製品・サービス
製造現場に求められる「リアルタイム性」と「改善力」を推進
ThingWorx RTPPM (Realtime Production Performance Monitoring)
「現場を止めない」「成果を逃さない」ための第一歩
近年の製造業では、市場ニーズの多様化、短納期化、要求品質の高度化に加え、エネルギー価格の高騰や人材不足といった厳しい経営環境にさらされています。
こうした中で企業に求められているのは、コストや品質の管理だけでなく、「リアルタイムな状況把握」と「データドリブンな即時の意思決定」によって、継続的な現場改善を推進する力です。
しかし、現実の製造現場では
- 設備ごとの稼働状況は手集計かつ、シフト毎、日毎の粒度でしか管理されていない
- 実際の停止理由や廃棄要因を把握するには現場に張り付いて調査する必要がある
- KPIは集計ベースでしか可視化されず、対応が常に「後追い」になる
といったように、データはあるのに“活かされていない”状態が大きな課題となっています。これにより、本来改善することが可能なロスや非効率な生産が放置され、「隠れた損失」が積み重なっていきます。
ThingWorx RTPPMとは?
こうした課題に対応するのが、ThingWorx RTPPM(リアルタイム・プロダクション・パフォーマンス・モニタリング)です。RTPPMは、現場の生産設備や製造ラインからリアルタイムに取得されるデータを活用し、生産状況や設備のパフォーマンスを即座に可視化・分析するためのアプリケーションで、OEEをはじめとする生産KPIの定量的把握と改善活動の促進をサポートします。
製造現場では、生産ロスの要因を迅速に特定し、対応するための「即時性」と「可視化」が不可欠です。RTPPMは、総合設備効率(OEE)や停止時間、およびアラーム発生などのKPIをわかりやすくダッシュボードで表示し、作業者・管理者の双方にとって判断しやすい情報を提供します。
ThingWorx RTPPMは、単なるモニタリングツールではなく、現場の気づきを生み出す“改善のためのプラットフォーム”です。
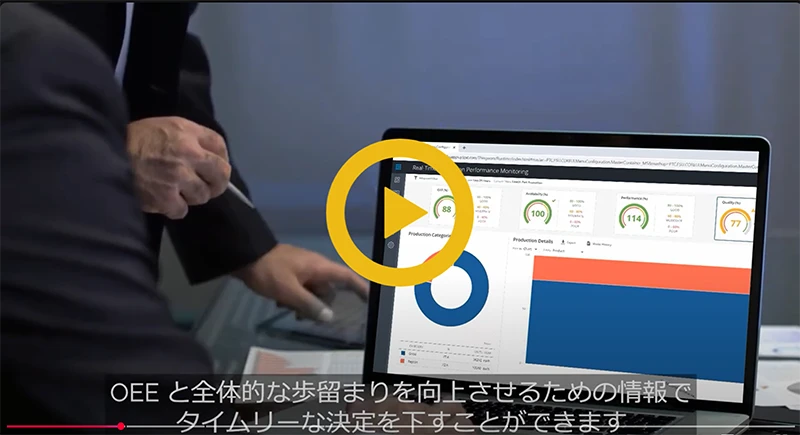
ThingWorx RTPPM紹介動画
現場のこんなお悩み、ありませんか?
1.「なぜ止まった?」が分からない ―停止・異常の原因把握が進まない
- 停止や異常の理由が曖昧で、真の原因が特定できない
- 設備のどこにどれだけの無駄があるか分からず、改善の優先順位が立てられない
- 担当者によって判断基準が異なり、現場の意思決定が属人的になっている
- 現場からの報告だけでは、定量的な裏付けが得られない
2. データはあるのに活かせない ― 情報活用の仕組み・時間が不足
- データは存在するが、活用する仕組みや時間がない
- KPIを定義してもリアルタイムでの活用が難しく、後手の対応になってしまう
- システムや指標の取り方が拠点ごとに異なり、全体最適の妨げになっている
3. 現場にフィットしない仕組み ― 柔軟性・拡張性への不満
- 既存のシステムでは柔軟な分析が難しく、カスタム対応に多くの費用と工数がかかる
- 設備・製品・工程ごとの固有事情にフィットしない画一的な仕組み
- ダッシュボードやレポートを毎回手作業で作成しており、属人化している
ThingWorx RTPPMの特長とメリット
ThingWorx RTPPMは、製造現場のパフォーマンスをリアルタイムに可視化し、改善活動の即時性と継続性を飛躍的に高めます。また、テンプレートパッケージならではの即効性と柔軟性も兼ね備えています。ここでは、RTPPMの3つの特長と導入によるメリットも合わせてご紹介します。
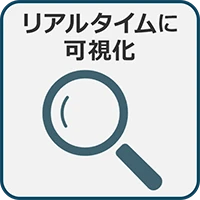
1.生産性と品質の“今”をリアルタイムに見える化
現場の状況をリアルタイムで把握し、迅速な判断と対応が可能になります。これにより、損失・停止の要因を即時に特定、改善のスピードを加速させます
- OEE・MTTR・MTBF・稼働率などのKPIを即時に可視化
- ダッシュボードやグラフを通じて、現場の状況を直感的に把握
- フィルタ・ドリルダウンで詳細な傾向分析が可能
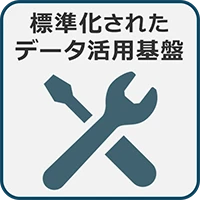
2.改善活動に“根拠”を与えるデータ活用基盤
データに基づくデータドリブンな改善サイクルが確立され、“勘と経験”から脱却できます
- 根本原因分析(RCA)に必要な停止・不良・歩留りなどのデータを一元的に収集・分類
- 担当者任せにせず、標準化された環境で共通認識を醸成
- KPIの履歴や影響分析により、改善の優先順位付けが可能
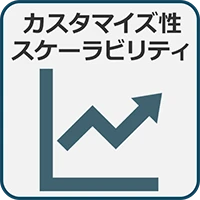
3.小さく始めて大きく育てる ― コスト・運用・拡張性を両立
スモールスタートから全社展開まで、お客様の状況に合わせて段階的な展開が容易です
- すぐに使えるテンプレート構成で、初期構築の費用と工数を最小限に抑制
- 設備・工程・ユーザーに応じた柔軟なカスタマイズや運用が可能で、定着・活用を支援
- 他のThingWorxパッケージやシステムとの連携・拡張や、将来的な機能追加・他アプリとの連携も容易
主な機能
KPIダッシュボード:OEEをはじめとする主要指標をリアルタイム表示
- OEE・MTBF・MTTR・OOEなどの主要KPIをグラフィカルに表示
- 日付、設備、製品、シフトなどでドリルダウン・フィルタリングが可能
- KPIの経時変化を確認し、傾向や異常値を把握
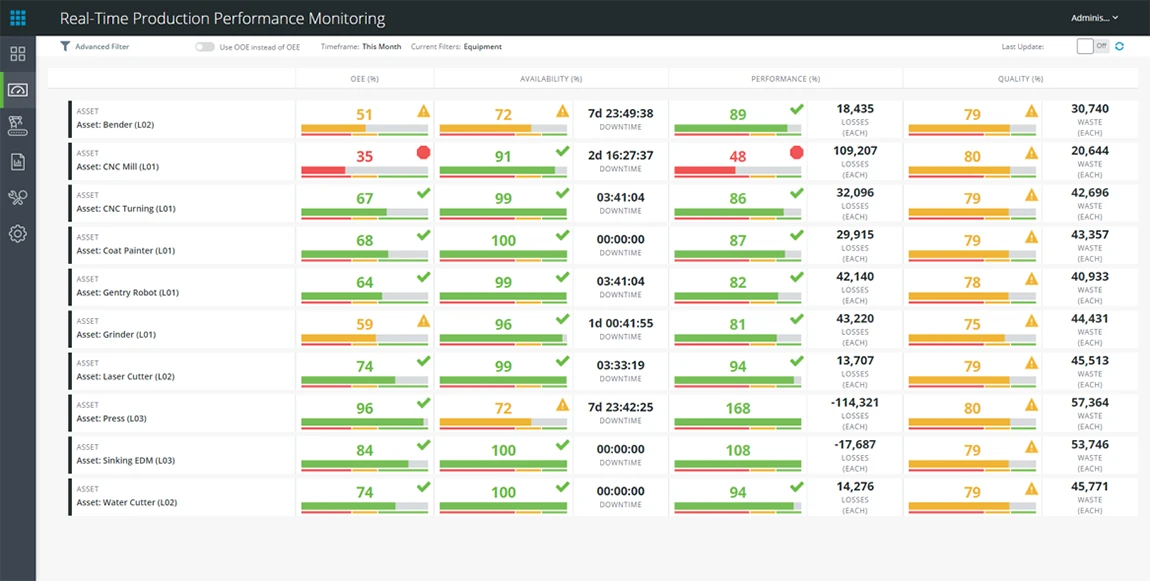
KPIダッシュボード
ダウンタイム分析:停止の原因を多角的に可視化
- 停止時間・回数別の理由コードをパレート図形式で分析
- 「どの設備で」「どんな理由で」「どのくらい」停止したかを明確化
- フィルタ条件に応じて特定シフト・製品・作業指示別の可視化も可能
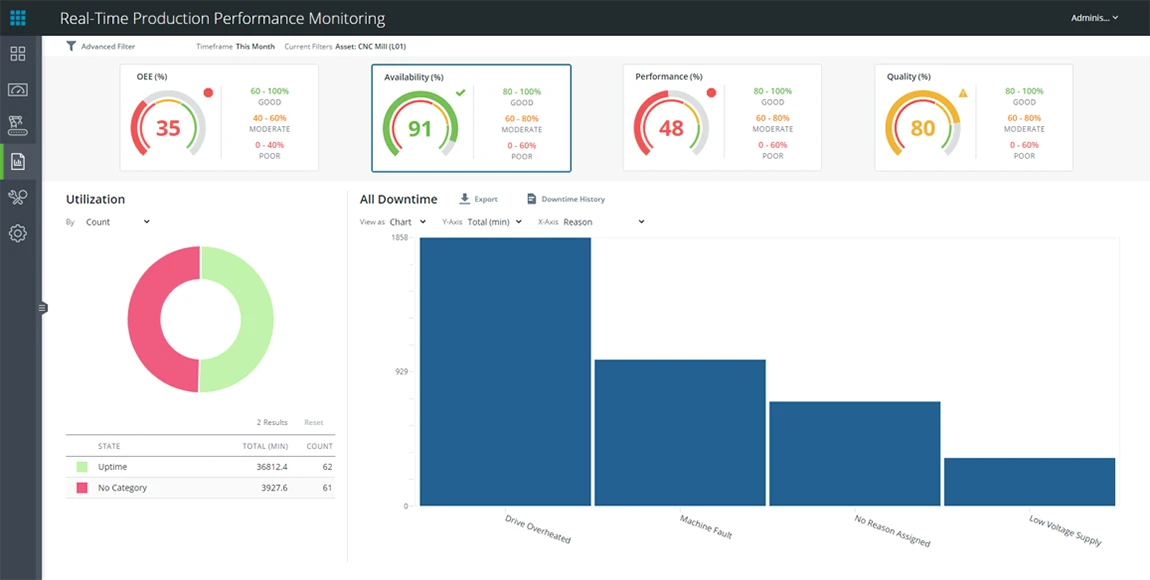
パフォーマンス分析:理想速度とのギャップを可視化
- 理想サイクルタイムに対する、実パフォーマンスを比較分析
- 製品・ライン・時間帯別の傾向把握と原因分析を支援
- 実行率が下がっている要因を特定し、改善へつなげる
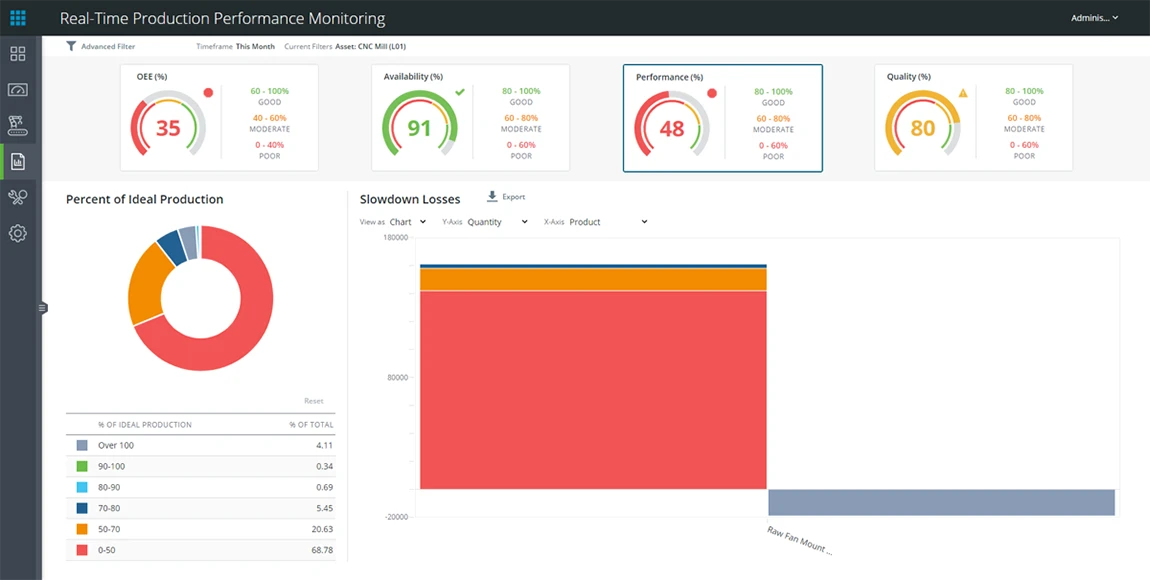
品質分析:廃棄・不良の要因と傾向を追跡
- 廃棄理由や不良内容を可視化し、分類別の割合を分析
- 生産品目や工程別にフィルタし、品質ロスの根本原因を特定
- 廃棄のトレンド・比率を把握し、改善計画の優先順位づけに貢献
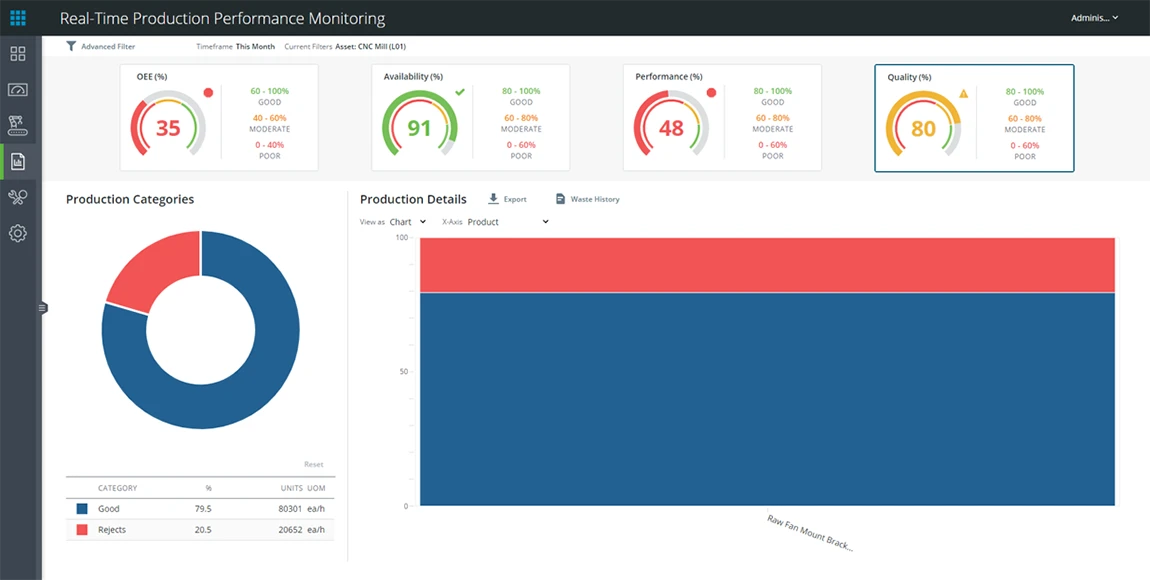
レポート・データ出力:分析結果の共有・再利用をサポート
- KPI・イベント・ダウンタイムなどの各種データをCSV形式でエクスポート可能
- 独自レポートや他システム連携に活用できる柔軟な出力機能
- ExcelやBIツールへの展開も容易で、レポート作成の効率が大幅に向上
ユースケース紹介
ケース1:ライン停止の原因を特定し、改善につなげたい
- 課題
生産ラインが1日に数回短時間停止しているが、原因が不明確で現場も対応できていない。現場報告書と実際の状況に乖離があり、改善が進まない。
- 活用のポイント
- 各停止の発生タイミングと理由コードをリアルタイムで記録
- 停止時間・回数ごとのパレート分析により“真のボトルネック”を可視化
- シフト別・製品別の傾向を把握し、メンテナンス要因やオペレーション改善に活用
- 想定される効果
- 各種レポートから停止原因の特定ができた事で適切な対策の実施
- 可視化される事でデータを元に改善活動が行えるようになり、部門間の連携も円滑
ケース2:製品別の歩留まりを分析し、品質改善へ活かしたい
- 課題
特定の品目で不良率が高いが、どの工程・時間帯に問題があるのか分からない。紙帳票やExcelベースの管理では手間がかかりすぎて分析が困難な状況にある。
- 活用のポイント
- 廃棄理由・不良要因をリアルタイムで記録、分類
- 品番・工程・シフト別に廃棄の傾向を可視化
- KPIレポートをCSV出力し、品質管理部門との連携に活用
- 想定される効果
- 特定工程に偏った廃棄が明確になり、作業手順の見直しで歩留まりが向上
- データ出力で月次レポート作成も自動化、報告業務の負荷が軽減
ケース3:複数拠点の稼働状況を統一指標で比較・管理したい
- 課題
拠点ごとに異なるシステム・帳票で管理されており、全社的な稼働状況の比較ができない。経営層がリアルタイムに全体状況を把握できず、改善施策も属人的になっている。
- 活用のポイント
- 全拠点共通のKPI(OEE, MTBF, 可用性など)をテンプレートで表示
- 拠点別・ライン別に稼働状況を横並びで可視化
- 拠点間でベストプラクティスの共有が可能
- 想定される効果
- 共通の可視化指標により現場の“共通言語”ができ、全社的な改善文化が促進
- 経営層もKPIをもとに各拠点に具体的なフィードバックが可能
活用事例
自動車部品メーカー:グローバルの生産拠点に“統一基準の見える化”を導入し、変革のスピードを加速
課題
- 拠点や部門ごとに異なるシステムが使われており、現場データの収集・統合が困難
- 多様な工場の稼働状況を標準化された視点で比較・評価する仕組みが無い
- 分析・改善のためのデータ活用が属人化しており、全社横断的な最適化が進まない
活用のポイント
- 標準化されたダッシュボードとKPIで、全社共通の“見える化”基盤を構築
- 拠点ごとに異なる設備・工程にも柔軟に対応できるテンプレート構成を活用し標準化
- 各拠点の設備稼働状況をクラウド上で統合的に可視化
効果
- グローバルで共通のデータ定義と分析軸が整備され、拠点間の横展開とベンチマークを実現
- 各製造拠点におけるOEEや稼働状況をリアルタイムかつ共通指標で把握可能
- データドリブンな改善文化の醸成が進み、“標準化された可視化”が全社的な変革の土台へ定着