導入事例|資料ダウンロード
電気機器の製造データ分析によりリアルタイム監視による不良検知を実現
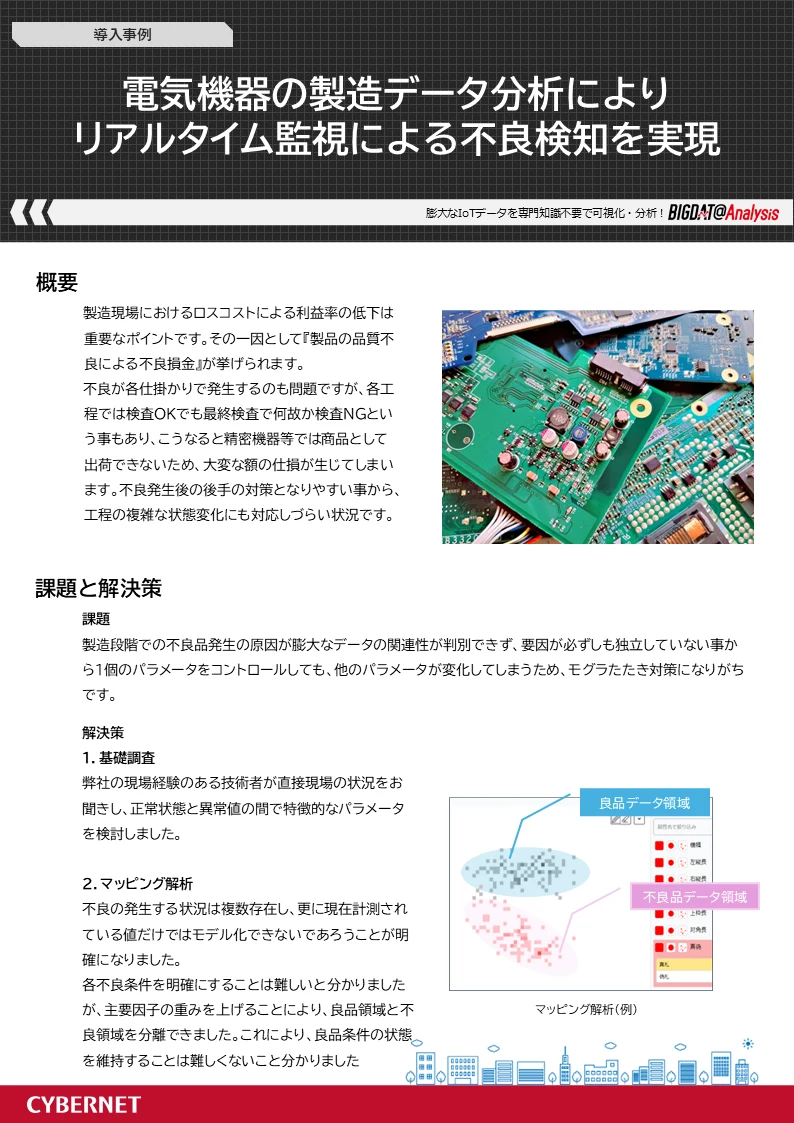
概要
製造現場におけるロスコストによる利益率の低下は重要なポイントです。その一因として『製品の品質不良による不良損金』が挙げられます。
不良が各仕掛かりで発生するのも問題ですが、各工程では検査OKでも最終検査で何故か検査NGという事もあり、こうなると精密機器等では商品として出荷できないため、大変な額の仕損が生じてしまいます。不良発生後の後手の対策となりやすい事から、工程の複雑な状態変化にも対応しづらい状況です。
課題と解決策
課題
製造段階での不良品発生の原因が膨大なデータの関連性が判別できず、要因が必ずしも独立していない事から1個のパラメータをコントロールしても、他のパラメータが変化してしまうため、モグラたたき対策になりがちです。
解決策
1.基礎調査
弊社の現場経験のある技術者が直接現場の状況をお聞きし、正常状態と異常値の間で特徴的なパラメータを検討しました。
2.マッピング解析
不良の発生する状況は複数存在し、更に現在計測されている値だけではモデル化できないであろうことが明確になりました。
各不良条件を明確にすることは難しいと分かりましたが、主要因子の重みを上げることにより、良品領域と不良領域を分離できました。これにより、良品条件の状態を維持することは難しくないこと分かりました
*続きはダウンロードしてお読みください。