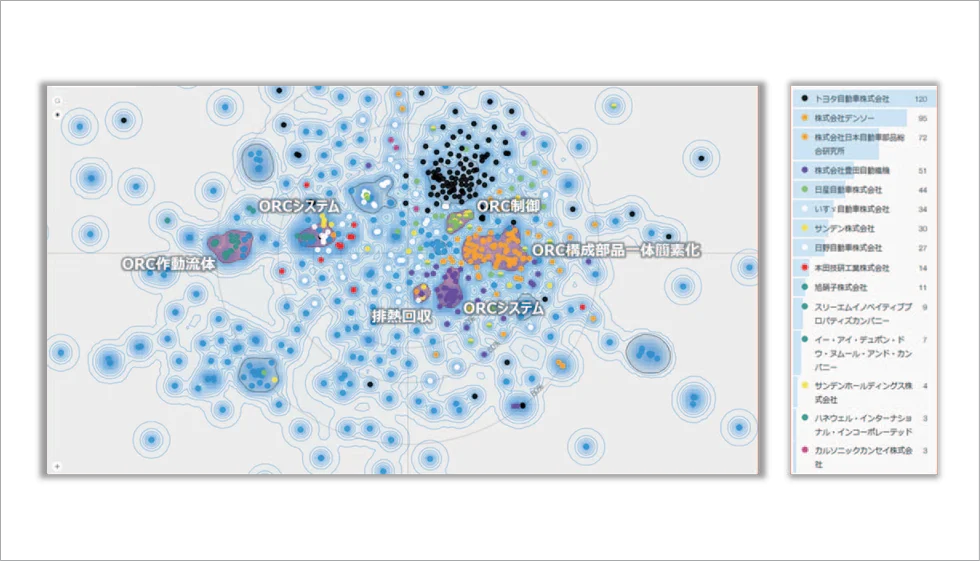
図3 特許オーバーヘッド分析例
4.1Dシミュレーションを活用することで現実的には不可能な検討を可能にした
1Dシミュレーションの活用目的を教えてください。
土佐
研究初期では、Goldfireを使った技術動向調査でスクリーニングした候補技術を最終的に一つに絞り込むにあたり、1Dシミュレーションを活用して机上で比較検討しました。廃熱回収はターボジェネレータ、熱電、ランキンサイクルなど技術毎に技術内容が全く異なります。これらの研究は別々にされてきており、同じ条件で比較されたことはないと思います。別々の技術をテストで比較するのは非現実的なため、1Dシミュレーションで行うことにしました。また1Dであれば、モード走行のような実用的な条件で比較検討することが可能になります。1Dモデルのデータを私たちのプロジェクトで全て作成することはできないため、先行して研究されていた方からモデルの一部やデータを頂き、ある部分は外部に委託するなどして作成しました。こうして得た3つの技術の簡易的1Dモデルを同一モード条件で比較した結果、ランキンサイクルが最も回収効果が期待できると判断しました。このように、データがない、モデルが自作できない状況でも、関係者・協力者から提供されたモデルをカスタマイズして利用するなどにより研究が進められることも1D活用のメリットであることを実感しました。
次のステップでは、ランキンサイクルシステムを試作してテストを行い、そのデータを基に1Dモデルを作成します。そのモデルを使って車両内の関連する他のシステムモデルと連成し、モード走行にて車両として得られる効果またはデメリットを試算します。図4は簡易1Dモデルの計算結果の例です。さらに、モデル上で改良を進めてバーチャルに最適仕様を構築することも可能と考えています。これを進める過程で、機械学習や最適化計算ツールも組み合わせて活用します。図5は1D-CFDを使用した効果予測フローの例になります。
この一連の検討内容を1Dなしで試作とテストで進めようとすると膨大な費用と工数がかかり、現実的ではありません。少し誇張して言えば、現実的には不可能な検討を可能にできる、これが本研究における1D活用の目的と言えると思います。
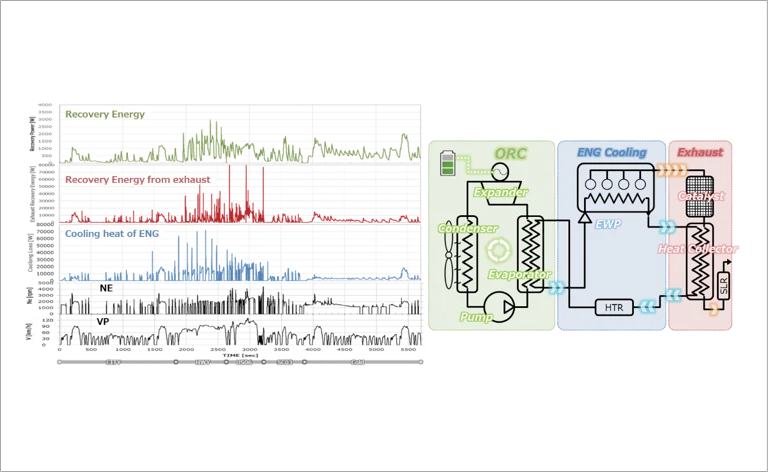
図4 簡易1Dモデルの計算結果例
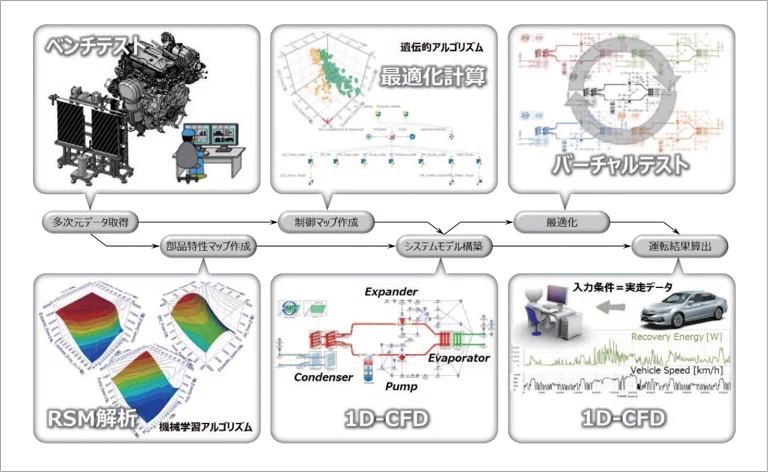
図5 1D-CFDを使用した効果予測フロー
1Dシミュレーションを利用するにあたって注意すべき点を教えてください。
土佐
私たちのプロジェクトでは、CAE専任担当を決めていません。わからないことなどは講習やサポートで対応し、難易度が高いことは外部業者のコンサルティングを受け、スキルが必要な作業などはサイバネットシステムをはじめとする外部専門技術者に一部業務委託することもあります。しかし基本的には研究担当者自身がCAEを行うことにしています。特に1Dやビッグデータ解析は共通ツールと位置付けておりメンバー全員がユーザーです。私自身も数年前までは全くのCAE初心者でした。CAEノンエキスパートの研究者自身が解析作業するには苦労は伴いますが、先にも述べたように、モデル作成やカスタマイズ作業そのものが研究の一環であり、部品特性・システム特性・現象・メカニズムに関する理解が深まります。その後の改良や最適化に向けてどこをどう変えたらよいのか?の気づきとなります。作業効率を優先するあまり、モデル作成作業全てを外部に委託してしまうと、貴重な知見を得る機会を逃していることになりかねません。
1Dシミュレーションをうまく使いこなすコツはあるのでしょうか?
土佐
はじめから完璧なものを作ろうとせず、ある程度の寛容さを持つことも必要だと思っています。CAE結果をPRすると即座に 「それ合ってるの?」「検証した?」と質問されることがあります。もちろん検証することは必要不可欠だと思いますが、重要なのはタイミングとやり方です。検証すなわち答え合わせが目的になってしまって、そのためのテストに時間と工数がかかったりしては本末転倒です。場合によっては検証を後回しにする、精度は悪くても割り切る、など状況によって臨機応変に活用し、研究を前進させることが一番大事でそのためのツールだと思っています。
実験結果との合わせ込みで割り切りをした一例を紹介します。廃熱回収シミュレーションのために1D排気モデルを構築し、その中で触媒モデルを作成しました(図6)。触媒による反応熱も熱量としては無視できないと考えたからです。三元触媒反応には9つの反応式を用い、その一つ一つのアレニウス式の頻度因子(A)と活性化エネルギーの値(Ea)を変数として、浄化率が実験値と合うように合わせ込みを行いました。合わせ込みは、排気モデルから三元触媒反応部分を切り出した1Dモデルと最適化ツールを連成させ、遺伝的アルゴリズムを用いて計2000回の計算を行いました。計算時間は一週間でした。結果、浄化特性計算値は初期設定に比べて実験値に近づいたものの、過渡特性は十分には合いませんでした。
EM目的のシミュレーションなら許容できないレベルですが、私たちの目的は廃熱回収であり、過渡の浄化特性がズレていても活性開始温度と最高浄化率がほぼ合っていれば、モード走行での排ガス総熱量としては誤差が僅かであることから、このモデルを使用しています。もしここで合わせ込みにこだわったなら、素反応の詳細な実験データを取得して最適化をやり直す、場合によっては阻害項や吸着項も見直さなくてはならず、少なくとも数か月は必要になったと予想されます。
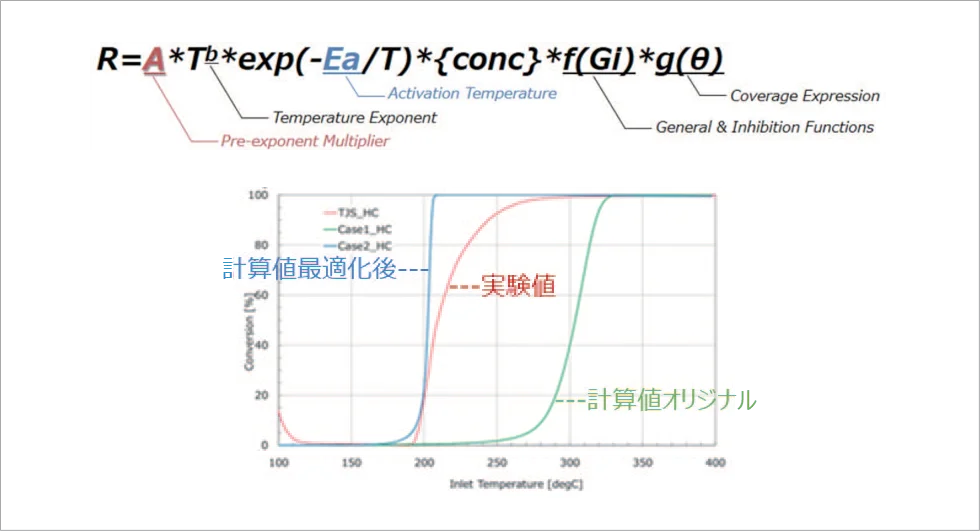
図6 触媒反応モデルの組み込み
1Dシミュレーションを活用するためには、寛容さを持って方向決定のために用いることが重要なのですね。では、3Dシミュレーションの活用目的を教えてください。
土佐
実用化に向けた一番の課題は搭載性であり、それに対応するには部品の小型化は必須です。ランキンサイクルには4つの主要機能部品があり、それらを小型軽量化する上で新しい構造を検討する必要があります。1Dシミュレーションでは部品の構造などを細かく検討できないため、3Dシミュレーションを活用します。小型化アイデアをモデルに適用し、試験データとのコリレーションも並行で行いながら進めていくことになりますが、今はその準備段階といった状況です。
3Dシミュレーションを実施することによってどのようなメリットがありましたか?
土佐
一つは実験で計測が容易ではないパラメータを得られることです。例えば熱流体の流れ分布や温度分布、微細構造の熱疲労などを見える化・定量化することでコンセプトに沿っているか、問題点、弱点部位に気づくことができました。
もう一つはバーチャルに構造変更を検討できることです。簡単に試作することができない構造の検討や最適構造の追求が可能となります。
私たちの研究テーマでは排気系部品や熱交換器などを検討するため、高温の熱流体や微細構造を取り扱うことから3Dシミュレーションなくしてそれらの詳細な情報は得られません(図7)。
なお、活用するツールもCFD・構造解析・マルチスケール・熱疲労解析・最適化と多岐にわたり、更にそれらを連成させる必要も出てきます。CAE専門スキルが求められる作業は適時コンサルティングをお願いして進めています。
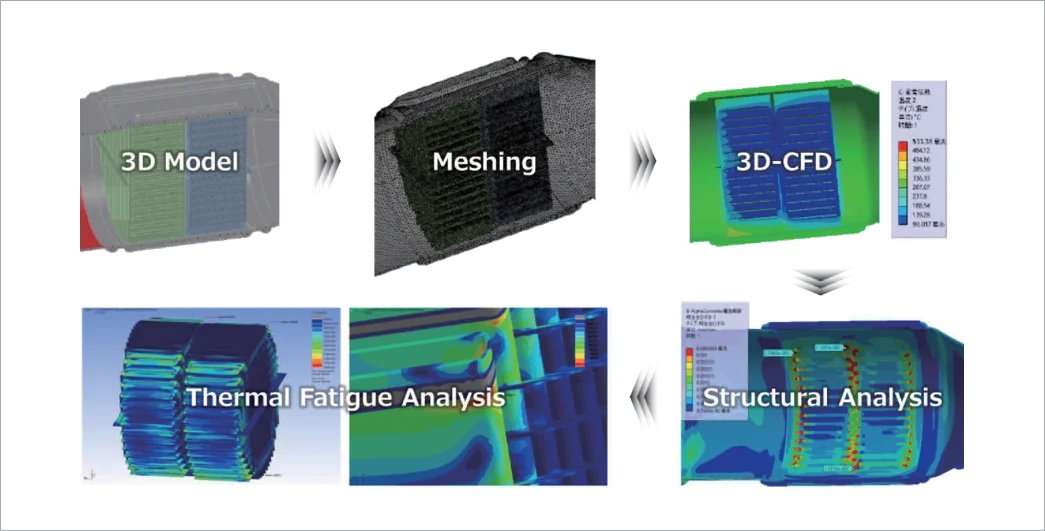
図7 熱交換器の3次元連成解析例
このプロジェクトはどのくらいの人数規模で実施されたのでしょうか?
土佐
現在は基礎研究段階ということもあり、さほど開発リソースをかけられず少数精鋭で研究を進めています。社内外の交流会などで話をすると「そんなに少ないんですか?」と驚かれます。実験を最小限にして、デジタルツール活用で進めていることで、研究内容からのイメージに対してはかなり少人数でできているのだと思われます。
5.いよいよ実車搭載に向けた詳細検討へ
今後はどのような取り組みを実施していく予定でしょうか?
土佐
価値と課題が明確にできた後、実車搭載に向けてシステムおよび各部品を具体的に検討していくことになります。現状では1Dでシステム検討し、3D(図8黄文字)で部品検討するという流れになっていますが、今後は両方向の流れにしていくつもりです。例えば3Dで計算した新構造の熱交換の効率パラメータを1Dモデルに反映しシステム効率の向上効果を確認する、といった具合です。このようなシミュレーションの連携を構築することで、スピード感をもって部品とシステムの最適化が検討できると思います。
また、実用化に向けてはものづくりに取組んでいく必要も出てきます。新しい構造で小型化できることがわかっても、創る技術が伴わなければバーチャルのままで終わってしまいます。ものづくりに関しても近年デジタルツールが使われて進化してきていますし、Additive Manufacturingなど新しいものづくり技術も開発されてきています。本研究でもそれらを積極的に活用し、チャレンジングに取組んでいきたいと思います。
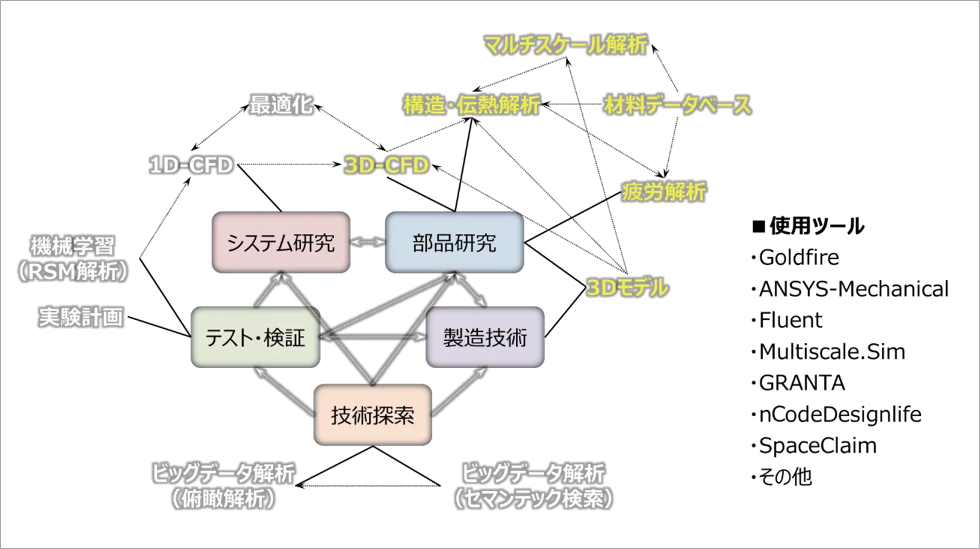
図8 ツール関連図
とても興味深い取り組みについてお話いただきありがとうございました。今後も可能な限りご支援をさせていただければと思います。どうぞよろしくお願いいたします。
この場を借りてお礼申し上げます。