解析事例
解析はあって当たり前という考え方も。CAEが非常に有効なツールであるという認識が社内で向上。
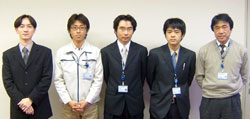
大日本スクリーン製造株式会社様の歴史は古く、前身の石田旭山印刷所が京都で創業されたのは1868年のことです。その後1943年に現在の大日本スクリーン製造となってからは、画像処理技術を中心に、印刷製版関連機器からエレクトロニクス産業に進出するなど幅広く事業展開されています。現在では、印刷関連分野として、印刷工程のデジタル化を促進する機器を、エレクトロニクス分野では半導体・FPD(フラットパネルディスププレイ)、プリント配線基板製造装置などハイテク産業機器を開発・製造し、IT社会の発展に貢献されています。
今回インタビューにご協力下さいましたのは、技術開発センター 機械技術統轄部 第二機械技術部の足立秀喜部長、古村智之係長、梶屋裕之主任、相良秀一様、第一機械技術部の波多野章人係長の皆様です。同社ではAnsysを20年程前からご利用いただいており、現在ではAnsys DesignSpace(以後DesignSpace)を設計部門にも展開されるなど、CAEを製品開発に積極的に活用されています。
(以後社名は大日本スクリーン様と表記させていただき、同社の皆様の敬称は略させていただきます。)
皆様の部門のご紹介と、解析業務などについてご紹介いただけますか。
足立
我々の機械技術統轄部は、全体で約50名、第二機械技術部と呼ばれるところで、現在20名ほどが所属しています。どちらかというと、他部門から依頼で解析を行なうことが主体ですね。当然ながら構造から流体まで解析のバリエーションはあるのですが、あくまでも解析は機械技術部の開発設計におけるツールと位置づけていますので、全員が構造解析も流体解析もできるようにという方向で組織を運営しています。実際はこれら解析業務も、非常に高度な解析から、少し難しい問題、それから普通の設計業務の中で行なう簡単な解析とレベル分けができますので、その中で皆が中級レベルまでは出来るようになって欲しいと考えています。
Ansysを導入いただいた時の経緯を教えて下さいますか。
足立
20年程前に導入したのを記憶しています。最初は節点をテキスト入力していました。導入当時は、構造解析だけの機能だったようですが、その後機能追加をして、アニールの設計のために熱解析などを行なっていました。当時は、熱分布や熱ひずみを主に検証するためにCAE利用を進めていました。
古村
私が最初にAnsysに触れたときは、入社直後でしたが、すでにAnsys PCがあったように記憶しています。黒いDOS画面でしたけど。その頃私が依頼された仕事は磁場解析とフレームの構造解析でした。まだその当時は各拠点で一人解析を行なっていて、時折集まって情報交換するような感じでしたね。
今のように設計の皆さんも使う環境になったのはDesignSpaceのようなツールが出てきたからでしょうか。
足立
設計者が解析も使うという思想は随分前からあったのですが、そういう中でユーザーフレンドリーなツールが出てきたのはインパクトが大きかったですね。DesignSpaceはAutodesk Inventor(以後Inventor)を導入した後すぐ使い始めていますので、もう使い始めて5年くらいになりますね。
DesignSpaceの導入は、機械技術統轄部から全社推進という形で始められたのですか。
古村
DesignSpaceの選定は我々の部門で行いました。これは既に導入されていたAnsysとの親和性を考慮したものです。導入自体は3次元CADのInventorと一緒に、CAD推進のグループにより全社展開の形で行われました。我々の部門では身近にAnsysなどが存在していたことから、比較的スムーズに活用されていると思います。他の部門については部門毎に活用にばらつきはあると思いますが、ずいぶん活用の度合いが増えてきていると感じています。というのも、最近DesignSpaceに対する質問をよく耳にするようになってきていますので。
足立
実は3次元CADを推進するということでDesignSpaceを導入したのですが、私が聞いたところですと、DesignSpaceを使うために3次元CADを使うという現象まで出てきたみたいですね。本末転倒ですが。でも導入して5年たってCADも機能的に満足できるところまで来ているので、本格運用は本当にこれからです。
波多野
私のいる第一機械技術部では、別の3次元CADでOneSpace Designer Modeling(以後OneSpace)を使っています。もともとメディアテクノロジー関係で、コクリエイトの2次元CADを使っており、その経緯でOneSpaceを利用しています。つまり半導体部門と、印刷製版関係の部門で異なるCADを運用している状況です。2次元CADの時代も2種類のCADで運用されてきた経緯で、3次元化したときにもその流れで結局2種類にわかれてしまったわけです。全社的には基幹ソフトを一つにしたいという希望はありますが、どちらの開発も大事ですし、今はそれで設計が上手くいっているのであれば、設計実務者の負担を考えると、無理やり統一しなくてもいいと個人的には考えています。
CAEを一本化するのは難しいと思いますが、解析の評価基準を統一しようというような動きはありますでしょうか。
足立
今我々がやっていることをデーターベース化して、検索できる環境づくりをすること、そして誰からもそういう技術データを検索できるシステムにすることなどに取り組んでいます。
梶屋
また社内において設計・解析技術交流会というものを開催しております。名称を設計・解析としているのは、解析技術だけではなく、設計開発技術を含めた技術交流を行いたいという意図が含まれています。ここでは社内各部門の解析や設計開発業務の担当者が集い、技術的な内容をはじめとして、解析システムの導入や運用、活用方法など、様々なテーマについて情報交換をしています。これは我々第二機械技術部が中心となって、全社展開、推進を図っているものです。
古村
現実的に構造系のCAEはDesignSpaceを含めてAnsysしかありませんので、そういう交流会を通じて、各カンパニーを支援していければと思っています。本当のところは、数値計算を活用しているところと、使いたくても使えていないところがありますので、設計製造のプロセスの中で数値計算の効果への認知度をもっと高めてもらって、同時に我々も十分支援できる体制を構築できればいいと考えています。私どもとしては専門性を高めて、専門職としてやっていきたいという思いもあるのですが、まだまだ布教活動としてフォローにまわらないといけないことや、設計との親和性も高めることを考える必要性もあります。ですから、もう少し軌道にのってくれば、個々に専門性を高めていって、各カンパニーが困ったときにはこちらに頼って来てもらえるような部署になれればと思っています。
現場を支援すると言う意味では、導入効果や推進度合をどうやって評価されていますか。また布教活動としては経営者に対してのコスト効果の報告なども必要のようですが。
足立
現在は、スポット的な依頼解析が多いのですが、同時に効果がこれだけ出ましたという成果報告も行なっています。そういう数値的な報告も出していかないと、経営としても理解しにくいと思います。CAEも3次元CADも、フロントローディングにより、トータル時間短縮になるという認識が、まだまだ管理職の方々に納得してもらい難いところです。そこが上手くいかないと、時間がかかるなら2次元でやればいいとかこれまでどおり試作からやればいいというふうに元に戻ってしまいますね。ですから何回も試行錯誤をするのではなくて、CAEできっちりとしたものを作れるところまで検討してから一度で正しく設計する方法が、いかにコストダウンや短納期に繋がるかをしっかりアピールしていきたいと思っています。
古村
それから社内での評価指標を作りたいという話が出たことがあります。投資額に対して、効果がどれほどのものかなど、依頼された方の満足度を数値化するのは大事だと考えているところです。依頼解析の打ち合わせの中で、何をもって設計に反映してもらえるかをこちら側でも認識したうえで計算には入れば、最終的な到達点が分かりますし、同時にこちらの出来ること、出来ないことも理解してもらうことも必要ですし。単に計算屋さんとして見られるのではなく、設計にちゃんと反映してもらえるようにと、ここ数年で意識改革も行なわれてきました。
そういう機運が社内的にも高まっているのですね。
足立
成果物として提出したものが、きちっと評価されるようになってきたので、CAEが非常に有効なツールであるという認識が社内で向上したと思います。それまでは請負の構造解析をしてほしいという場合は、ものづくりのための解析ではなくて、出来あがったものがどうなっているか、極端に言えば視覚的に見せるためだけのツールとしての捉え方があったのですが、最近は、簡単に作れないものが多くなってきまして、次第に解析技術の重要性を理解してもらえるようになってきていると感じています。
梶屋
もっといえば、昔は確かにコストや時間を削減できたから効果があるという見方もしていたのですが、最近では更に、解析無しで開発をするのが困難になってきていて、解析があって当たり前という考え方もされているんですよ。解析からのアプローチを用いてはじめて把握される現象も有りますし、これらを評価して設計に活かすなど、深いところまで追求していくと製品の質にまで影響してきます。ですから、今では単にコストや時間だけの問題ではないですよね。
波多野
私は3年程前までは、ここにいるメンバーと同じ第二機械技術部で解析を専任で行なっていたのですが、今の設計現場に移ってからは、解析の必要性は感じているものの、高度なシミュレーションにチャレンジする時間が無く、非常にジレンマを感じています。しかし、お客様に対して製品を紹介する際に解析結果をお見せすることで、製品の付加価値もあがりますし、開発リードタイムの短縮等、設計現場にいても解析が非常に有効な手段であることを感じます。
ではAnsysの機能についてご意見をいただきたいのですが。
梶屋
他のAnsysユーザさんからも聞きますが、プリポストとソルバーの環境が同じなのはいいですね。他のツールで組み合わせて使ったこともありますが、やはり煩わしいのでAnsysのトータルな環境はいいです。計算を個々に流すだけであれば多少煩雑でもいいのかもしれませんが、実際の業務では計算の数も多くデータの管理も結構たいへんなので、その度にCADデータとメッシュデータとソルバーデータがあると、それだけで煩わしいのです。Ansysの場合はその辺の管理も楽なので助かりますね。他には特に不満を感じたことはないですし、Ansys以外のものを使う機会があったときに、Ansysの操作性のよさを逆に実感するという感じです。
古村
モデリングからメッシュを切って計算して結果を処理するまで一連の環境を提供するというコンセプトを、最初から掲げているのはすばらしいと思います。でも最近周りからよく聞かれることはDesignSpaceとWorkbenchとAnsysとの関係が理解されていないようで、そこがもう少しわかりやすいとありがたいです。我々はバッチで計算することが多いので、昔からあるAnsysの環境を使っていますが。
梶屋
ただ、これから使いたいという人はDesignSpaceに手を出しつつあるので、それが浸透していくといいですね。初めての人にはDesignSpaceは解析の入り口としてはいいと思います。要望としては、DesignSpaceからAnsysにデータを持ってくるとき、またその逆もそうですが、もう少し入出力が意識しないでもできるくらいに便利になるといいですね。
相良
私は入社一年目なのですが、入社直後からDesignSpaceではなくAnsysを主に使っています。初めは、複雑な操作が必要かと思っていましたが、いざ使ってみたら意外に簡単なので驚きました。ただ、ヘルプに英語がたくさん並んでいて、使いたいコマンドのヘルプを見ると全部英語で書かれていたりするので、使わずじまいということもあります。それが全部日本語だと、こちらももっと使うようになると思うので、もったいないですよね。でも、操作が難しくて困るということは感じなかったです。
Ansysの従来環境は、機能ごとのGUI構成になっているのですが、Workbenchはオブジェクト志向型なので、何を目的に作業を進めるかがわかりやすいのです。逆に解析の専門家の方は、目的を理解した上で操作をされているので、従来のAnsysのような機能志向型がわかりやすいのかもしれないですね。
では具体的な解析事例についてご紹介いただけますでしょうか?
波多野
3年程前に実施した露光装置描画ヘッドにおける熱変形解析をご紹介します。この露光装置は、マスクを使って露光する代わりにCADデータから直接基板にパターニングすることで、基板の様々な露光パターンに対して柔軟であるというのが売りですね。その描画ヘッドから光が出てパターンニングをする際に、熱が原因と考えられるビーム位置の変動が問題になっていました。要因としては、光源から発生する熱によるヘッド周辺の雰囲気の温度上昇、また、描画ヘッドについているモータによる発熱などが考えられるのですが、これを検証するために解析を行ないました。熱解析では境界条件の最適化等、実現象との整合性を取る部分が難しく、また、時間も要してしまいますので、このときは、絶対値を見るというよりはどういう変形が起こるか傾向を見るというスタンスで解析を実施しました。熱変形解析は2種類行なっていまして、まず一つは光源からの熱で全体の温度が上昇した場合の変形を見ています。解析手法は定常状態の熱と上昇温度を入力して計算を行ないました。この図で言うと当然上に向かって伸びるのですが、このなかには主要な光学レンズ等が乗っており、雰囲気温度の上昇により、それらが傾きを持ってしまう事が解ります。例えば対物レンズホルダーもズームレンズホルダーも傾きがでてくることがわかります。これはガイドが鉄でベースがアルミですので、固定していて熱を加えると、バイメタル構造が原因で変形するのですね。
次に一部にモータをつけた場合の変形を見るために、まず伝熱解析をして、その結果を境界条件にして熱ひずみの解析をしています。この場合も主要な部品が傾きを持っており、実験結果と比較しても近い値が出ています。レンズが傾いた場合に露光位置ずれがいくら発生するかが既にデータとしてありますので、最終的に許容される露光位置ずれから傾きの許容量を割り出して、その許容量になるまでいろいろな部材や構造を変えて解析を進めました。最終目標は熱による露光位置ずれが1ミクロン以内です。全部鉄にするとおさまる話なのですが、鉄にすればかなり重くなるので、鉄を採用するだけではなく、構造の最適化を図ったり、片持ち的な部分を改良したりして、目標は達成しました。
解析事例1: 露光装置描写ヘッドにおける熱変形解析
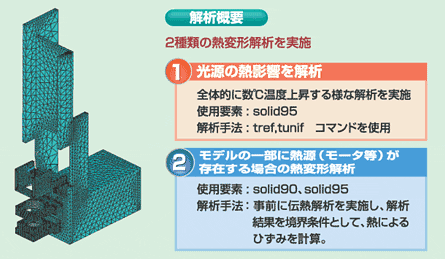
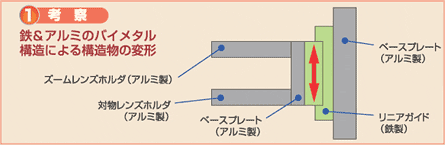
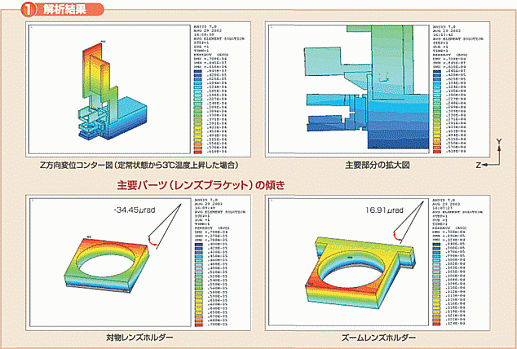
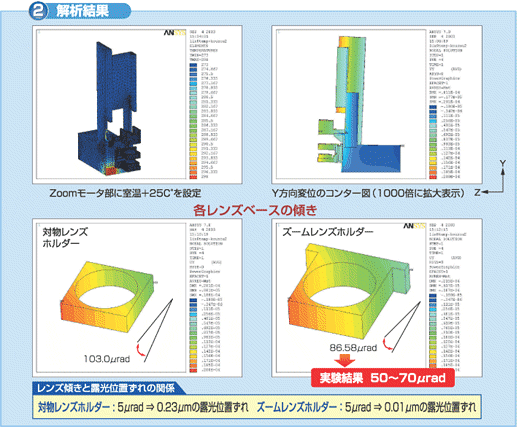
この解析自体はどれくらい時間を掛けられていますか。
波多野
2〜3週間から1ヶ月程です。モデルを作って試し計算をし、設計の方に渡すところまでΩですね。再度パラメータを入れて最適化をするところまで入れると、もっと時間はかかっていると思います。
古村
こちらの解析は、FPD製造装置開発への解析適用事例です。最近では液晶TVの大型化が加速度的に進んでいますから、当社でもそのニーズに対応した大型基板対応装置の開発を積極的に進めています。またそのような装置開発にも短納期、試作レスが求められますから、解析により効率よく開発をすることが必要なのですね。液晶の製造プロセスでは、洗浄、成膜からレジストコーティング、露光、レジスト剥離、エッチング、現像、そして検査、液晶充填、組み立てという工程がありますが、ここで紹介する解析事例は、レジストコーティングの工程に使われる装置のモーダル解析とその最適化の事例です。ちなみに、レジストコーティングとは、電極となる透明な金属膜が形成されたガラス基板上に、スリット塗布を使ってレジスト液を均一に塗布する工程のことを指します。この解析は、まず個々の部品について、詳細モデルの作成と計測を実施し、実験モーダル解析を行なうことによって対象物の振動特性を把握しています。その後モデルをアセンブリに変えて、モデルの妥当性を検証しました。ここでお見せしている解析結果は、さらに次世代の装置へ展開した例で、装置全体モデルを使って1次から5次までのモードを計算しています。これと実測による結果を比較すると、解析結果が妥当であることがよくわかると思います。最後に静解析を行なうことで、最適な構造を求めています。これは、2005年のAnsys Conferenceでも発表した事例で、社内でも解析で効果をあげた例として報告していまして、CAEの社内啓蒙にも役立っています。
解析事例2: FPD製造装置開発における適用事例
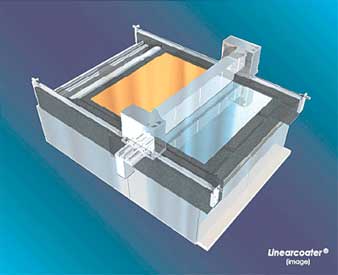
Resist Coating System Linearcoater
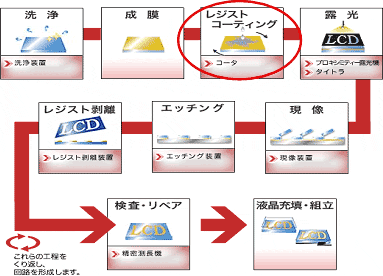
液晶製造プロセス
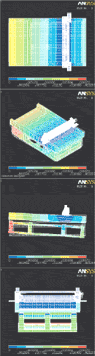
FEM(1次モード)
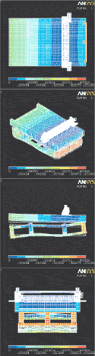
FEM(1次モード)
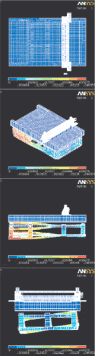
FEM(1次モード)
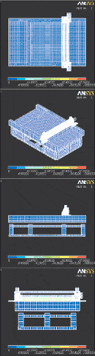
FEM(1次モード)
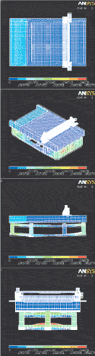
FEM(1次モード)
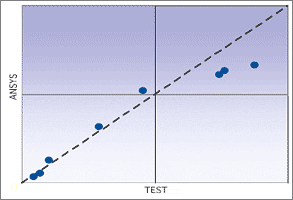
実験とAnsysによる計算結果の固有振動数の比較
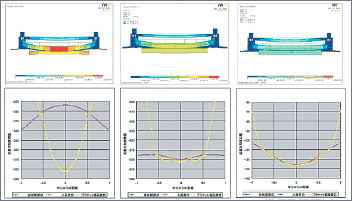
構造最適化検討事例
ありがとうございました。Ansys Conferenceでも反響が大きかったと聞いています。では最後にサイバネットシステムやAnsysに対しての要望事項をお聞かせくださいますか。
古村
他のCAEに比べれば、Ansysの日本語化は充実していますよね。またQuickAでのサポートが始まってからは、質問に対する満足度が高いので助かっています。要望としては、最近特にDesignSpaceの質問を受けることが多くなってきましたので、DesignSpaceを利用するような設計者のためのFAQがあるといいですね。また、操作を進めていくときに脆性と延性を選択したり、接触ブランチを使ったりというところで、何を使えばいいか、それにどういう意味があるのかがしっかり説明されているといいと思います。
波多野
簡単なひずみの解析から熱解析や振動解析にステップアップするときに、一番障害になるのがいろんな係数です。熱伝達係数とか、減衰係数とか、そういうのがわからなくて止まっている人も多いと思います。実際はユーザ毎に計って入力しないといけないのでしょうが、QuickAなどでまずは経験則からで結構ですから、方向付けをできるような参考値だけでも教えてもらえるとありがたいです。
梶屋
DesignSpaceを使う人にとっては解析技術そのものを理解,習得することに対する重要性は高くなく、必要な計算結果を出来るだけ早く得ることが大切なのですが、いざDesignSpaceを使おうとすると,例えば接触の条件を選ばないといけなくなり、そこで止まってしまうわけです。ですから、条件設定などに対するおおよその目安が何かあってもいいのかなと思います。係数なら技術的な本を見れば載っていますが、接触の話はそれこそ解析特有の話ですので、それは一般の設計者にとっては時間を割いて学ぶべき知識ではないですし、気にしなくてもいいようにして欲しいですね。
ご意見どうもありがとうございます。これからは設計者の方にも安心して使っていただけるようなサービス面での支援も強化していきたいと思っております。
大日本スクリーン製造株式会社の皆様には、お忙しい中インタビューにご協力いただきまして誠にありがとうございました。この場をお借りして御礼申し上げます。
「CAEのあるものづくり2006,Vol.4」に掲載