資料ダウンロード|分野別ソリューション
実使用を考慮したブレーキ鳴き現象の最適化
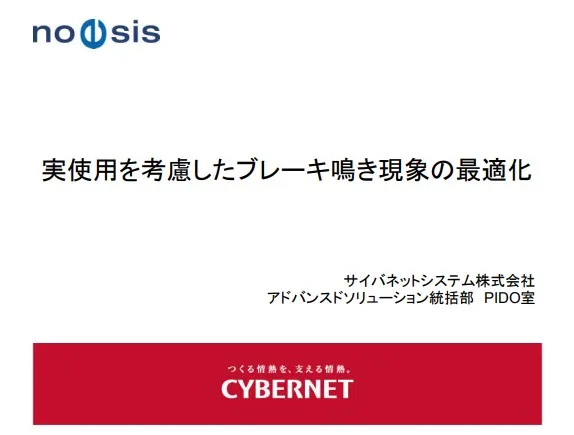
以前弊社が発表した論文“ブレーキ鳴き現象モデルの最適化”では、ブレーキ鳴き問題を検証する為、ディスクブレーキを3次元CAD(ANSYS WB)でモデル化し、有限要素解析の複素固有値解析を実施する事でブレーキ鳴きの最小化を目的とした最適化をOptimusを使用して実施しました。本事例では、同一のモデルを使用し、製造工程での寸法誤差、実使用においての気温、湿度の変化といった不確定要因を考慮したロバスト・信頼性設計の各手法による結果の比較及び考察をします。
製造工程での寸法誤差
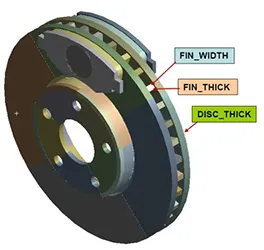
工場での製造における寸法誤差を考慮して、ディスクの厚さ、フィンの厚さ+幅に分布(正規分布)を定義します。上下限値に最適化計算で使用した範囲を設定し、分布の標準偏差は工程能力指数(Cp)より算出します。工程能力指数とは、工程が規格を満足する製品を出しているかの判断基準であり、Cp=1.0の時、分布の平均値から±3σが上下限規格値である事を意味しています。 (今回は1.33を使用)
制約の設定(信頼性)
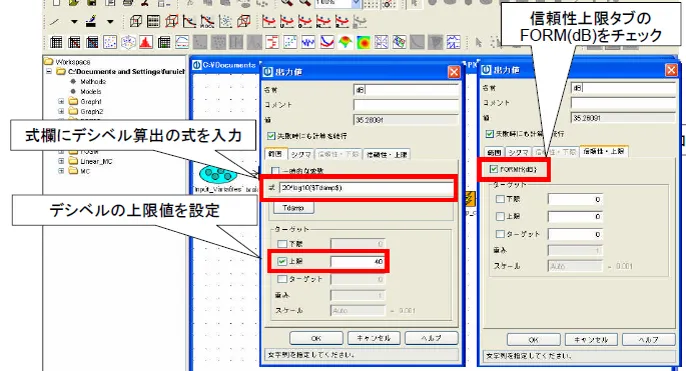
信頼性設計のため、目的関数である「減衰の最小化」に制約を設定します。減衰の値自体に制限値を設けるのは難しい為、減衰の値をデシベル(dB)に変換し制約を設定し、その制約を超える確率を算出します。
制約の設定(ロバスト性)
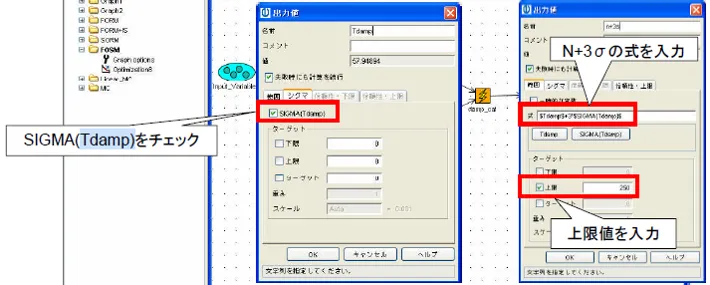
Optimusに搭載されているロバスト性の手法では出力値の分布の標準偏差(σ)を算出しロバスト性の評価及び最適化を実施する事が可能です。ロバスト性を考慮した最適化計算では複数のアプローチが考えられますが、今回は基準値+3σの値を新たに出力値として制約と共に設定し評価指標とします。
各最適化手法の比較
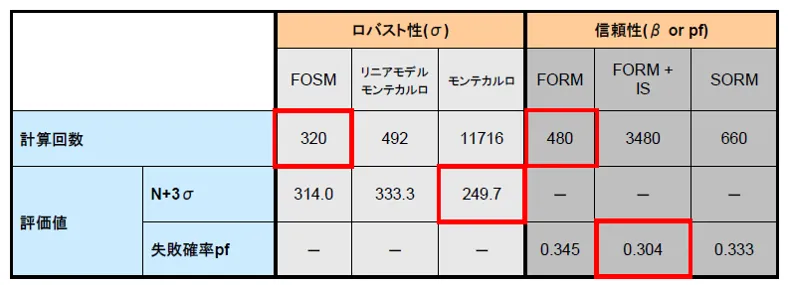
結果を見ると、ロバスト性の手法ではモンテカルロ、信頼性の手法ではFORM+ISの手法の解が最適であることがわかります。しかし、この2手法は他の手法と比較して計算回数が非常に多い為、ロバスト性ではFOSM、信頼性ではFORMの手法が多少精度は落ちるものの計算回数が少なく有効である事が確認できました。また、最適化計算ではOptimusの優れた機能のひとつである分散処理を使用しました。
工程能力指数Cpの算出と評価
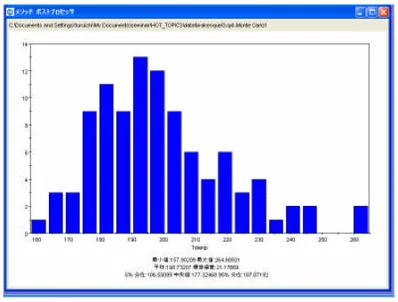
出力値の工程能力指数Cpを算出し、評価を行います。図は、モンテカルロの計算結果を用いた結果を表しています。Cpが1以上であり、工程能力は十分といえます。
*続きはダウンロードしてお読みください。