資料ダウンロード|分野別ソリューション
射出成形シミュレーションを用いたパネル製品形状の最適化
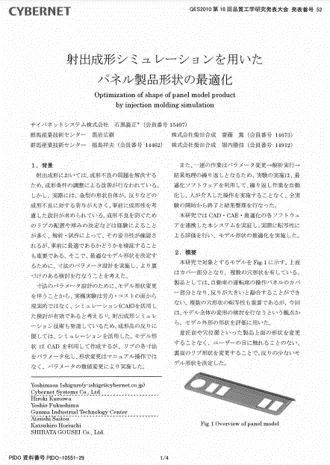
射出成形においては、成形不良の問題を解決するため、成形条件の調整による改善が行われています。しかし実際には、金型の形状自体が、反りなどの成形不良に対する寄与が大きく、事前に成形性を考慮した設計が求められています。最適なモデル形状を決定するために、寸法のパラメータ設計を実施し、より裏付けのある検討を行います。本研究では、CAD・CAE・最適化の各ソフトウェアを連携したシステムを検証し、実際に転写性による評価を行い、モデル形状の最適化を実施しました。
射出成形の形状評価
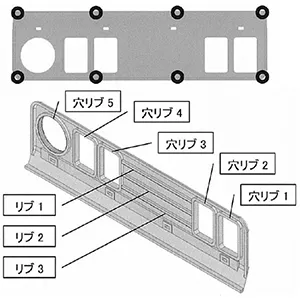
本研究で対象とするモデルを右に示します。上面はカバー部分となり、複数の穴形状を有しています。意匠面や穴位置といった製品上面の形状を変更することなく、ユーザーの目に触れることのない、裏面のリブ形状を変更することで、反りの少ないモデル形状を決定します。解析前のモデル形状寸法を入力信号Mとし、出力yには解析によって得られた反りを考慮した変形後の解析結果形状寸法を用います。形状の特長点を8点として、この8点から得られるすべての2点間の組み合わせ、全28寸法を出力として評価します。図内の○印は、形状評価に使用し節点位置を示しています。
制御因子と誤差因子
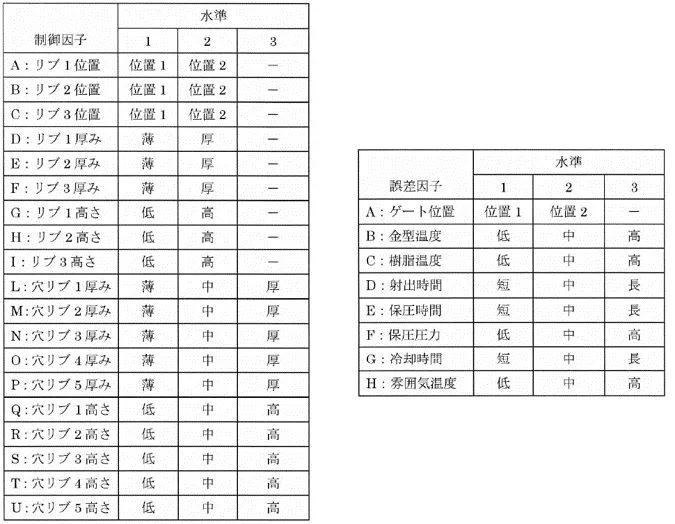
制御因子は、左側の表に示すような成形条件としました。従来は、経験的に形状が決められていた製品裏面のリブの高さ、厚み、位置などを制御因子として選択しました。直交表にはL36直交表を使用しました。
今回は、形状寸法を制御因子としたので、成形条件等を誤差因子にしました。すでに決定されていた成形条件を第2水準として、類似の検討より、水準値を決定しました。誤差因子の組み合わせにはL18直交表を用いました。
システムの構築と解析の実施
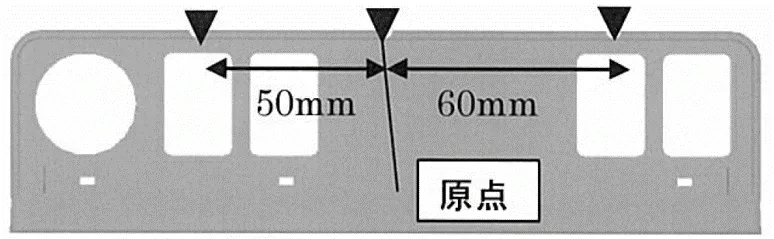
モデル作成にはSolidWorks、SolidWorksからのモデル読み込みと形状変更のためのパラメータ化にはSpaceClaim、射出成形シミュレーションにはAutodesk Moldflow Insight、最適化にはOptimusを用いました。直交表への割り付け、水準値の入力、形状変更、解析実行、結果処理を自動実行するシステムを構築しました。要素数は形状ごとに異なりますが、約14000程度、充填+保圧+反りの解析を行いました。ただし、ランナーやスプルーなどは除き、樹脂注入点のみを指定しました。ゲート位置は、右図に示す通りです。また、冷却管配置も省略したため、金型温度はモデル全体に均一に分布しています。
結果と考察
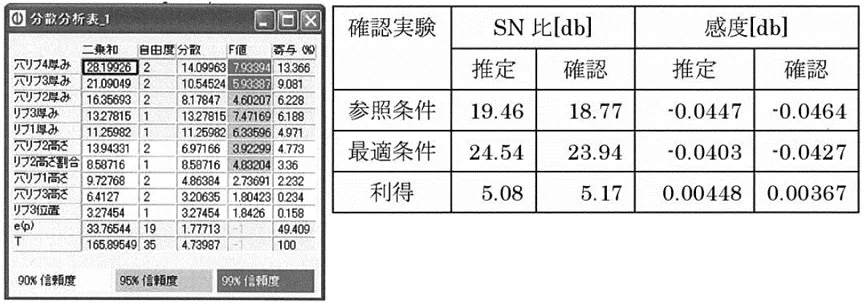
左側の図に示す分散分析の結果により、SN比に効果を持つ因子を判定しました。今回のモデルでは、穴周りのリブについて、形状が厚く、低いものがSN比が高くなる傾向にあることが分かりました。転写性の検討では、SN比が高い水準の組み合わせを選択し、そのバラツキを考慮して感度をチューニングします。右側の表はその結果を示しています。SN比に関しては5.17dbの利得を得ることができました。また、推定値と確認実験の利得差は小さく、再現性を確認することができました。
*続きはダウンロードしてお読みください。