製品情報
事例アプリケーション
Dynaformにより、下記解析結果を出力することができますので、試作の前の事前検証及び試作とシミュレーションとの整合性について各種検証することが可能です。
- 成形不良(しわ、ひび割れなど)の評価機能
- 成形限界線図(FLD)による評価機能
- 板厚減少率やひずみのコンタ図
- サークルグリッド
Blank Size Engineering (BSE)モジュール
DynaformのBlank Size Engineering(BSE)モジュールは、簡易的な成形シミュレーションツールです。ETA社の独自開発ソルバー「MSTEP」を搭載し、ブランク展開、ブランクレイアウト(歩留り計算)、トリムライン展開、Assemble BSEの4つの機能が含まれます。
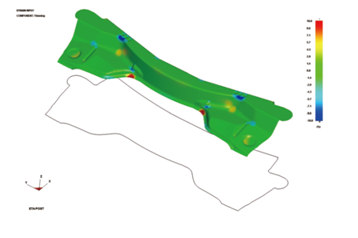
ブランク展開&簡易成形性評価
- 製品形状からブランクアウトラインの展開予測
- パッド圧/クッション圧設定可能
- 簡易成形性評価の自動レポート作成機能を標準装備

ブランクレイアウト(歩留り)計算
- 豊富なレイアウトテンプレートにより、効率よく歩留り率を最適化
- 狙った歩留り率を満足させるための部品形状を3Dラインで予測
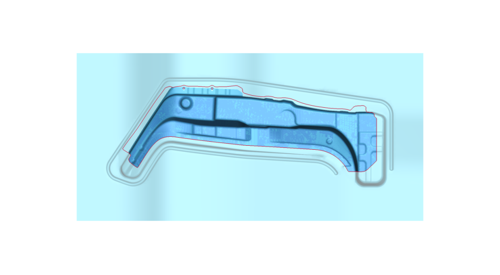
トリムライン展開
- 製品形状のフランジラインを金型形状面に自動展開
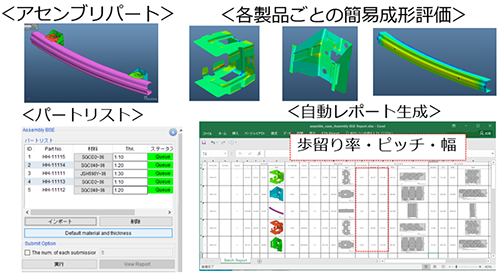
Assemble BSE
- 複数部品のアセンブリデータの一括バッチ処理
- ブランク展開・ブランクレイアウト(歩留り)の自動出力
<評価項目>
- 板厚減少率
- 板厚
- FLD(成形限界線図)
- 最大/最小主ひずみ
- 最大/最小主応力
多段階成形加工の結果
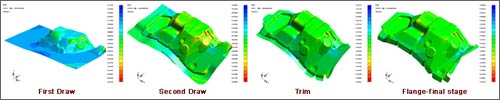
Dynaformでは多段階の成形をまとめて設定して自動的に各工程の解析を連続して実行することができます。 多段階成形としてのトランスファープレス、タンデムプレス、順送プレス(プログレ)を得意としています。 また、最終成形結果だけでなく各工程の成形結果を一括して確認することができます。 この事例では、1工程:深絞り成形(ドロー)、2工程:トリム、3工程:フランジングの多段成形です。 成形性評価として板厚減少率をコンタ図で示しています。 プレス成形における金型設計・工程計画の検討に役立ちます。
最適なプレス成形の検証
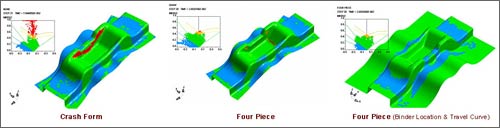
本事例は同一形状に対して方案検討を行った事例です。
各方案で FLD (Forming Limited Diagram) の結果を表示しています。 FLD 結果では、最大主ひずみと最小主ひずみの関係をプロットしたもので、成形時に割れ/シワの発生を予測することができます。
左の画像は上型・下型のみで構成されるクラッシュフォーム (バカ押し・素押し) で成形した結果で割れ発生の可能性が高いことがわかります 中央の画像はクラッシュフォームにシワ押さえを追加して成形した結果で改善されていますが割れ発生の可能性があります 右の画像は上型にパッドを追加して成形した結果で成形不良となる割れやシワが発生しないことがわかります。
プレス成形解析結果は金型設計に利用できるだけでなく、方案検討、工程計画にも活用できます。
試作とシミュレーションとの比較検証例
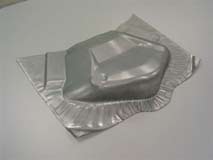
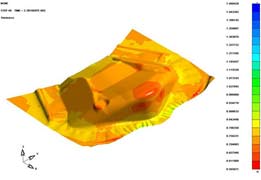
金属プレスシミュレーションではさまざまなトライをパソコン上で行うことができますが、実現象を再現できていなくては試作レスを果たすことはできません。
画像は試作とシミュレーションとの比較事例になりますが、画像右側のプレス成形解析 Dynaform の 結果では、シワの発生位置やスプリングバック量を忠実に再現できていることがわかります。
精度の高い金属プレスシミュレーション結果を得ることにより、金型設計へ結果を反映したり、スプリングバック結果を見越した金型見込みを行うことが可能です。
成形限界線図(FLD)
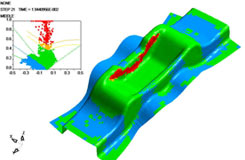
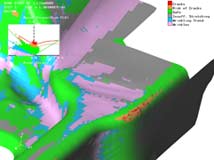
成形限界線図(FLD)では、最大主ひずみを縦軸にとり、最小ひずみを横軸としたグラフに、各部位で発生する主ひずみをプロットします。 材料特性値、板厚で算出される成形限界ライン(赤色)より主ひずみが高い部位では赤色でプロットされ、割れ判定となります。 また、FLDで表記される単軸圧縮ラインより下側でプロットされる部位は濃ピンク色で表示され、シワ予測と判定されます。 成形限界線図では、等2軸引張・単軸引張・単軸圧縮のラインが表記されているため、成形途中での各部位のひずみの方向を理解することができます。
板厚分布の解析結果
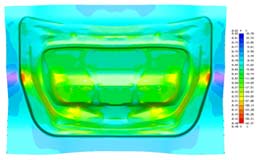
板厚変化率で板成形不良(割れ)を評価することができます。初期板厚(UT)、成形後の板厚を(T)とすると、板厚減少率は、(UTーT)/UT *100(%)で算出します。 成形不良(割れ限界)は、成形限界線図(FLD)で評価することもありますが、この板厚減少率の基準値で 判断することも多いです。一般に絞り加工は板厚が減少しやすくなり、この評価方法がよく用いられます。
ハイドロフォーミングのセットアップと解析結果
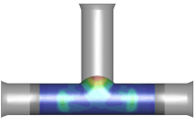
ハイドロフォーミング加工(バルジ加工)解析は、型締めした後、中空部品内部に液圧を負荷し、同時に両端を軸方向に押し込むことで成形します。 上図では、中空部品としてチューブのハイドロフォーミング加工例ですが、2枚の板材に適用することも可能です。
スプリングバック結果を考慮した金型見込みの自動化
AutoSCP機能により、金型見込み(SCP)を自動で複数回の実行が可能
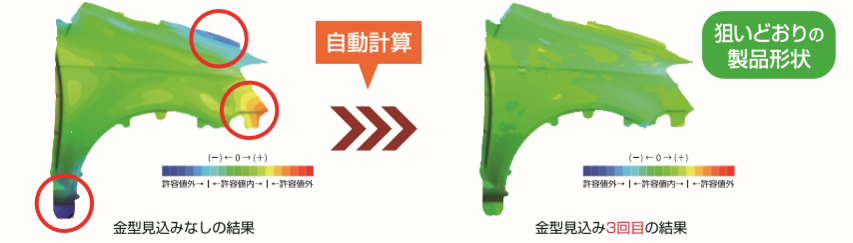
金型見込みの自動化の事例です 板成形では、プレス成形後にスプリングバックが発生し、製品の形状と成形後の形状が乖離してしまうことがあります。 スプリングバックが生じる変形をあらかじめ金型に見込んでおくなどの対応を行いますが、Dynaform の金型見込み機能では、スプリングバック解析結果を利用して、金型形状を自動的に修正します。 特に、自動車などで多く用いられているハイテン材料では、一度のスプリングバック見込み計算だけでは製品形状にあった金型形状を算出することが難しくなってきており、金型見込みを複数回自動化することにより精度の良い金型見込み形状を得ることができます。
ブランクアウトライン・トリムラインの最適化
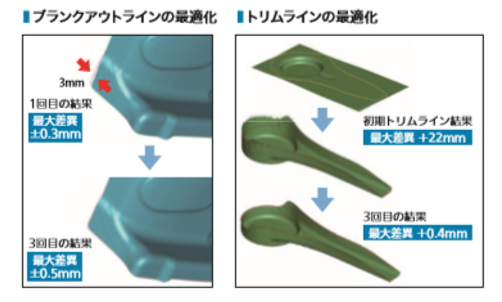
繰り返し計算を自動的に行うことにより、製品ラインと一致する最適なブランクのアウトラインあるいは最適なトリムラインを生成します。