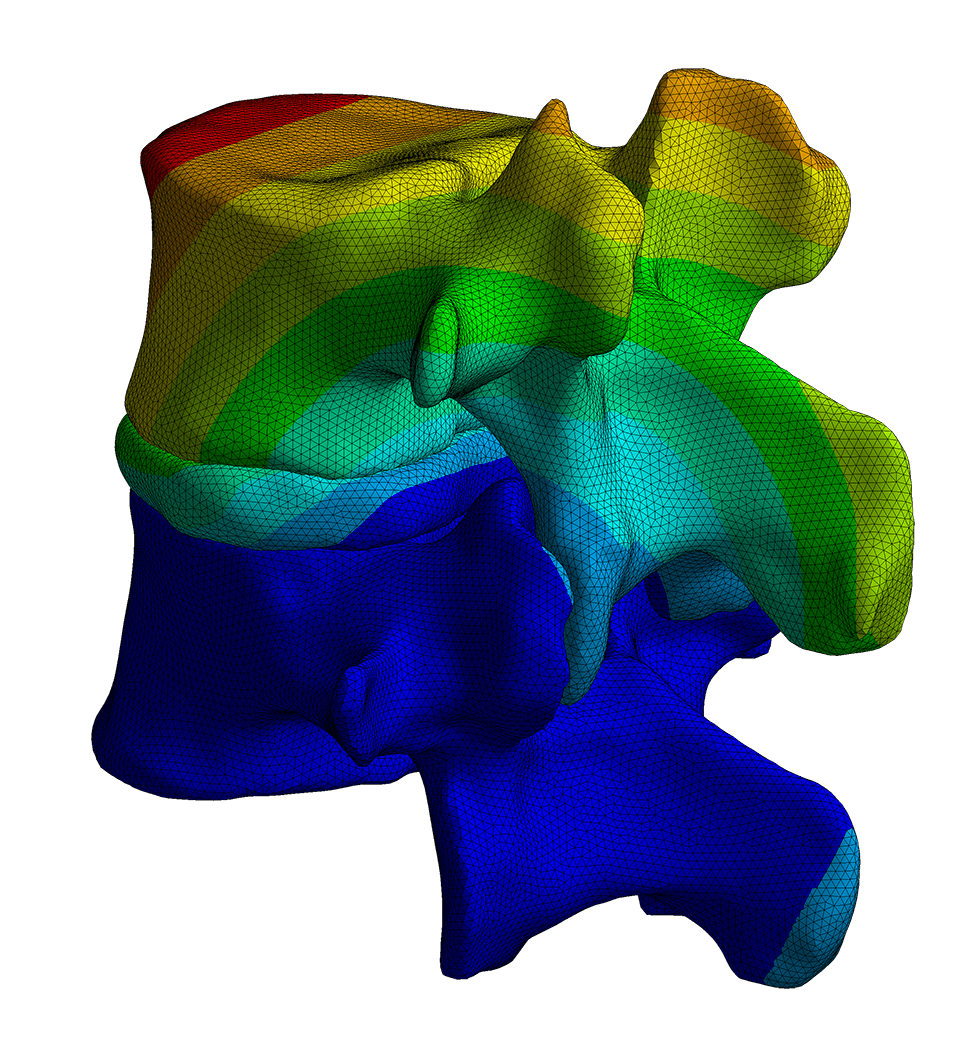
CASE STUDY
事例
解析分野、業界別の解析事例をご紹介
Ansys 事例の概要
Ansys に関連するさまざまな解析事例をご紹介します。自社における CAE 活用、または弊社「エンジニアリングサービス」での受託解析のご参考情報としてご活用ください。
各種事例は、[事例を検索する] より、分野、業界、使用ソフトウェアから絞り込めるほか、キーワード検索も可能です。
解析分野別から探す
業界別から探す
業界別 目次
事例インタビューから探す
事例インタビュー一覧へ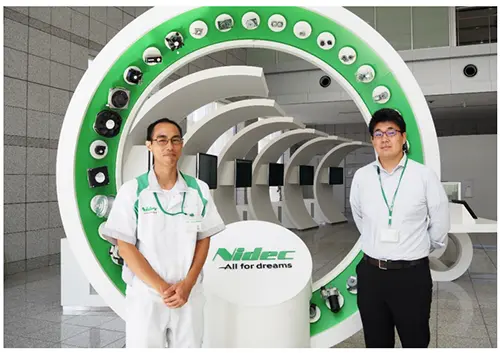
ニデック株式会社 様:Ansys Motor-CADで設計時間を50%削減。 磁気・熱・構造の連成解析で社内の技術レベルもアップ!
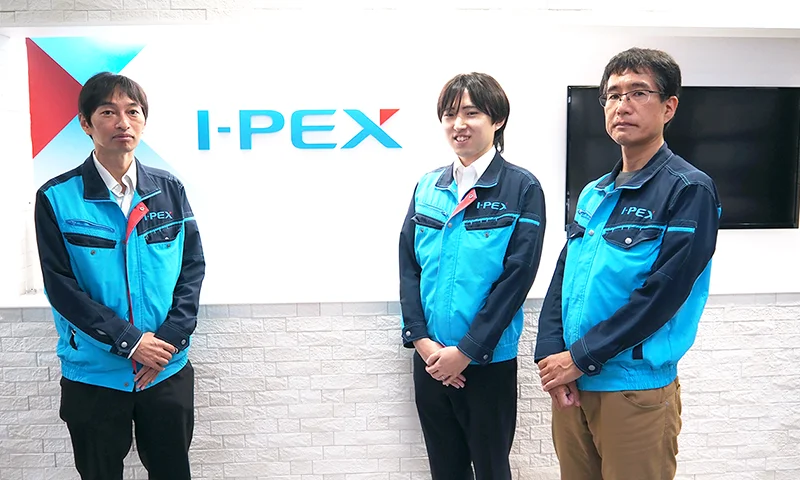
I-PEX 株式会社様:Ansysの活用で実測値に近い解析が可能に。開発のリードタイムも短縮
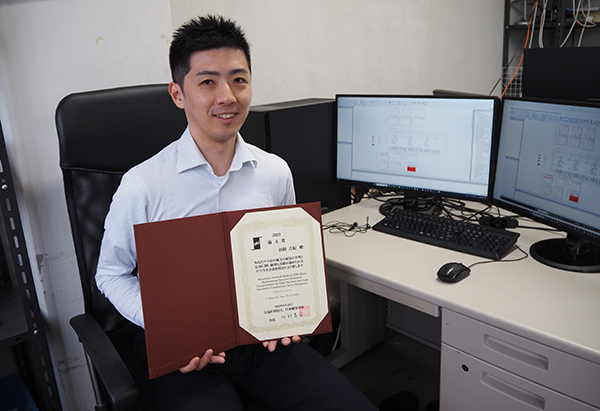
磁気ヒステリシス損を考慮したモータのモデル化を1D-CAE(Ansys Twin Builder)で可能に
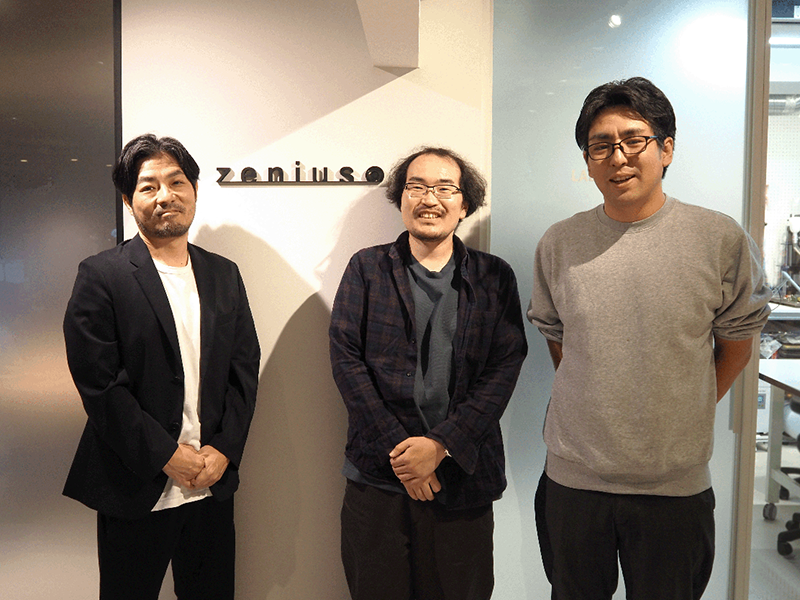
粉末吸入剤の流れと衝突を可視化し、 実証実験を重ねなくても薬効を保てるデバイスを開発
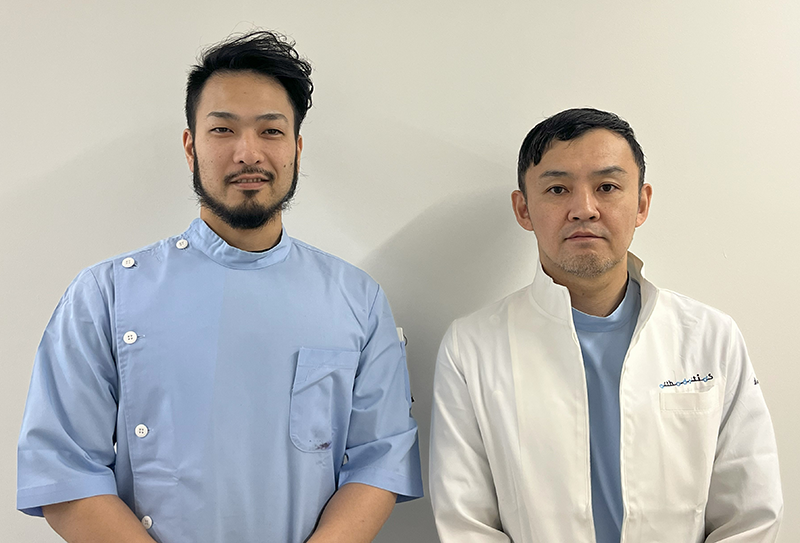
頭蓋骨と歯の矯正装置を3Dモデル化して解析、骨の広がり方を検証
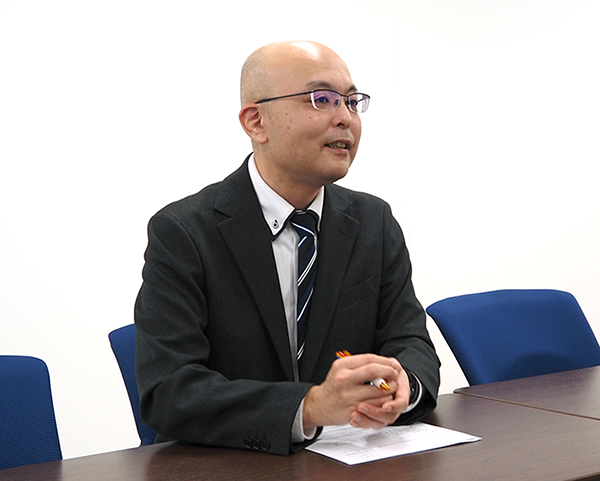