資料ダウンロード|分野別ソリューション
樹脂部品の形状最適化
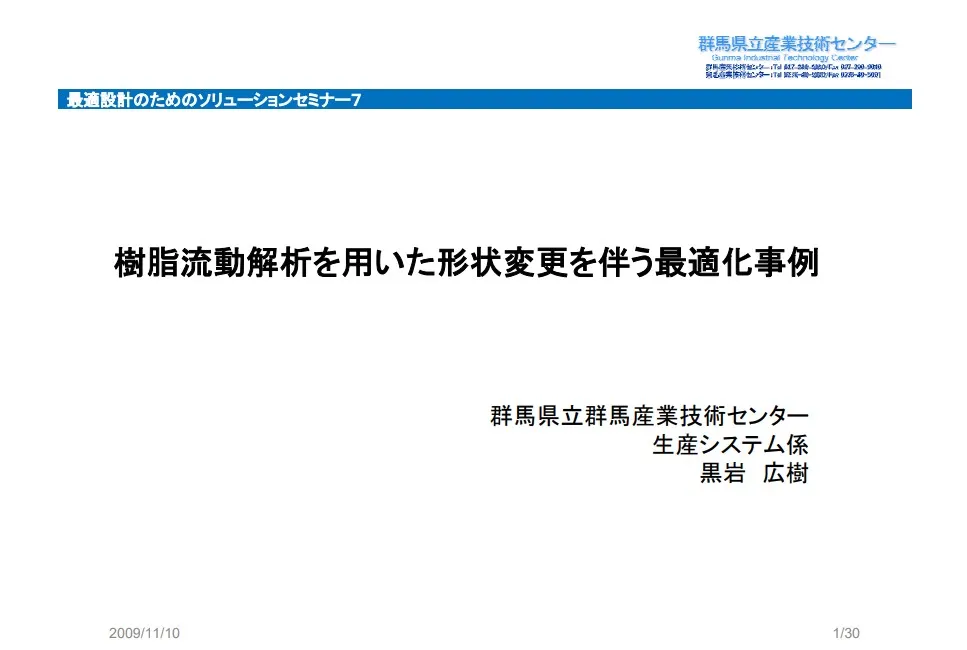
「開かれたセンター」と「産学官連携の拠点」というコンセプトのもと、技術支援、開発研究、情報提供の3本柱を通じて中小企業を支援されている群馬産業技術センター様。地球温暖化問題に対して、車体の軽量化が重要であると考えていらっしゃいます。樹脂部品の形状の最適化、形状・成形条件の最適化、樹脂化における課題の最適化など、樹脂化における課題解決に取り組んでおられますが、本資料では、自動車の運転席の操作パネルを対象とした、樹脂部品の形状最適化事例をご紹介いただきます。
最適化方法
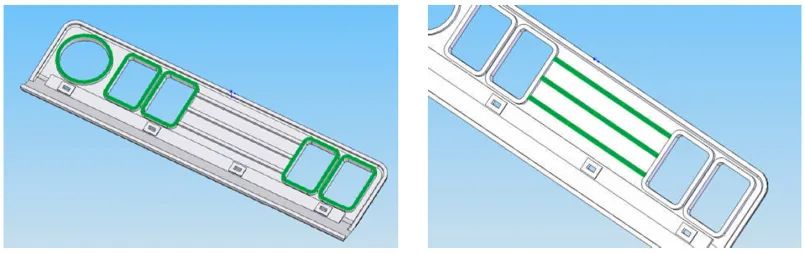
Optimus+SpaceClaim+MPI (Moldflow Plastic Insight) を用いて、変形量と重量が最小となる形状検討を行います。目標は、意匠面や穴位置を変えず、裏面のリブ寸法をパラメータとし、変形量と重量が最小となるように最適化解析を行うことです。SpaceClaimを用いて各パラメータのモデルを作成します。評価値は、変形量と重量がもっとも小さいことです。ゲート位置は固定です。
シミュレーション結果:実験計画法
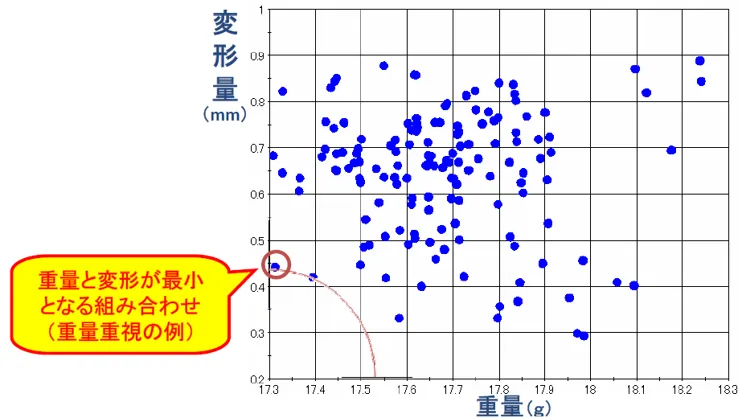
PCが空いている時間帯を有効利用して結果を得るため、金・土・日曜日の3日間でシミュレーションを実施しました。変形量と重量に対して効果のある設計パラメータを調べるため、実験計画法(ラテン超方格法)を選択しました。散布図から、重量と変形が最小となる組み合わせを決定しました。
シミュレーション結果:相関係数
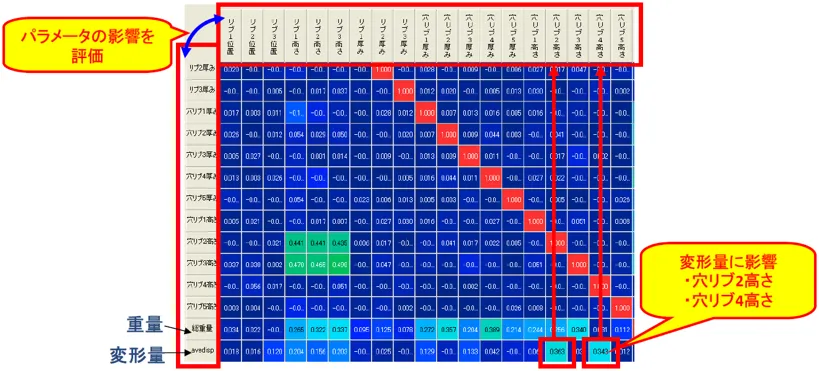
相関係数を利用して、設計パラメータの絞込みを行います。変形量に影響しているのは、穴周りのリブ2の高さ、穴周りのリブ4の高さであることがわかります。このように、設計において重要なパラメータを検討します。最適化前と比較し、変形量50%減・重量7%減の形状を求めることができました。
課題・問題点
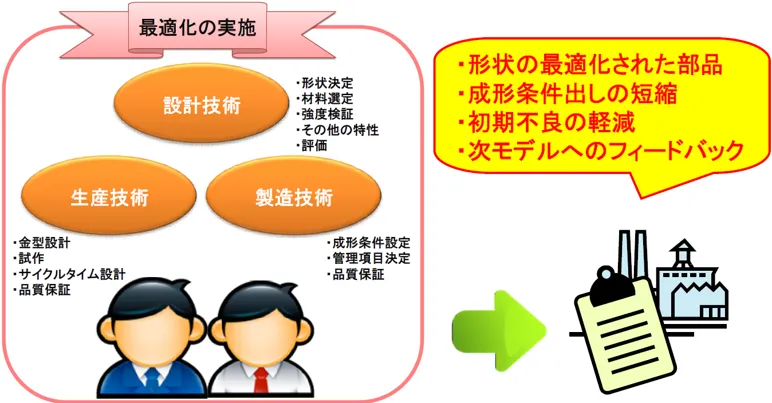
最適化の課題・問題点として以下の3点が挙げられます。
①設計者が最適化を行うには、CAE解析者のサポートが重要であること
②解析結果と実際のものとの検証を行う必要があるため、解析と試作の比較から解析技術の向上を図ること
③解析時間がかからないよう、どの部品を最適化するかしないかの線引をすること
*続きはダウンロードしてお読みください。