ユーザー事例
アルパインにおけるOptimusを利用した最適化解析と、技術者に向けたスキルアップ支援の取り組み
アルパイン株式会社 木下 佳久 様
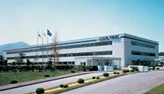
いわき本社
アルパイン株式会社様は、1967年創業以来、車室内での快適なドライブを実現すべくカーナビ、カーオーディオなどの車載音響機器、情報通信機器の開発・製造・販売によってクオリティの高い製品をいち早く市場に提供し続けています。
今回インタビューにお答えいただいた木下様の所属する「機構製品開発部」(福島県いわき本社)は筐体設計、メカ設計など機械系の技術者が集まった設計部門で、「製品の軽量化・燃費向上」「開発期間の短縮化」など自動車メーカー様からの厳しい設計要求に応えるべく、設計プロセスの改善に取り組んでおられます。
今回は、自動車メーカー様との打ち合わせ時や、設計の優先順位を決める際にOptimusをどのように活用しているかをご紹介いただきます。
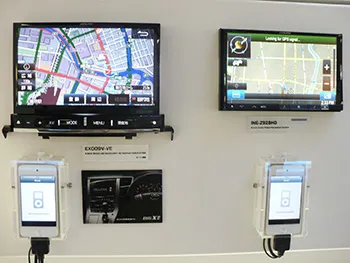
アルパイン製品
木下さんの所属する機構製品開発部の主な業務を教えてください。
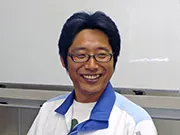
自動車メーカー様との打合せの中では、Optimusはどのように活用されているのでしょうか?
自動車メーカー様には、より品質の高い製品をより早く市場投入したい気持ちがあります。そのため様々な要求を頂きます。こうしたお客様の高いご要望にお応えするための手段のひとつに最適化解析は有効だと思っております。設計方針の判断を早くしつつ、設計完成度も高めていく、スピードと品質の両方を向上させる事が出来るのが最適化解析「Optimus」の効果だと思っています。
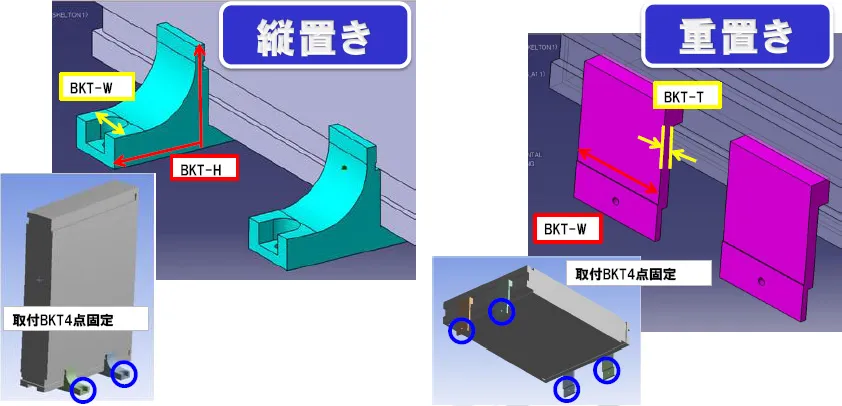
例えば製品の取り付け部を3点固定にするか4点固定にするかを自動車メーカー様と弊社との間で検討する場合、3点固定にすれば自動車に取り付ける作業工数を減らせるという利点があります。一方で固定箇所を減らすと1部品にかかる応力は高くなり設計の難易度も上がるため、より信頼性や余裕を持たせた形状を優先して4点固定にする考え方もあります。迅速に判断して次の工程へ進めたい場面であっても、双方が納得できる結論に至らない場合は検討が長引くこともあり、その結果、開発工程にも影響を及ぼしてしまいます。このような場面でOptimusを使うと、限界値や効果の根拠を相手に伝えやすくなりますし、異なる意見が出てもデータを元に検討できるため、仕様を早期に決定する事が出来ると思っております。
社内的にはどのような使い方をされているのでしょうか。
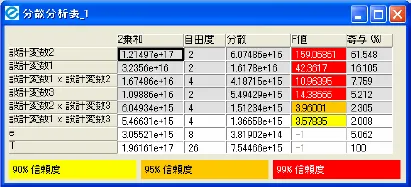
分散分析表
設計者がある目標の最適値に近づける際に、「どの数値が効いているのか?」「どの箇所から検討すれば良いのか?」という点がわかれば、優先順位がつけられ必要な箇所の設計に注力することができます。
その優先順位を決める1つの方法として、Optimusの「分散分析表」はそれぞれの寄与度率が何%なのかを具体的な数値で表示してくれるので便利だと思っております。この機能は以前から品質工学(直交表)には対応していましたが、Optimus Revision 10.9以降は直交表以外の実験計画法でも利用が出来る様になりましたので以前よりも頻繁に利用するようになりました。
具体的には、対象がアセンブリ部品の場合は、板厚をある一定の数値で振る事で、どの項目に何%効いているのかが一瞬でわかります。経験のある設計者なら改善部位を特定する事は出来ますが、その部位がどれくらい支配的に利くのかを具体的に数値で示すのは経験豊富な設計者でも難しいと思っております。設計変更の時間とコストの兼ね合いから、どの部位から着手すべきかが判断しやすいのは非常に有効だと思っています。最終的な最適化解析までCAEを使って求めるには計算負荷が大きすぎて非現実的ですので、まずは実験計画法に基づいて寄与度率を出し、対処すべき箇所を決めて計算を行うことが多いです。また、「相関図」や「相関散布図」も交互作用や対策の全体観を掴むには有効だと思って使用しております。
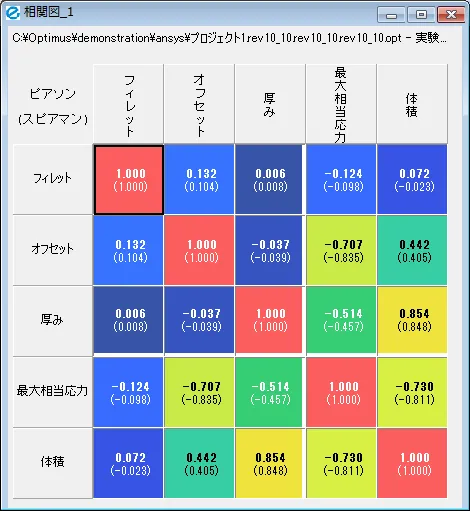
相関図
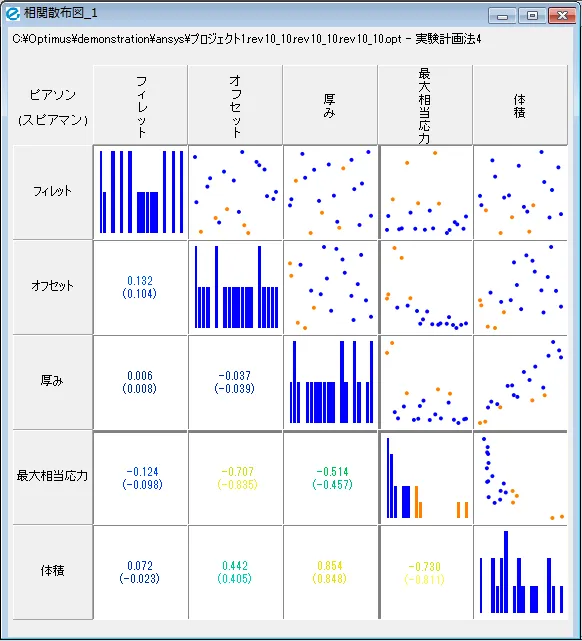
相関散布図
また、ツール間の連携がスムーズに出来るかが重要だと思います。構造解析系のソフトは比較的親和性が高いですが、Linux上で動かしているCAEはPCの知識が必要でしきいが高いと思っています。
あと、解析にかかる時間も重要だと思っております。以前、PSpice(アナログ・デジタル混在回路シミュレータ)とOptimusを連携して計算を行った時は、1回の計算時間がExcel並みに短かったです。通常、構造系のCAEだと2〜3日かけて感度解析を行っていますが、PSpiceとOptimusを連携して最適化手法を7〜8個計算しても半日程度で終わってしまいました。また、PSpice本体にある最適化機能だけでは感度解析は出来ても交互作用の解析は出来ませんがOptimusを連携させることで交互作用も検討できる点もメリットだと思います。
もしOptimusを使わないとしたらどのように解析を進めるのでしょうか?
設計者の工学的知識と経験で判断するしかないと思っています。しかしながら、ベテランの設計者はいろいろな事に思考が広がり検討範囲を広げられますが、効果が低い部位の改善に多くの時間を割いてしまっては逆効果です。本当に必要な検討は何かを示唆するには裏付けがないと難しいと思います。その点Optimusを利用する事で、考える領域をしっかり絞ることができ、部品コスト・人間のリソース・設計時間を短縮する事が可能だと思っております。
Optimusの操作性、利便性などのオペレーション面はいかがでしょうか?
最初のオペレーションを習得するのに半日もかからなかった事を覚えています。最適化ツールは使いこなすのが難しいと思われがちですが、難しいのはオペレーション面ではなく結果処理の方だと思います。知りたい情報を表現するにはどういった結果表示が良いかを、色々な表示を見ながら自分の考察と重ね合わせる作業に慣れるには多少時間がかかるかも知れません。
サイバネットの技術サポートはいかがですか?
質問に対する回答がとても早いですし、細かいところまでしっかり調べて回答してくれます。例えば「このJAVAのエラーについて教えてほしい」と聞けば、そのエラーの事はもちろんですが質問した内容だけでなく更に細かい所まで調べて回答が返ってきます。なぜそのエラーが出たのか詳しい説明をいただく事で、こちらもきちんと理解できるので納得して利用出来ています。
また、以前にOptimusの機能改善の要望を伝えたら次のバージョンアップで反映させてもらった事がありました。弊社のような日本の1企業の意見を取り入れた開発をしてくれる点でもサポートに満足しています。
サイバネット全体として貴社のお役にたてる点などご要望があればお聞かせ下さい。
理論教育の場を提供していただければありがたいです。
何か新しい解析分野に手を出したいと思った時に、独学で統計学の勉強を始めるのはなかなか敷居が高いですし、弊社(福島県いわき市)からはセミナー受講のために東京に出張するのも大変です。従ってWebセミナーであれば社内にいながら参加できますし、後日録画などで複数回聞きなおせるのも利用しやすいので充実して頂ける事を希望します。
ありがとうございます。最後にアルパイン様の今後のOptimusを利用した取り組みとしては、どの様な事を考えているのでしょうか。
1人が1領域担当では仕事の範囲は狭まってしまいます。強度解析をやるにも樹脂成型がわからないと結果の考察は深くはなりません。複数の領域を知っているからこそ自分の特定領域がより深く考察できると思っています。特定の分野を究め、そのスキルを自らの軸に据えつつ、さらにそれ以外の解析についても幅広い知見を併せ持っているT型人間になれるための手段のひとつとして、Optimusが活用出来ればと思います。
木下さん、本日は貴重なお時間をいただきありがとうございました。