コラム
マシンビジョンとは?設計・開発時の考慮ポイントや設計手順を詳しく解説
MACHINE VISION SOLUTION
製造業での「人手による目視検査」の課題を、高精度かつ安定的に解決する「マシンビジョン」。
その適用シーンから、設計時のカメラ・照明などの選び方まで、詳しく解説いたします。
その適用シーンから、設計時のカメラ・照明などの選び方まで、詳しく解説いたします。
INDEX
- マシンビジョンとは?具体的な活用シーンや構成要素をご紹介
- マシンビジョンの設計・開発において考慮が必要なポイント
- 試作と実験を繰り返さないために:CAEで進める「マシンビジョンの仮想プロトタイピング」
TOPIC 1マシンビジョンとは?具体的な活用シーンや構成要素をご紹介
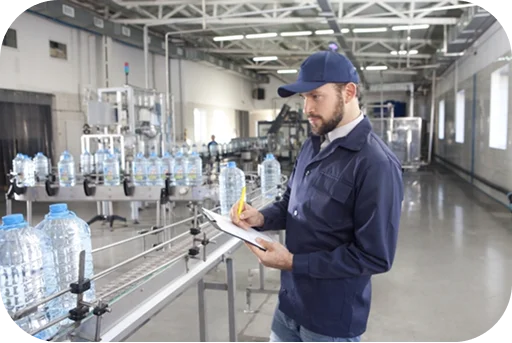
マシンビジョンとは、機械がカメラやセンサーを用いて視覚情報を取得・解析し、自動で判断・動作を行う技術の総称です。
これは単に「カメラで撮ってAIで判定する」ものではなく、一連のシステム設計と制御ロジックの集合体です。
マシンビジョンの処理フロー
①画像の取得(センシング):カメラ・レンズ・照明による高精度な映像の取得
②画像処理・解析:歪み修正、エッジ検出、パターンマッチング、特徴量抽出など
③判断と出力制御:NG/OK判定やロボットアームなどの機構制御と連動
人手の目視検査では「目」と「脳」で行っていた処理を機械で代替・強化することで、高速かつ一貫性のある判断が可能になります。
マシンビジョンの導入により、長年製造現場の課題であった不良品の見逃し・検査員の疲労や熟練度による検査精度のばらつきなどの問題を解決できると考えられています。
マシンビジョンの主な活用分野

マシンビジョンは、特に精度が求められる工程において活用が期待されています。
◆外観検査:キズ、汚れ、欠け、異物混入などの検出
微細な表面欠陥の検出に優れており、電子部品や半導体のクラック検出、食品や医薬品の異物混入検査、自動車部品の塗装ムラやバリ検出などに最適です。
◆寸法測定:ミクロンレベルの寸法許容差検査
サブピクセル解析やキャリブレーション技術を用いることで、高精度な非接触寸法測定が可能になります。製品の内径・外径測定や、レンズや樹脂などの厚み測定、傾きの測定などにも活用できます。
◆部品の識別と仕分け:QRコード読み取りや色識別
製造現場や物流ラインでは、検査の工程だけではなく、部品や製品の自動識別や仕分けにもマシンビジョンが活用されています。1D/2Dバーコード、QRコードの高速読み取りや、製品ラベル・印字の確認(OCR)、色や形状の識別による多品種仕分けを実現します。
◆ロボット誘導:対象物の位置認識と動作制御連携
産業用ロボットは従来、決まった場所に決まった向きで置かれた部品を扱うのが基本でしたが、実際の現場では部品の位置や向きが少しズレていることも多く、そうしたズレを人が直してからロボットに渡す必要がありました。ロボットとマシンビジョンと連携させることで、部品の位置・向き・掴み方などを自動で判別し、部品のピッキングや組み立て作業などをロボット自身が臨機応変に、自律的に作動できるようになるというメリットがあります。
マシンビジョンの4つの基本要素
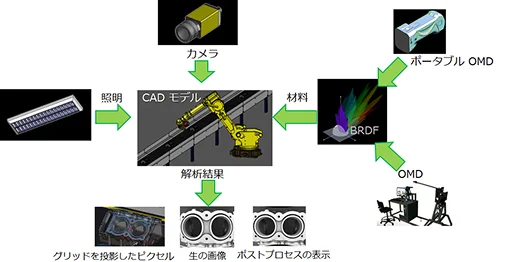
マシンビジョンシステムは、「目」と「脳」にあたるハードウェアとソフトウェアが一体となって初めて成立します。
正確で安定した画像検査を実現するためには、様々な基本構成要素を的確に選定・設計する必要があります。
◆カメラシステム:視覚の解像度と精度を担う中核部品
マシンビジョンにおいて重要なのがカメラシステムです。これらは人間に例えると「目」に相当し、システム全体の“視力”を左右します。撮影対象や作業距離によって、最適なシステムが変わってくるので、要件を満たすような選定を行う必要があります。
◆照明系:画像の見やすさを左右する最重要パートナー
どれほど高性能なカメラを使っても、照明が適切でなければ良い画像は得られません。 光は視覚情報を浮かび上がらせるための鍵であり、単純な明るさだけではなく、「どのような光を、どの角度から、どう当てるか」の総合的な設計が肝心です。
◆撮像環境(視野と背景):検出精度に影響する舞台設計
撮影対象とカメラの位置関係、背景、周囲の環境光などを考慮した撮像環境の最適化も重要です。この段階での設計が甘いと、後工程の画像処理や検査精度に大きな悪影響を及ぼします。
◆画像処理・アルゴリズム:目で見た情報を理解する知能
取得した画像を解析して「良品か不良品か」「どこにあるか」を判断するのが、画像処理・解析アルゴリズムです。例えば寸法検査では、撮影した画像を処理して事前に既定したグリッドの中に部品が収まっているかどうかで良・不良の判定を行います。昨今では、AI/機械学習と組み合わせたアルゴリズムの高機能化も日々進んでいます。
TOPIC 2マシンビジョンの設計・開発において考慮が必要なポイント
マシンビジョンの導入を検討する中で、「できれば自社内で開発・設計したい」と考える技術者は少なくありません。
しかし、カメラの選定・光源条件・視野の設計・画像処理アルゴリズムの適合など、設計の自由度が高い一方で、設計ミスのリスクも高まります。
ここでは、開発時に考慮すべき重要なステップをご紹介します。
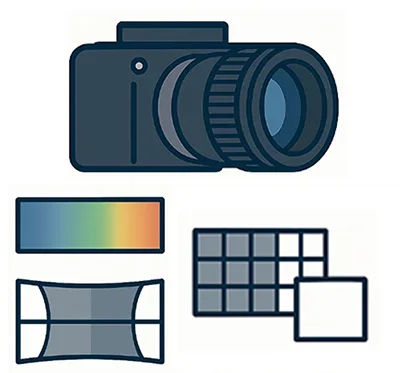
ステップ1:最初に押さえるべきは「カメラと光源の特性設計」
マシンビジョンの性能は、カメラと光源の選定で8割が決まると言っても過言ではありません。
以下のような要素を考慮しながら、目的にあったカメラ・光源を選びます。
◆カメラの性能検討要素
- 解像度:対象物の細部まで捉える能力で、高解像度ほど微細な欠陥を検出できます。
- センサーサイズ:大きいほど受光量が多く、暗所や高速撮影に適用があります。
- スペクトル感度:可視光だけでなく、赤外線や紫外線を使った特殊な検査も可能です。
- 焦点距離・F値:撮影範囲(視野)と被写界深度(ピントの合う範囲)を決定します。
- ディストーション補正:レンズによる歪みを最小限に抑え、寸法測定の精度を保ちます。
◆光源の性能検討要素
- LED照明:多くの用途で使われる標準光源で、指向性や色温度の制御が容易です。
- レーザーライン:3D形状認識や凹凸検出などに使用します。
- 自然光/環境光:使用環境・現場に即した検査が可能ですが、外光の影響を受ける場合の再現性確保が課題になります。
- 照明角度・方向・拡散性の調整:ハレーションや影、反射を抑制し、欠陥を強調する照明設計が肝要です。
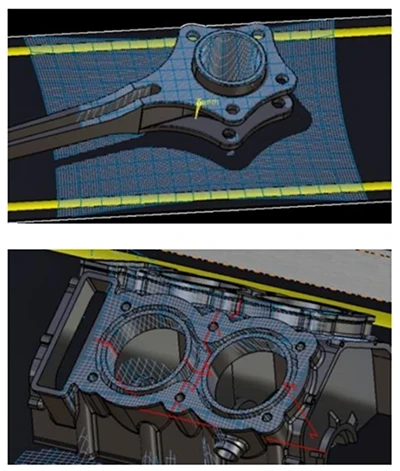
ステップ2:3D環境での視野解析によるカメラ配置の最適化
設計の初期段階では、「どこにどの角度で照明とカメラを設置するか」というレイアウト検討が極めて重要です。
- カメラの視野が検査対象を網羅できているか、解像度は十分か?
- 照明が影を生まず対象を均等に照らせているか?金属部品の光の反射はないか?
- ピントはあっているか?背景色や素材によって対象がみえにくくなっていないか?
これらの項目に対して、最適な配置ができているか、実際にテストを行って確認します。
CAEを用いることで、3D CAD環境での視野可視化をシミュレーションでき、これらの要素を事前に検証・検討できます。
ステップ3:撮影画像の品質とアルゴリズム適合性を見極める
物理設計後は、取得画像の評価とポスト処理が鍵となります。
①焦点距離や分光感度、照明条件などを設定し、カメラ撮影シミュレーションを実行
時間帯や経年によって照明条件や対象物の反射特性が変化する環境では、カメラや照明の周りに
カバーを設置するなどして、一定の条件を保つ必要があります。
②カメラのポスト処理を実行
生の画像のままだとディストーションが発生する場合、
画像加工処理を通してディストーション補正を行うことがあります。
③画像を解析して、形状・寸法不良などを検知する
解析アルゴリズムにはさまざまな手法があり、要件や目的に合わせて最適なものを選ぶことになります。
- 形状認識:輪郭抽出やテンプレートマッチングによるパターン判定が可能です。
- 位置検出:XY座標、角度、奥行きなどの測定による位置決め支援を行います。
- 寸法測定:高精度なサブピクセル演算により、非接触で寸法確認が可能です。
- 分類・識別:バーコード、印字文字、色などによる製品分類や仕分けができます。
- AI・機械学習連携:ディープラーニングを活用した柔軟な不良検出や傾向分析技術の研究が進んでいます。
これらの複雑なステップに対して、治具の作成(試作)や環境テストを通して設計を進めていくのが、マシンビジョン開発の基本的なフローです。
TOPIC 3試作と実験を繰り返さないために:CAEで進める「マシンビジョンの仮想プロトタイピング」
マシンビジョンシステムの開発では、実機テストや治具の試作を重ねながら最適な構成を探っていくのが一般的です。しかし実際に開発を進めていくと、
- カメラや照明の配置を変えるたびに治具を再設計・再製作しなくてはならない
- 設計ミスが判明してからの修正に時間と費用がかかる
- 現場での調整作業が属人化・ブラックボックス化してしまう
といった課題に直面することが少なくありません。
そこで注目されているのが、CAE(Computer Aided Engineering)による仮想プロトタイピングです。
シミュレーションを用いることで、実際に装置を組み立てる前の段階で完成イメージに近い評価が可能になり、実機テストの時間とコストを大幅に削減することができます。
ここでは、光学設計解析ソフトウェアと、実際の機能や解析事例をいくつかご紹介いたします。
光学設計解析ソフトウェアのご紹介
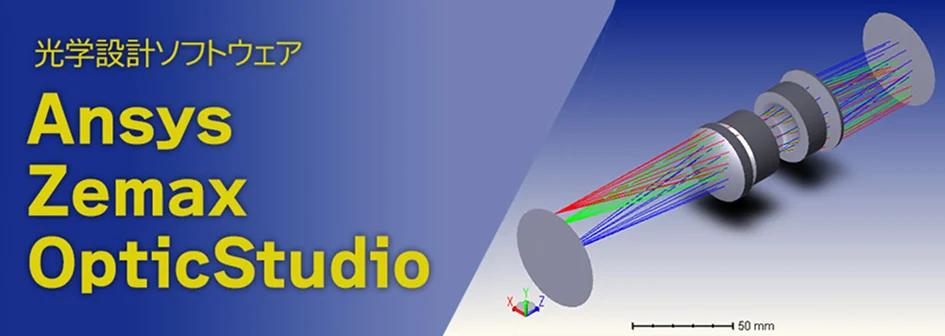
Ansys Zemax OpticStudioは、レンズ設計・光学系の性能解析において世界的に広く活用されているツールです。マシンビジョン用途では、検査対象の大きさや撮影距離に応じた最適な焦点距離やF値を持つレンズをシミュレーションできるほか、歪み補正や周辺光量落ち(ビネッティング)の事前評価も可能です。
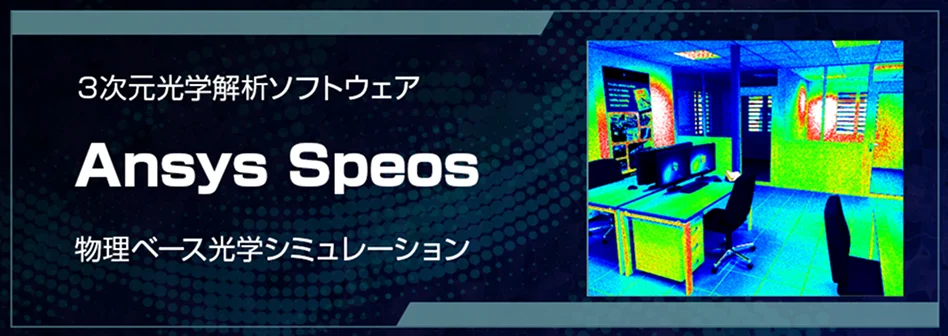
Ansys Speosは照明設計や全体環境の評価に最適なソフトウェアです。マシンビジョンシステムの光源配置を3D CADモデル上で再現することで、影・反射・ハレーションの発生状況をリアルに再現。照明角度や拡散板の設計検討も可能なので、試作前にマシンビジョン装置全体の最適化を行うことができます。
マシンビジョンカメラの設計データをシームレスに連携し、システム全体での撮像を最適化
Ansys Zemax OpticStudio と Ansys Speos はシームレスなツール間連携機能を持っているため、Ansys Zemax OpticStudioで設計したカメラの光学系性能を Ansys Speos にインポートし、撮像環境全体での実画像品質を評価することが可能です。ほかにも、照明・筐体設計とカメラ光学設計の整合性確認や、光学系と照明系を統合した最適設計の検討などを簡便に行うことができ、仮想マシンビジョン環境の構築に役立ちます。
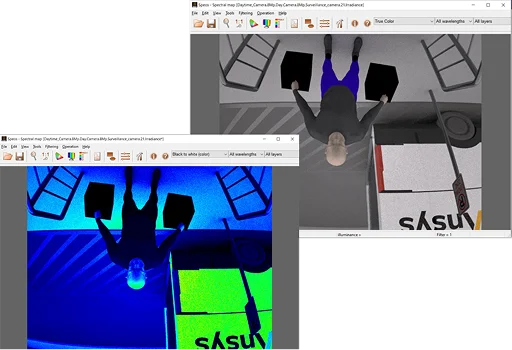
オンデマンドセミナー:小型カメラユニットの設計&迷光解析と3D撮像シミュレーション
監視カメラなどの小型カメラユニットに向けたコンパクトなレンズ設計と、撮影画像のシミュレーションを行った事例です。Ansys Zemax OpticStudioにより、サイズ制約の中で高画質を実現するレンズ設計と迷光解析をシームレスに実施します。さらに、Ansys Speosでは設計データを用いて3Dモデルを対象とした画質評価を行うことで、OpticStudioで設計したデータについて、実使用環境に近い形で性能を検証します。シミュレーション段階でリアルな性能を可視化・対策検討できるため、設計の精度と開発スピードの向上に貢献します。
Ansys Speos「カメラ & LiDAR センサー」機能で、設計・検証を仮想空間で完結
Ansys Speos Premium Sensor ライセンスに実装されている「カメラ & LiDAR センサー」機能を活用すれば、TOPIC 2でご紹介したマシンビジョン設計・開発ステップのすべてをシミュレーション上で再現・検証することができます。
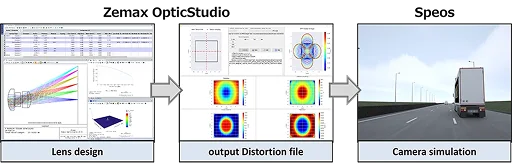
- カメラや光源の位置・角度による視野の変化の可視化
- 照明条件や反射の影響を含めた画像取得のシミュレーション
- 画像処理後のディストーション補正や寸法検証の実行
- 経時変化(時間帯・外光・劣化)の影響を含む検討
これら一連の実施が可能な、センサー評価に特化した機能です。
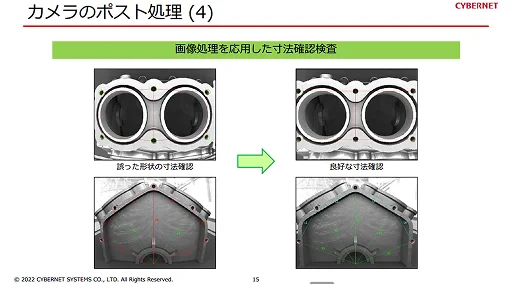
事例資料:カメラ & LiDAR センサー機能を用いたマシンビジョンの解析
カメラ & LiDAR センサー機能を用いて、マシンビジョンの設計・開発を行う事例資料です。
本機能を用いることで、各プロセスの処理や最適化がどのように行えるのかを確認できます。
マシンビジョン開発過程で必要となる解析の一覧や、設定の全体像についても簡単に説明していますので、設計を検討している方はぜひダウンロードしてご覧ください。
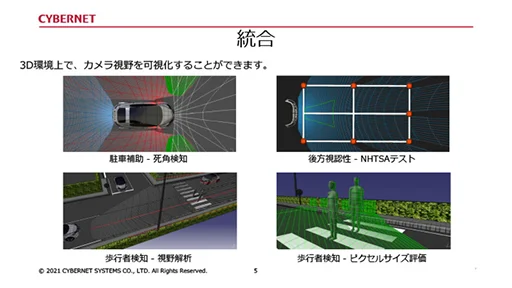
事例資料:カメラ & LiDAR センサー機能を用いた車載用LiDARの設計
車載用LiDARの設計にカメラ & LiDAR センサー機能を用いた事例です。
これにより、車載用LiDARやカメラの取り付け位置・角度、検出範囲などを検証することができるほか、時間帯や天候などを考慮した様々な環境条件での見え方を可視化できます。
カメラ & LiDAR センサー機能でできることを、マシンビジョンとは別の角度からご覧いただけます。
今後の開発スピードを変える“設計手法の転換”
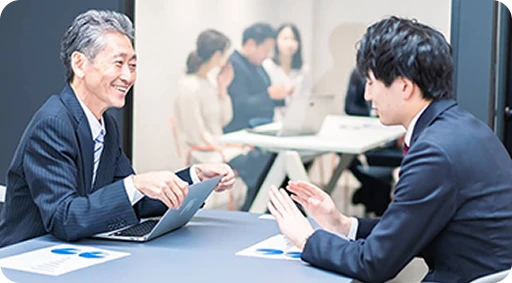
物理試作から脱却し、CAE上で完結できる設計環境を整えることは、開発スピードと品質の両立に直結します。 特にマシンビジョンのようなシステム全体の整合性が重要なシステムにおいては、事前検証の精度こそが競争力となります。
「試作を重ねず、最短ルートで動作検証まで進みたい」
そんな企業様は、ぜひ弊社のシミュレーション支援をご活用ください。
設計から検証、導入までを一気通貫でサポートいたします。